This is what was wrong with my lathe One picture is of the gear cover that sets on the end of my lathe to protect my fingers from the gears. Notice the bent bracket at the lower right corner of it. That bent bracket pushes on a switch which disables the electrics on the lathe if the guard is removed. I haven't had that cover off the lathe in more than a year. Somehow---Perhaps metal fatigue? the bracket bent far enough that it no longer pushed on the button, and consequently the lathe stopped right in the middle of a cut. The switch it presses on is right below the gears and is virtually impossible to see unless you stand on your head to look for it. When I left the lathe in Concord at Busy Bee, I told them that my rpm indicator only worked intermittently and please either fix it or replace it, as well as please fix whatever is wrong that I have no power to the lathe. They replaced the rpm indicator, scratched their heads a bit and then found that bending the bracket by hand fixed things so it pushed the button and restored power to the lathe. I either didn't know, or else forgot that switch was even there.They charged two hours labor and the price of the new readout. My bill came to $129. So, they treated me quite honestly I think. They could have told me it needed a new motor and charged me another couple of hundred dollars but they didn't.
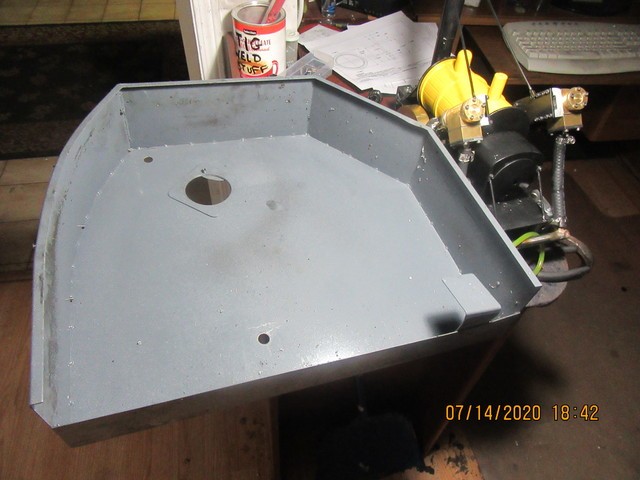
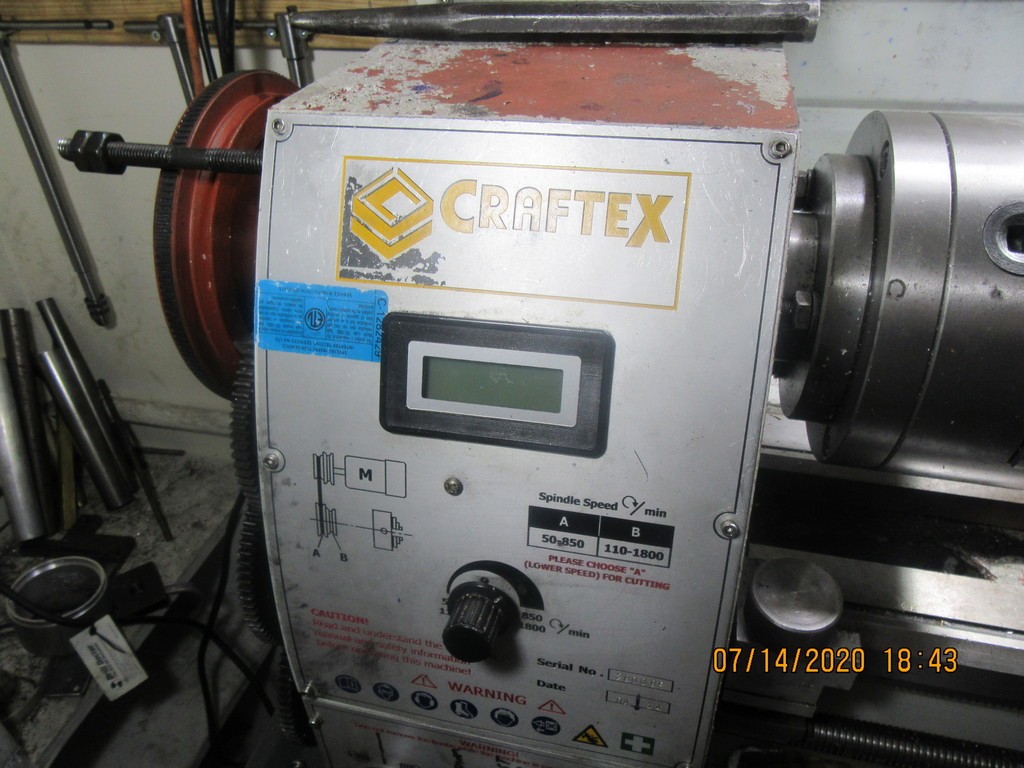