zeeprogrammer
Well-Known Member
- Joined
- Mar 14, 2009
- Messages
- 3,362
- Reaction score
- 13
Didn't get anything done today...still hurting a little from yesterday. But my 'real' excuse is that wife came home from her trip. Right.
Thought about the tramming question from -B-...Not sure it's about tramming. The part itself (the edges) seem to be perfectly square...it's just the slot that's off. If the mill was out of tram I think the part would also have been out. Maybe the saw and/or arbor? Don't think so. I think the part rotated in the spindex. That's my first 'professional' opinion.
Should know more this weekend or when I have time to relax and be careful. At least be careful. At least have a go. Wife is leaving again this weekend.
I'll also blame 'nameless', whose initials are VM, for not having enough machining time tonight.
What? Hey! A mystery part showed up...
Doesn't look like the fellow has a very good countersink. It's probably 25 years old and dull as me.
Thought about the tramming question from -B-...Not sure it's about tramming. The part itself (the edges) seem to be perfectly square...it's just the slot that's off. If the mill was out of tram I think the part would also have been out. Maybe the saw and/or arbor? Don't think so. I think the part rotated in the spindex. That's my first 'professional' opinion.
Should know more this weekend or when I have time to relax and be careful. At least be careful. At least have a go. Wife is leaving again this weekend.
I'll also blame 'nameless', whose initials are VM, for not having enough machining time tonight.
What? Hey! A mystery part showed up...
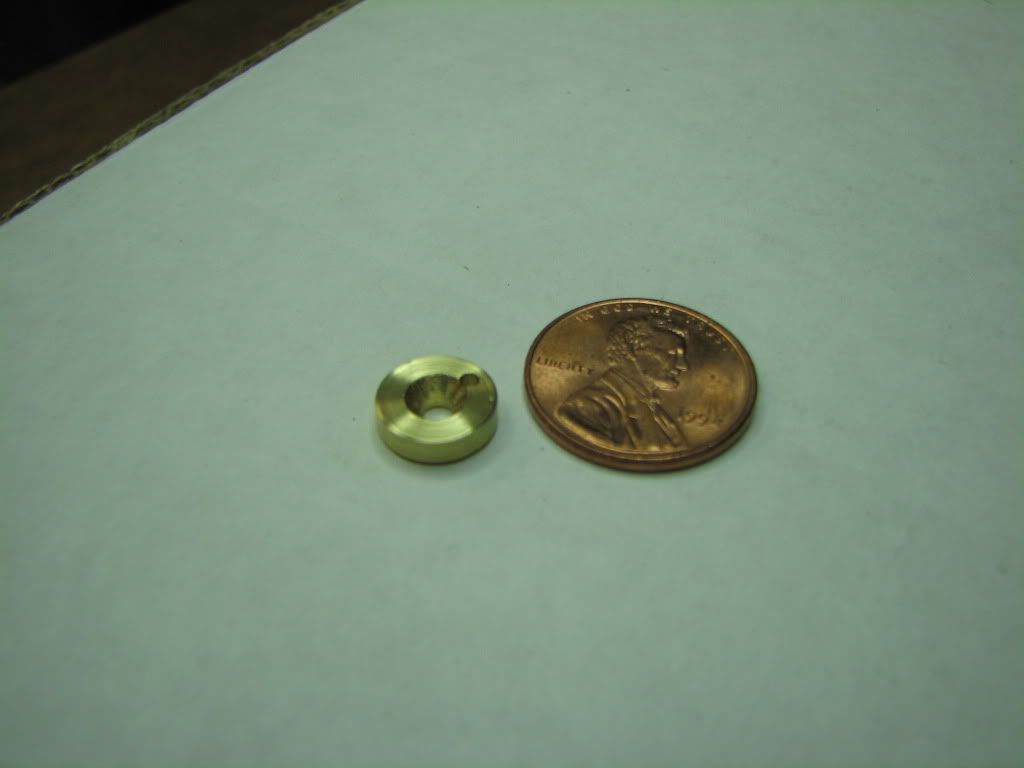
Doesn't look like the fellow has a very good countersink. It's probably 25 years old and dull as me.