- Joined
- Jan 17, 2009
- Messages
- 887
- Reaction score
- 82
Thanks for fead back shred, no ones shouted at me so I think i'll just goahead and post the drawing when I'm done.
Any way not so cold today so got the pistons finished.
Set up for drilling gudgiun hole. find edges and index to corect position, all three were drilled from the same setting
The inside of the piston requires milling out to give clearance for the con rod little end.
This is the set up, a length of 4mm rod was inserted in gudgion pin hole then squares this up to the vice,
At my first attemp I used a 3mm slot drill but broke it so went up the a 4.5 end mill that worked ok
And her they are done
And on the crank
I've just got three bits to make before I start assy and test, so I've attached the drawing that shows these last three bits
Have fun
Stew
View attachment Sht 4-Model.pdf
Any way not so cold today so got the pistons finished.
Set up for drilling gudgiun hole. find edges and index to corect position, all three were drilled from the same setting
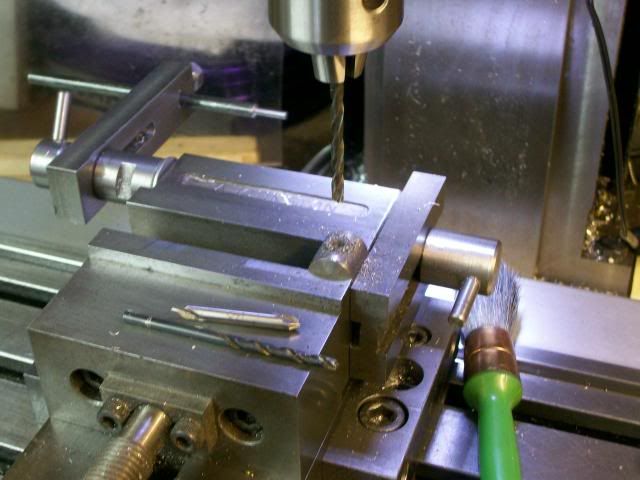
The inside of the piston requires milling out to give clearance for the con rod little end.
This is the set up, a length of 4mm rod was inserted in gudgion pin hole then squares this up to the vice,
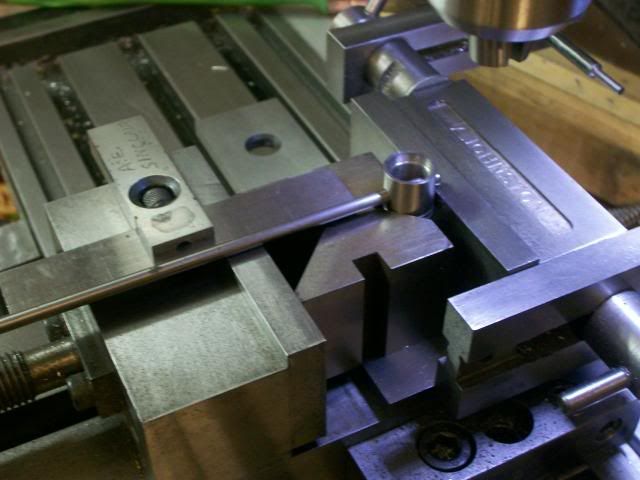
At my first attemp I used a 3mm slot drill but broke it so went up the a 4.5 end mill that worked ok
And her they are done
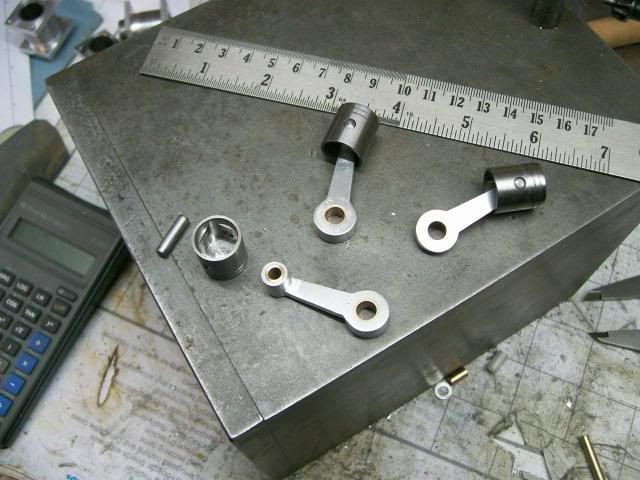
And on the crank
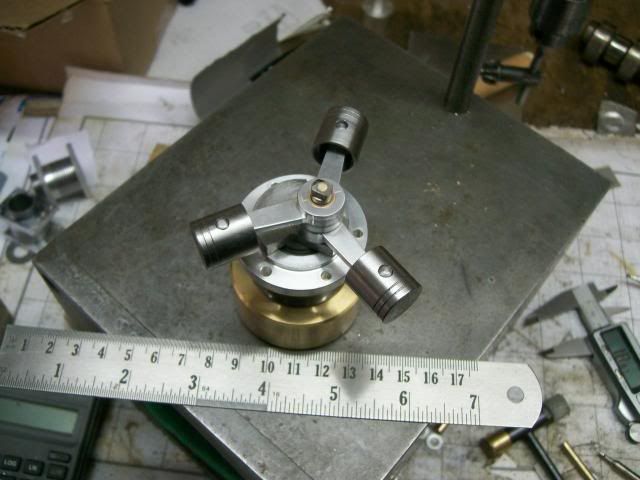
I've just got three bits to make before I start assy and test, so I've attached the drawing that shows these last three bits
Have fun
Stew
View attachment Sht 4-Model.pdf