zeeprogrammer
Well-Known Member
- Joined
- Mar 14, 2009
- Messages
- 3,362
- Reaction score
- 13
Well, I think the people that suggested I cut my reamers down have misled me.
If I shorten this one anymore...there won't be any reamer left!!!
What are you people thinking?!
I think it's the other end that...oh...is that what you meant? Darn.
(Is a fake picture. Just couldn't resist. Actually meant to have a real one but when I went to do it...I realized that I don't have the required reamer! Nothing to cut! For the other hole, I think the reamer is short enough already. If not...I'll cut it when I need it...not when I'm not sure.)
If I shorten this one anymore...there won't be any reamer left!!!
What are you people thinking?!
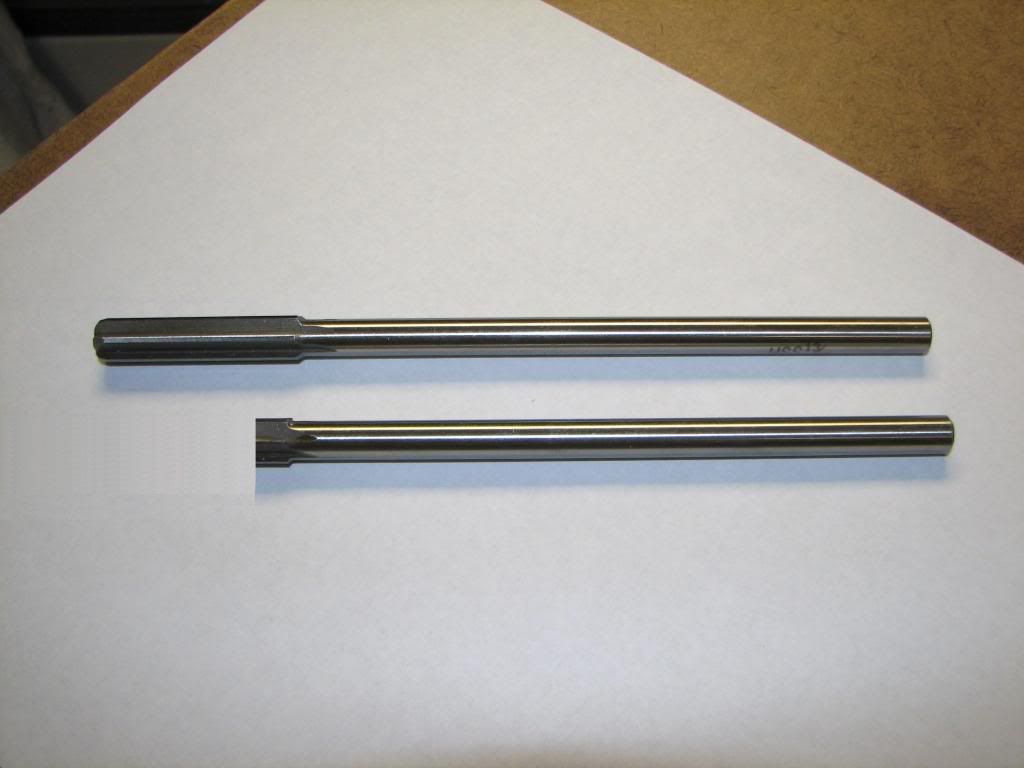
I think it's the other end that...oh...is that what you meant? Darn.
(Is a fake picture. Just couldn't resist. Actually meant to have a real one but when I went to do it...I realized that I don't have the required reamer! Nothing to cut! For the other hole, I think the reamer is short enough already. If not...I'll cut it when I need it...not when I'm not sure.)