zeeprogrammer
Well-Known Member
- Joined
- Mar 14, 2009
- Messages
- 3,362
- Reaction score
- 13
Here's a pic with vise stop behind...can't install it...
Here's a pic with vise stop in front...
Here's a pic using a 1-2-3 block in back up against the collet...
I don't know if this is what you all meant...
[EDIT: I don't think that last shot with the clamps is right. Now it's not just the collet block that has to be square...but the draw bar thingie too. Needs to be in front. Okay. Enough of this...gotta mill. Back to Spindex ;D]
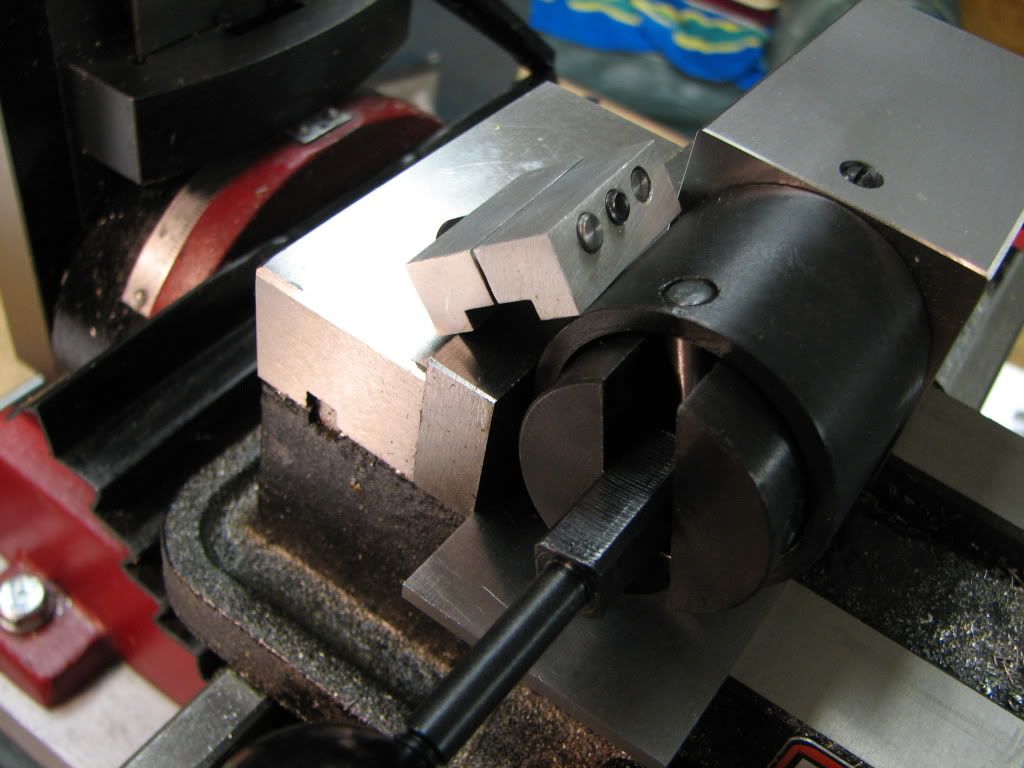
Here's a pic with vise stop in front...

Here's a pic using a 1-2-3 block in back up against the collet...
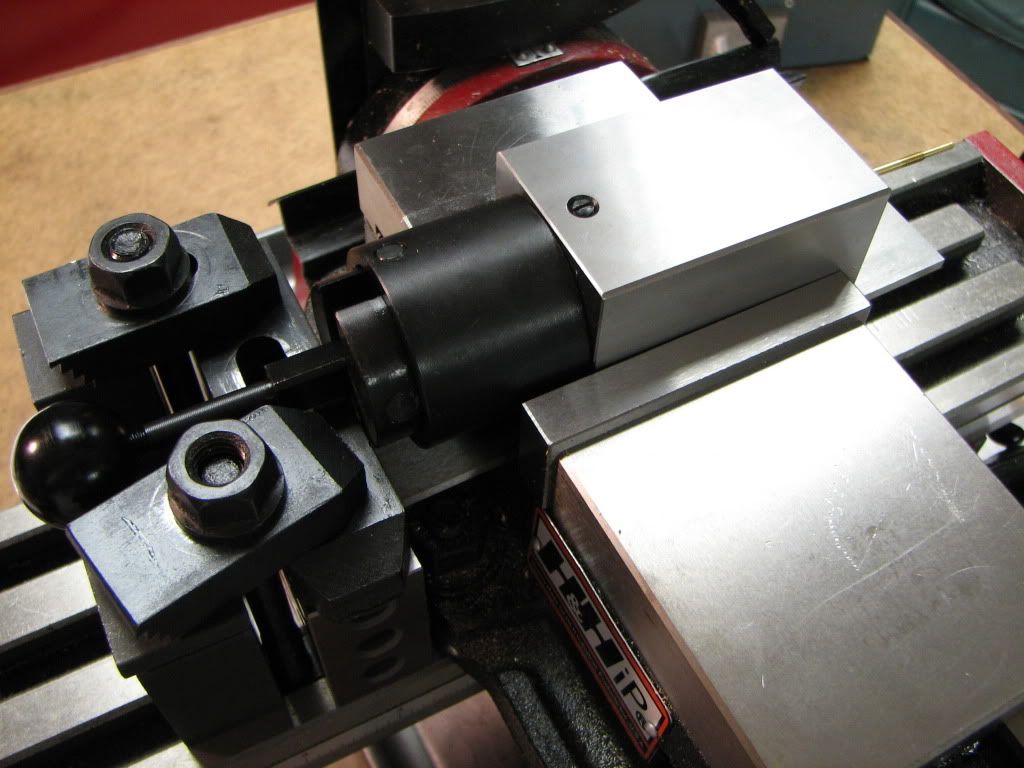
I don't know if this is what you all meant...
[EDIT: I don't think that last shot with the clamps is right. Now it's not just the collet block that has to be square...but the draw bar thingie too. Needs to be in front. Okay. Enough of this...gotta mill. Back to Spindex ;D]