- Joined
- Nov 12, 2009
- Messages
- 1,427
- Reaction score
- 221
Hi Guys
Well It has been a bit of a eye opener that's for sure, as at first glance Castings look so easy :big:
I must admit though that a nice Flywheel casting is a wonderful thing and makes life really easy
I had to do a fair bit of work to get a clear path for my new Rods but as of today we have the Crank and rods Rotating assembly even if it does still need cleaning up.
I then drilled the 7/64 cross hole for the Throttle assembly unfortunately the smallest mill bit I have, seems to be 1/8 so I may have to put finishing the part off for a while.
The part is slotted up to the cross hole from the venturi from opposing directions on either side if that makes any sense, to allow the throttle to open and close with the cross bar installed.
After drilling the cross hole I'm starting to wonder about my choice of Stainless for the throttle, I just hope it slots 7/64 OK
Pete
Well It has been a bit of a eye opener that's for sure, as at first glance Castings look so easy :big:
I must admit though that a nice Flywheel casting is a wonderful thing and makes life really easy
I had to do a fair bit of work to get a clear path for my new Rods but as of today we have the Crank and rods Rotating assembly even if it does still need cleaning up.
I then drilled the 7/64 cross hole for the Throttle assembly unfortunately the smallest mill bit I have, seems to be 1/8 so I may have to put finishing the part off for a while.
The part is slotted up to the cross hole from the venturi from opposing directions on either side if that makes any sense, to allow the throttle to open and close with the cross bar installed.
After drilling the cross hole I'm starting to wonder about my choice of Stainless for the throttle, I just hope it slots 7/64 OK
Pete
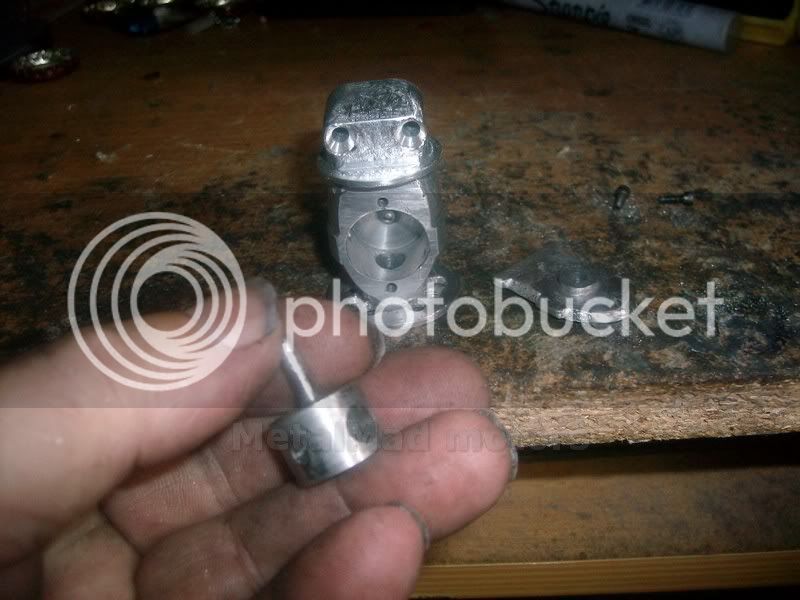