- Joined
- Dec 2, 2008
- Messages
- 971
- Reaction score
- 9
It has officially started. I cut some material. The plans are almost finished and will likely change as I get into it but I started sizing up material. In case you have not read my post in the break room about diversion, here is where I am headed.
If all goes well the end result will be a double acting vertical twin with Stephenson reversing gear. It will have a bore and stroke of 5/8" x 1" with trunk style x-heads. The cylinders will be a brass fabrication of pipe and plate. The support legs and trunk guide will be a one piece aluminum turned on the lathe (one for each cylinder) to approximate the appearance of a casting. The crankshaft will be built-up with stainless shaft and journals and brass webs. The base will be one piece of aluminum with efforts to simulate a casting.
I started out with a piece of aluminum bar 1 3/8" x 2" x 22". I convinced myself that this was not much different than very hard wood so I took it to the table saw a ripped it to 1.125" x 2". Really. No problem. It actually cut cleaner than a lot of soft wood that I have worked with. No pinching in the kerf and no burning. I wasn't much concerned about the surface finish since it would be removed by later processes, but the result was better than a lot of band saw cuts I have seen. I then cross cut it to length + .125" for the base and supports. Here is the stock cut to size.
The 3/16" slab that the parts are sitting on is the off cut from the ripping operation.
The next step was to drill centers on each end for setting up in the lathe. In the lathe, the top end was turned to a 1" diameter for a length of 1.5" I also turned the bottom section to 2" dia. (just taking of the square) except for the last 1/8" for the foot mounting which is left square.
Wow! What is this stuff? It's like no aluminum I have ever seen. It cuts clean. It sings almost like brass when it is cutting. and it produces uniform coma shaped chips and leaves fine finish!!!
I have to make a boring bar for the inside of the legs so that's for tomorrow.
Jerry
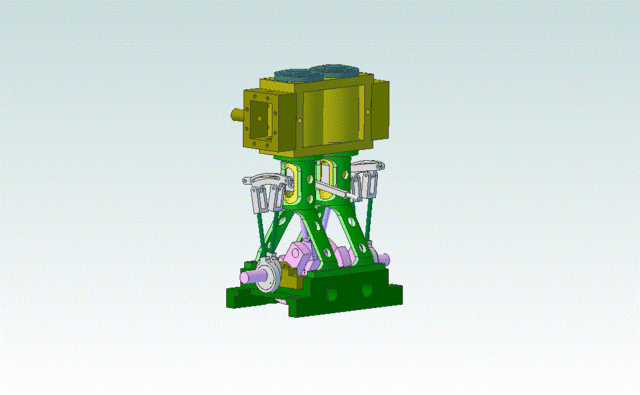
If all goes well the end result will be a double acting vertical twin with Stephenson reversing gear. It will have a bore and stroke of 5/8" x 1" with trunk style x-heads. The cylinders will be a brass fabrication of pipe and plate. The support legs and trunk guide will be a one piece aluminum turned on the lathe (one for each cylinder) to approximate the appearance of a casting. The crankshaft will be built-up with stainless shaft and journals and brass webs. The base will be one piece of aluminum with efforts to simulate a casting.
I started out with a piece of aluminum bar 1 3/8" x 2" x 22". I convinced myself that this was not much different than very hard wood so I took it to the table saw a ripped it to 1.125" x 2". Really. No problem. It actually cut cleaner than a lot of soft wood that I have worked with. No pinching in the kerf and no burning. I wasn't much concerned about the surface finish since it would be removed by later processes, but the result was better than a lot of band saw cuts I have seen. I then cross cut it to length + .125" for the base and supports. Here is the stock cut to size.
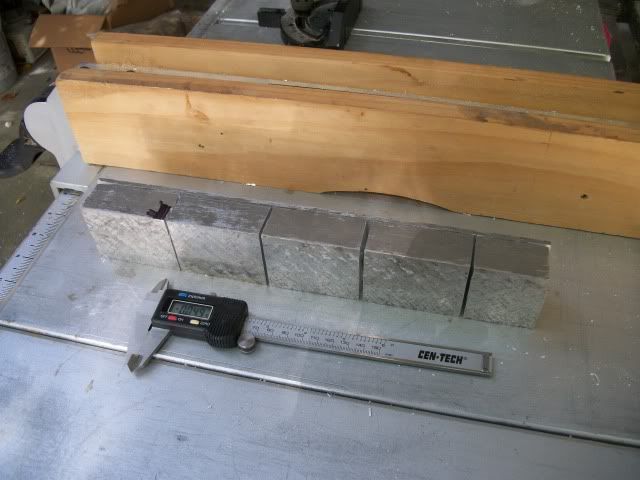
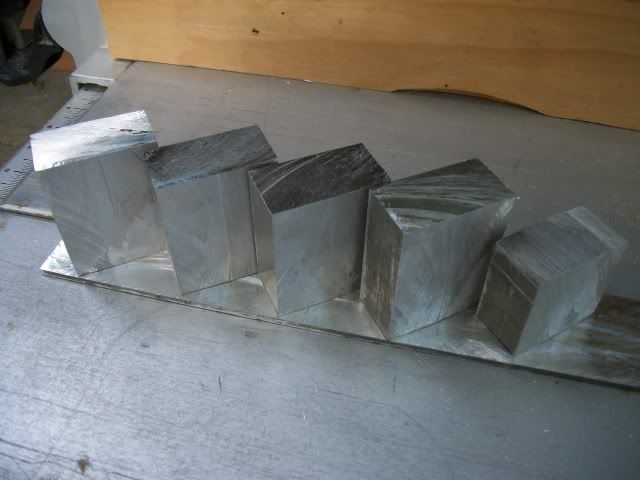
The 3/16" slab that the parts are sitting on is the off cut from the ripping operation.
The next step was to drill centers on each end for setting up in the lathe. In the lathe, the top end was turned to a 1" diameter for a length of 1.5" I also turned the bottom section to 2" dia. (just taking of the square) except for the last 1/8" for the foot mounting which is left square.
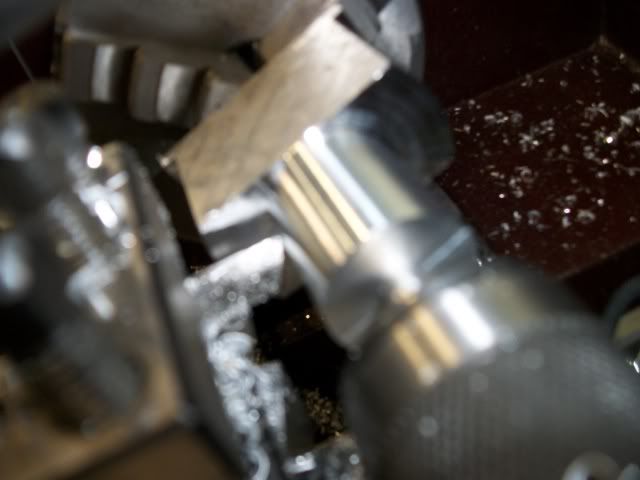
Wow! What is this stuff? It's like no aluminum I have ever seen. It cuts clean. It sings almost like brass when it is cutting. and it produces uniform coma shaped chips and leaves fine finish!!!
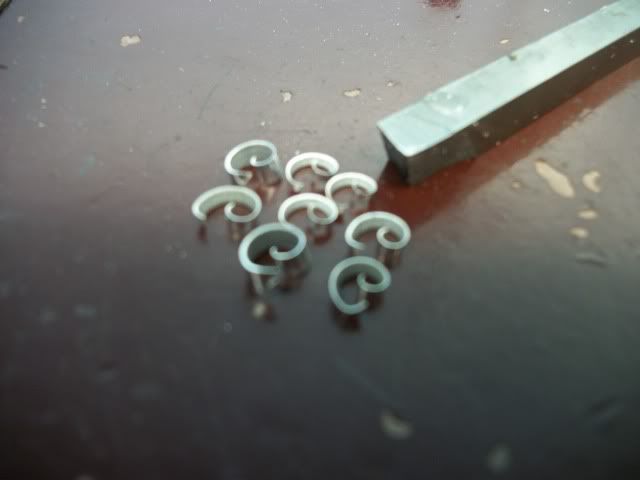
I have to make a boring bar for the inside of the legs so that's for tomorrow.
Jerry