Hello All!
Made a bit more progress today. Chucked up the rear pieces and started to finish them up. I used my "bat wings" (brass inserts) on the jaws so i wouldn't damage the finish. Indicated to less than .001
I turned the shaft down to about .010 over size and then got the tail shaft ready for threads.
Ran the threads on.
Finished the shaft to .0005 - .001 oversize and then i like to bring the shaft to size using some 320 sand paper. This way I can work the taper out if there is any and i can usually hit my number within a few tenths.
Then I put the taper on last.
Thats about all until I get my hands on a 5/16 collet.
Made a bit more progress today. Chucked up the rear pieces and started to finish them up. I used my "bat wings" (brass inserts) on the jaws so i wouldn't damage the finish. Indicated to less than .001
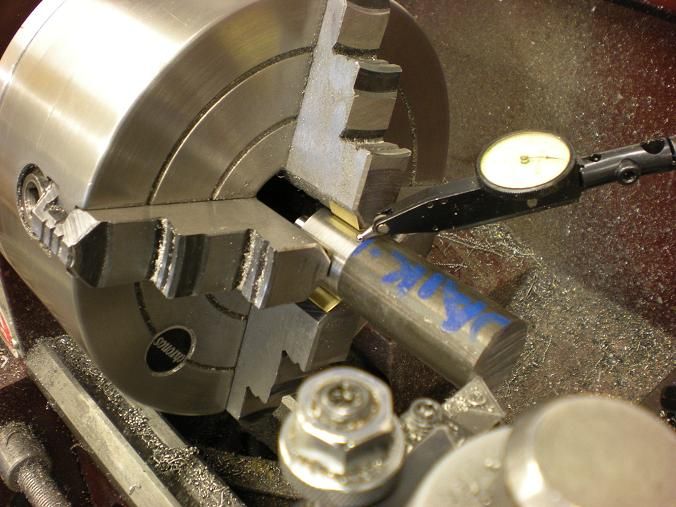
I turned the shaft down to about .010 over size and then got the tail shaft ready for threads.
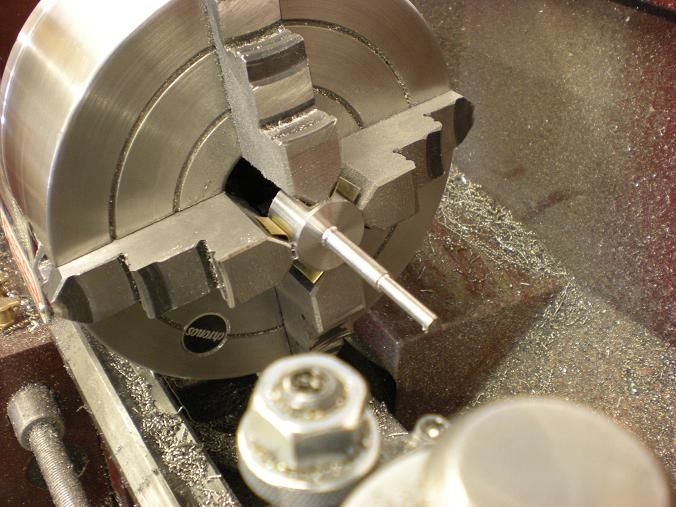
Ran the threads on.
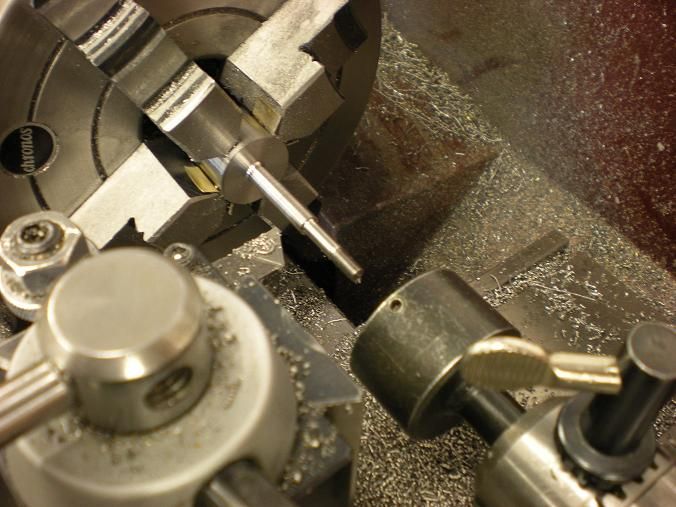
Finished the shaft to .0005 - .001 oversize and then i like to bring the shaft to size using some 320 sand paper. This way I can work the taper out if there is any and i can usually hit my number within a few tenths.
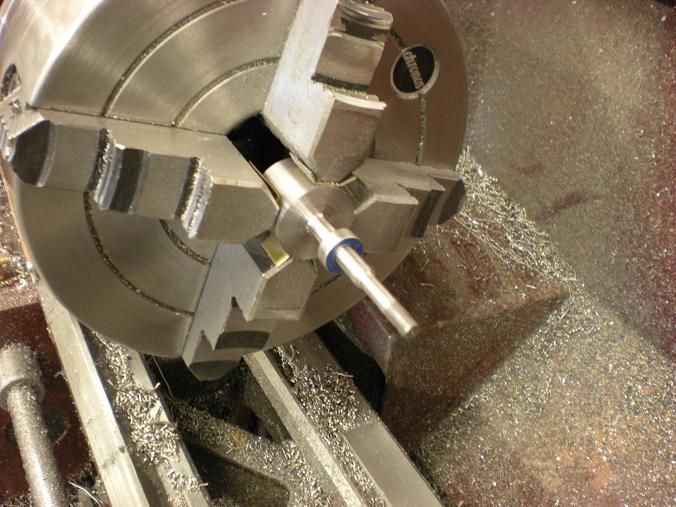
Then I put the taper on last.
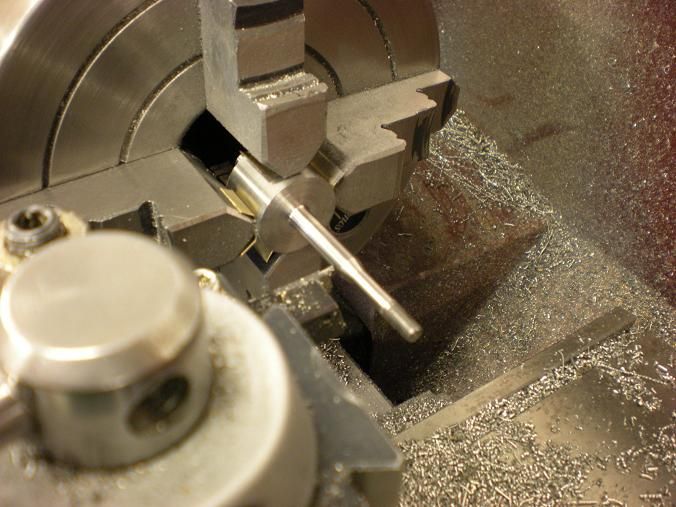
Thats about all until I get my hands on a 5/16 collet.
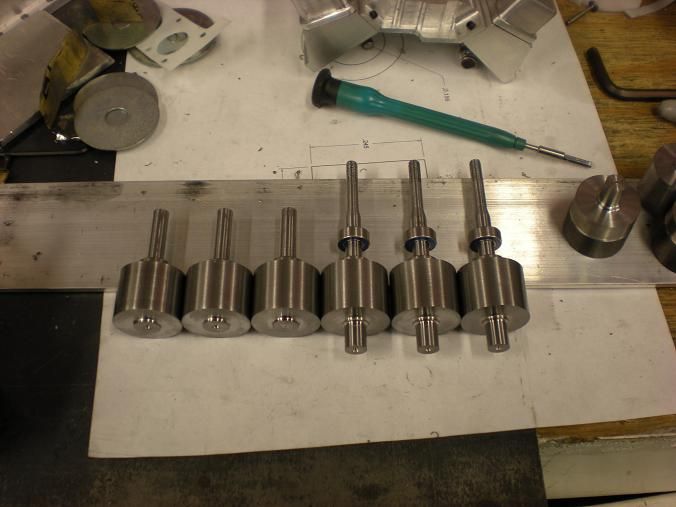