zeeprogrammer said:I've started with the eccentric rod. But I took some longer stock, drilled one end, and mounted it in the lathe with a live center.
Centers = Good
Hi Zee;
I would do this similar to how MB describes, using flat stock. You can do almost the entire piece in one setup in the lathe this way. All you need to do to finish it is drill the holes in the ends and cut off the excess left over on the ends where the holes were for your centers.
If you only have round stock, you can turn it into flat stock on the milling machine, (best this way), or you can cut the profile of the piece from the round stock on the lathe and then mill the flat sides. If you do it this way, you can chuck one end, but still need the center in the tail stock end.
Start by turning a ball on each end, the basic size of the small and large end of the crankshaft. You don't need a ball turner. With the tail stock center in the end that will be the small end, start by making a couple of 45 deg tapers, one on each side of what will become the ball. Then file the corners off of the 45 deg tapers to form the ball. If you draw the piece out, you will find that you can make a whole bunch of tapers instead of just the two 45's, and get closer to the ball shape. Brass is very easy to file in the lathe, though, and even with only two tapers, it won't take long.
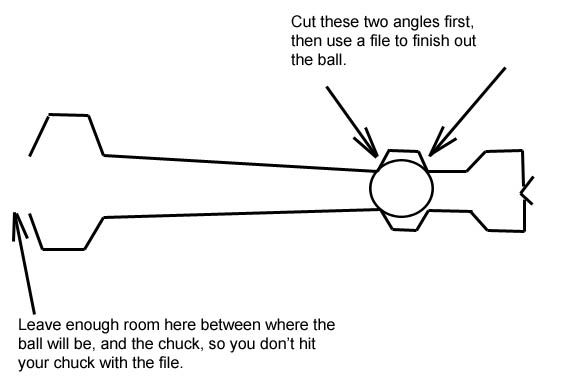
For the taper between the ends, you would be okay to turn it taking light cuts. I doubt your compound slide will do that in one cut, or that it will even fit with the tail stock there at the end of the piece, but if it does, great. Otherwise, take light cuts and make two diameters on the shaft part of the crankshaft, and file it in the lathe with a fairly fine cut file. Just don't push hard, and you won't bend the piece.
The thing about starting with round stock, for this piece, is that you still have to make it flat in the milling machine after you have the shaft part done, so really, you might as well go ahead and make a piece of flat stock from your round to begin with.
For a tool, try HSS ground something like this, and used at this approximate angle in your tool post. Leave the tool flat on top for brass cutting. Put a very small radius or facet on the very end to get a nice cut.
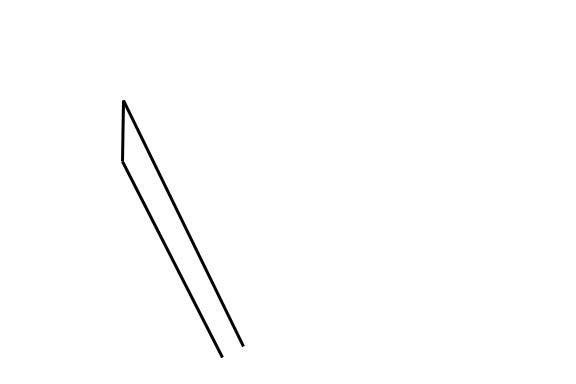
Hope this stuff makes sense. Sorry the "drawings" look like a six year old did them. I'm not much good without paper and pencil.
Dean