The Lever
Made one that didnt snap so figured a second try was in order to verify the results.
First up was to shape the piece. Did same as first, similar to Zee's sketch with the addition of a 0.200 by 0.080 neck.
Used a 0.125 drill bit shank ground down at an angle to form a radius between the neck and shoulder. It does chatter but did the job
Used 220 and 400 paper to smooth the piece out, with a quick brush against a buffing wheel to remove any chatter, scratches. Piece ready for heat.
Held the long end with a pair of vise grips (they have a hole ground into the jaws to grip better with less force. Heated the piece with a regular propane torch. Sorta a dull red color that turns silvery, at this point with piece still in flame used some flat nosed needle nose to grap the lever end and with even pressure bent the piece just a bit. Slow and even bending, as soon as the needle nose touch the piece the heat gets drawn away, youi can see the color change so keep the piece in the flame and work slow
First bend just a few degrees To take the photos I had to dunk the piece in water after each bend and restart the heat process. As the end product was sucessuful I be sticking with this approach
Second Bend Few more degrees
Third Bend Few more
Final Bend Looking good Top piece is one I did a few days ago, bottom one is the result of this adventure.
As close a shot as my camera will allow, but the bend is clean and contained within the neck portion
It can be done, just allow the material to bend on its own good time while applying the encouragement. To much force or try to bend it too fast and, well, as ZEE puts it, much colorful words will be heard
Robert
Made one that didnt snap so figured a second try was in order to verify the results.
First up was to shape the piece. Did same as first, similar to Zee's sketch with the addition of a 0.200 by 0.080 neck.
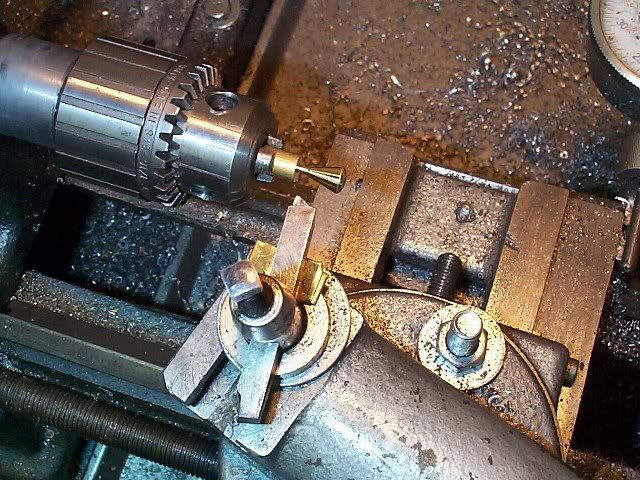
Used a 0.125 drill bit shank ground down at an angle to form a radius between the neck and shoulder. It does chatter but did the job
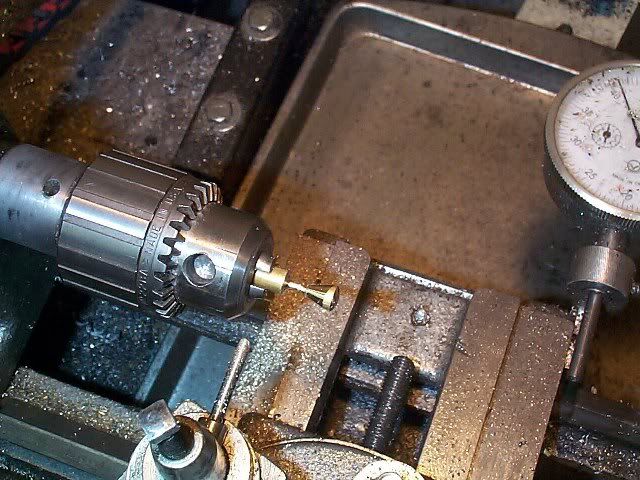
Used 220 and 400 paper to smooth the piece out, with a quick brush against a buffing wheel to remove any chatter, scratches. Piece ready for heat.
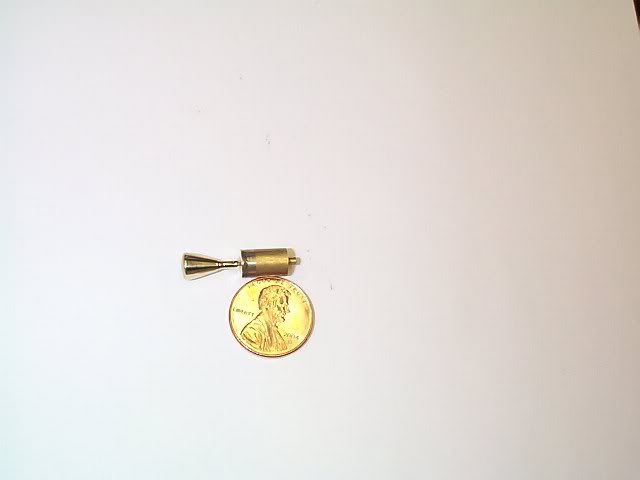
Held the long end with a pair of vise grips (they have a hole ground into the jaws to grip better with less force. Heated the piece with a regular propane torch. Sorta a dull red color that turns silvery, at this point with piece still in flame used some flat nosed needle nose to grap the lever end and with even pressure bent the piece just a bit. Slow and even bending, as soon as the needle nose touch the piece the heat gets drawn away, youi can see the color change so keep the piece in the flame and work slow
First bend just a few degrees To take the photos I had to dunk the piece in water after each bend and restart the heat process. As the end product was sucessuful I be sticking with this approach
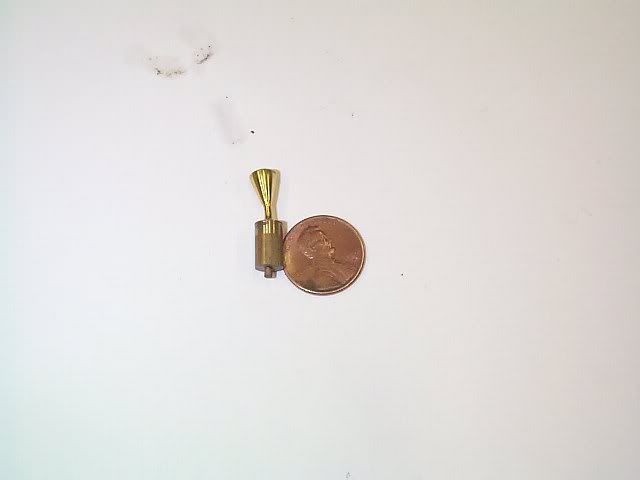
Second Bend Few more degrees
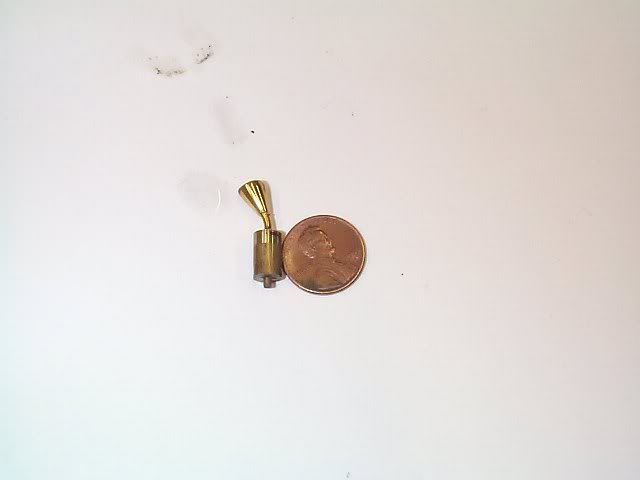
Third Bend Few more
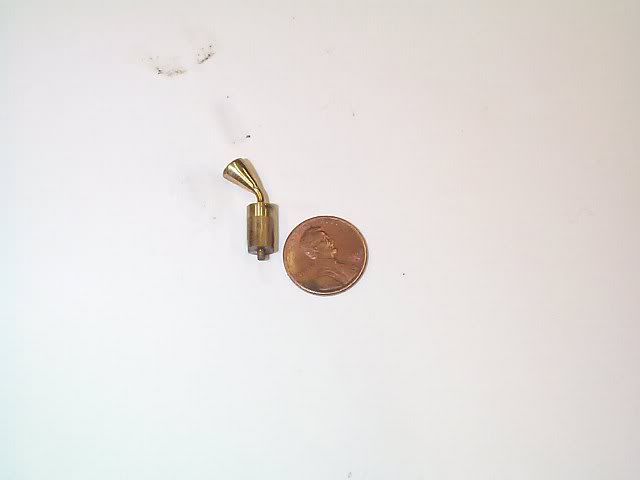
Final Bend Looking good Top piece is one I did a few days ago, bottom one is the result of this adventure.
As close a shot as my camera will allow, but the bend is clean and contained within the neck portion
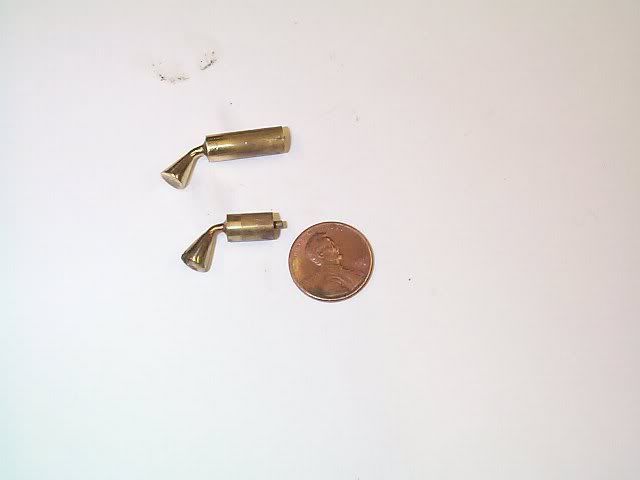
It can be done, just allow the material to bend on its own good time while applying the encouragement. To much force or try to bend it too fast and, well, as ZEE puts it, much colorful words will be heard
Robert