This is a rather dreadfull picture, in which I was attempting to show the 3 bores in the cylinder housing (water jacket). I drilled though with progressively larger drills, starting with 5/16" and ending with 3/4", which was the largest drill I have. This was stretching the limit of what my small mill will do without blowing a fuse, and it was compounded by the fact that my quill travel is only 2", while I was going through material 2 1/2" thick. --this meant a lot of running the head up and down the column as well as using the full quill travel. I used my boring head to go all the way through at 0.950, knowing that if I didn't get it dead on 0.950. I would be turning the outside diameter of the cylinder and could turn it 'to suit". The 1.00 diameter c'bore x 1/8" deep presented no problem. But when I got to the large c'bore about 1/3 of the way down the bore, I thought----Hmmmm---How the heck do I do that??? I zeroed out my depth vernier on the mill, cranked the offset on the boring bar down to a point where it would fit into the bore, ran the quill down to 1.125", backed off the advance screw on the boring head untill I could just feel the boring tool touching the inside wall of the bore (All this of course with the machine turned off), For every full turn of the adjusting screw, my boring bar advances 0.100"---So---I advanced it 1/4 turn which of course created big interference with the inside of the bore, then turned the quill by hand untill I had one full revolution completed, then turned the mill on at very low speed and gradually increased the speed untill it was turning without dragging, then repeated the process untill I had reached the bore which I wanted 1.311". Of course I had no way to measure this, s I was counting divisions on the tiny dial on my boring head. About this time, I began to realize that I should have done this in the four jaw chuck in the lathe. Oh well, live and learn!!! Once I reached the desired diameter, I measured the length of carbide on a similar boring bar and seeing as it was 0.25", I set the mill for a mid range RPM and backed the quill up 1/4" to give a counterbore 1/2" long as per the drawing for a water passage. I certainly don't recomend this method to anyone else. It works, but its kinda like wiping your a$$ with your elbow!!! It should have been done in the lathe using the 4 jaw chuck. Oh well, I "Goterdone" and its all hidden when everything is assembled. I'll know better next time!!!
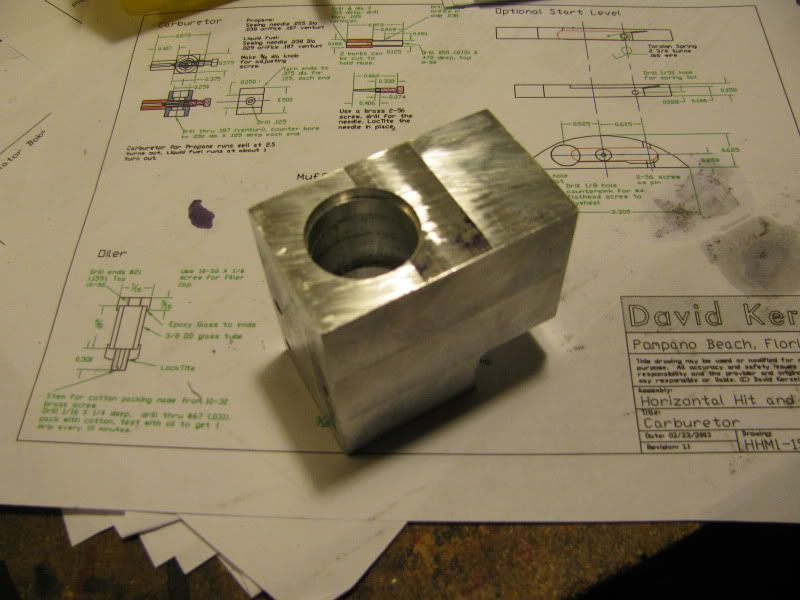