We have a cylinder. It is pretty, it fits where it's supposed to, and after honing the bore with a 3 stone brake hone it measures about 1.001" bore. That's all for today folks. I will get some mounting holes drilled in the cylinder tomorrow.---Brian
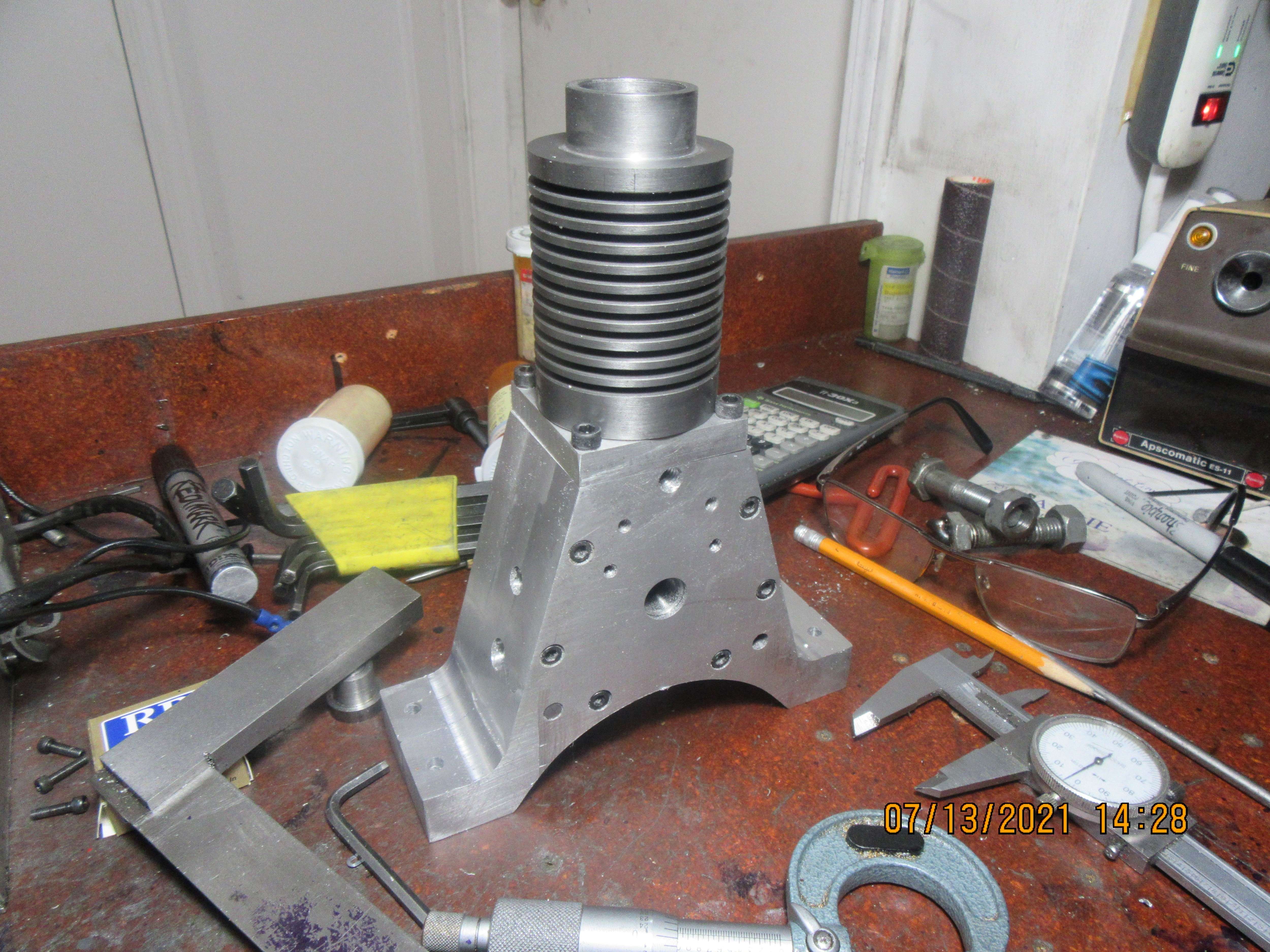
Today seen the beginning of a new engine.---The design phase, at least. After recently seeing an Upshur T head coming together on HMEM and a post by Vederstein about building a T head engine I thought that would be an interesting engine to design and build. I'm in no rush to start building, but I know how that generally works. I spent most of today bringing the design along to this stage, and will probably finish up the cylinder head tomorrow.
Brian, when you get time I would be interested in knowing what equipment is required to cut gears. Bevel gears obviously must use a different technique and cutter? You seem to make it sound so simple but I am thinking it is only be because you know what you are doing, but it is still a machining mystery to me.Got up nice and early this morning and cut both 50 tooth gears. Everything worked out nice, no extra teeth. Maybe I'll do the 25 teeth gears tomorrow. It has been a lovely day here, had a family birthday party for my daughter and I out in my backyard. There are twelve of us now in the family. I'm the oldest at 75, Davy's the youngest at 1 1/2 years.
![]()