- Joined
- Jan 17, 2009
- Messages
- 887
- Reaction score
- 82
Started to cut metal for this engine: for those of you who didn't pick it up her's my thread on the design
http://madmodder.net/index.php?topic=3990.0
And a pic of the engine the model will be based on.
Using a chunk of brass donated by John:- thanks John
first square it up and bring it to size with a fly cutter.
Then with a 18mm end mill cut a couple of scallops down the sides,
Then set the boring bar up to cut a 12.5 mm rad
Open the scallops out to 12.5 mm rad
And counter bore them out to 15 mm rad
so you've got this
Then turn up a couple of brass spools that fit into the scallops
And you've got your self a twin cylinder.
Well you will have when you've silver soldered them together thats a job for the week end :- if I can sneak away, our son and wife are staying with our new baby granddaughter, so we will have a string of visitors ho-ing and ar-ing, and doesn't she look like youing.

Really looking forward to it
Stew
http://madmodder.net/index.php?topic=3990.0
And a pic of the engine the model will be based on.
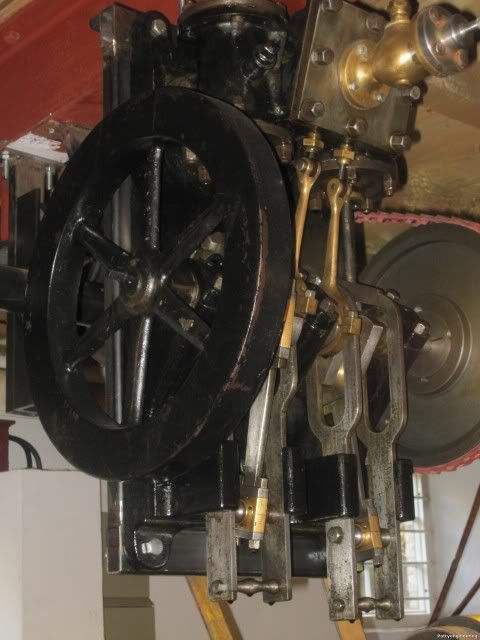
Using a chunk of brass donated by John:- thanks John

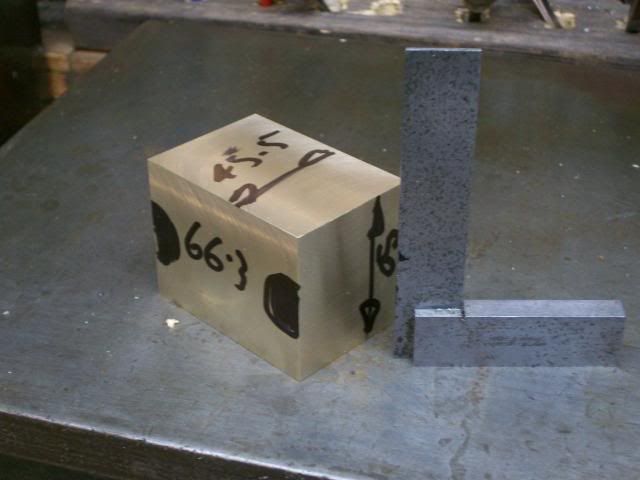
Then with a 18mm end mill cut a couple of scallops down the sides,
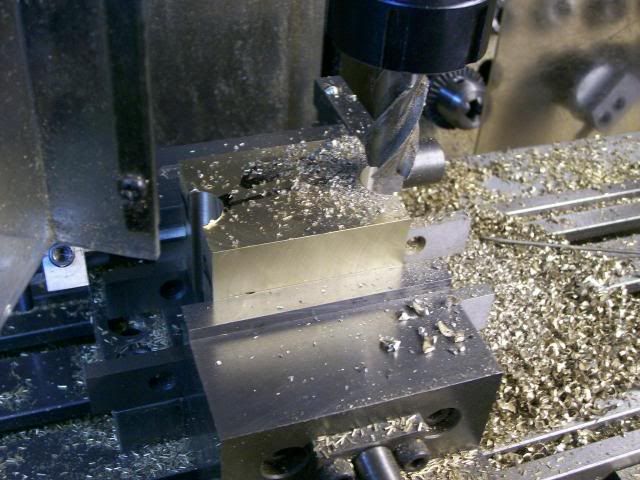
Then set the boring bar up to cut a 12.5 mm rad

Open the scallops out to 12.5 mm rad
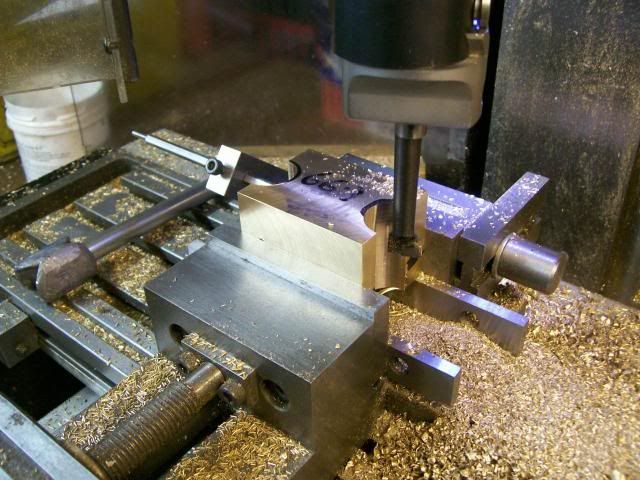
And counter bore them out to 15 mm rad
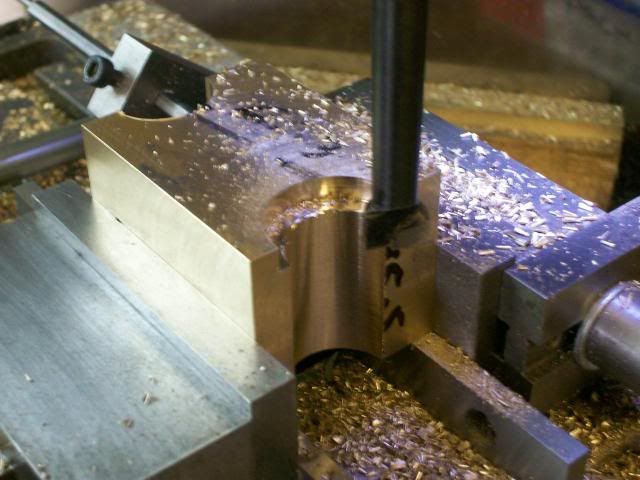
so you've got this
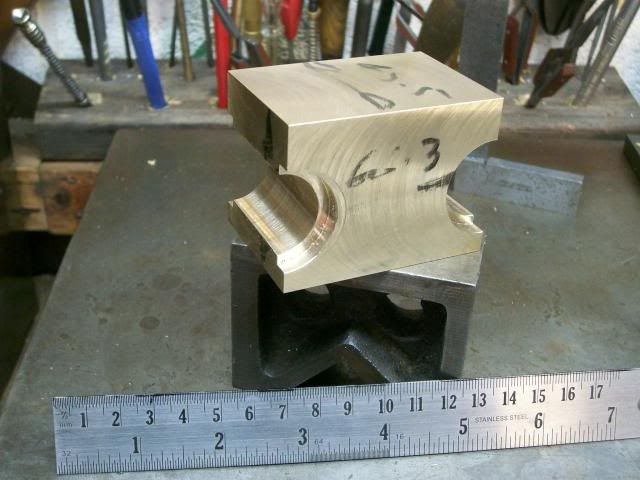
Then turn up a couple of brass spools that fit into the scallops
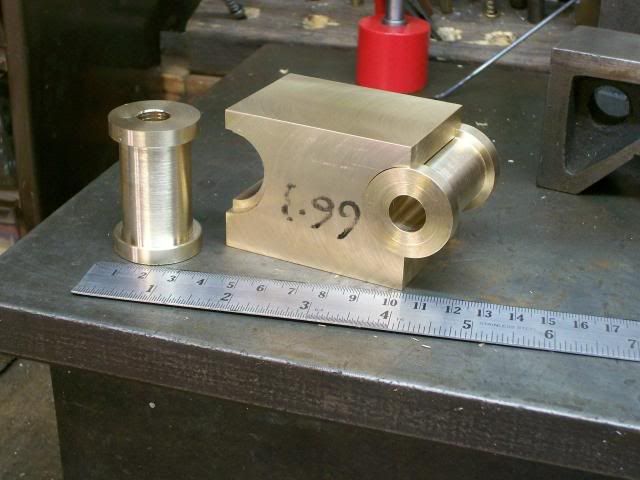
And you've got your self a twin cylinder.
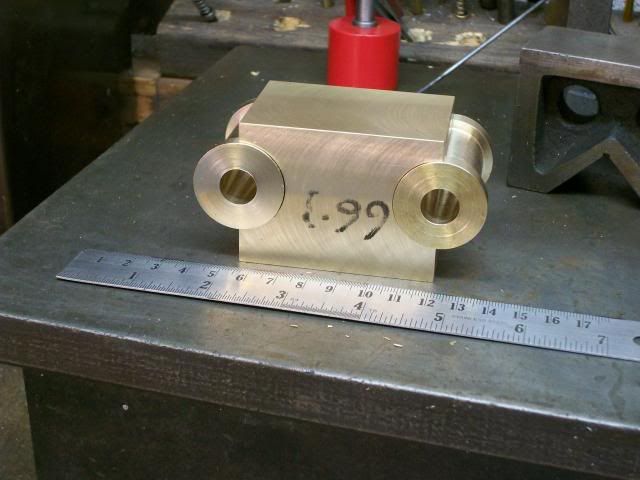
Well you will have when you've silver soldered them together thats a job for the week end :- if I can sneak away, our son and wife are staying with our new baby granddaughter, so we will have a string of visitors ho-ing and ar-ing, and doesn't she look like youing.
Really looking forward to it
Stew