Heres a pic of the head mounted to the fixture upside down so the holes for the valve cages can be seen. I used a small woodruff key cutter to extend the slot for the coolant to surround the exhaust valve cage. Heres where I made my first big OOPS. When withdrawing the keycutter from the hole on the last part I drug it across the surface of the hole leaving a large void where coolant will leak. I have a replacement started and will finish soon.
Heres a pic of the heads attached to the cylinders. I am going to open up the coolant lines some before I go any further. I was originally going to use 3/16 fittings but I think they will be too restrictive so I will open everything up to 1/4".
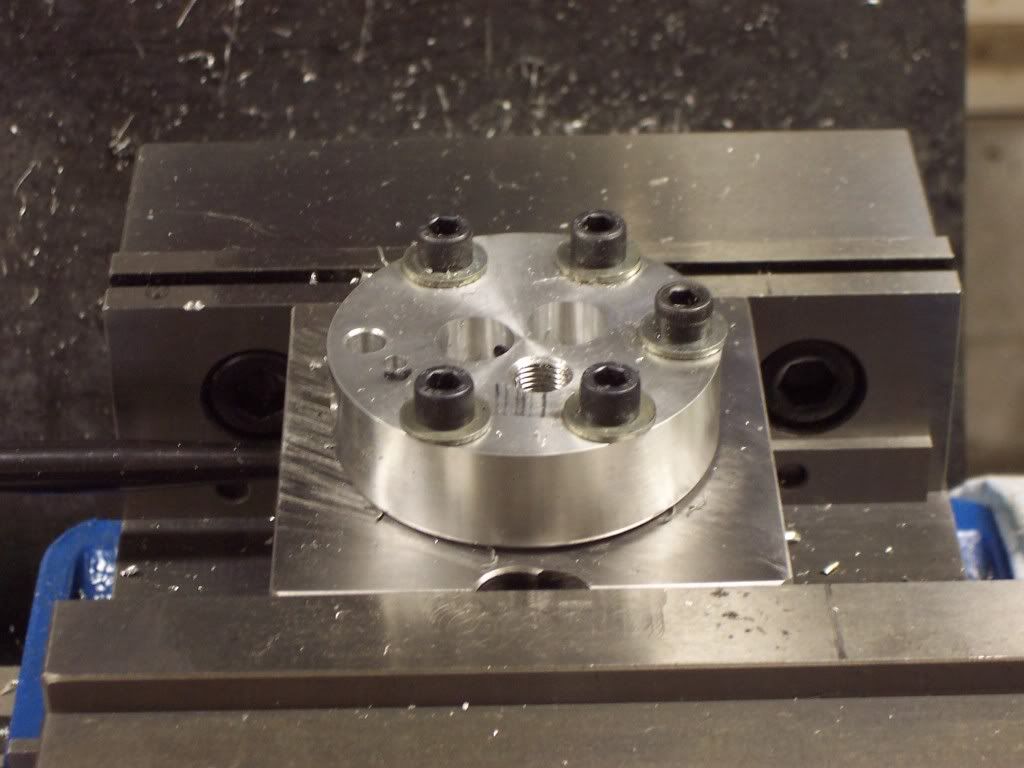
Heres a pic of the heads attached to the cylinders. I am going to open up the coolant lines some before I go any further. I was originally going to use 3/16 fittings but I think they will be too restrictive so I will open everything up to 1/4".
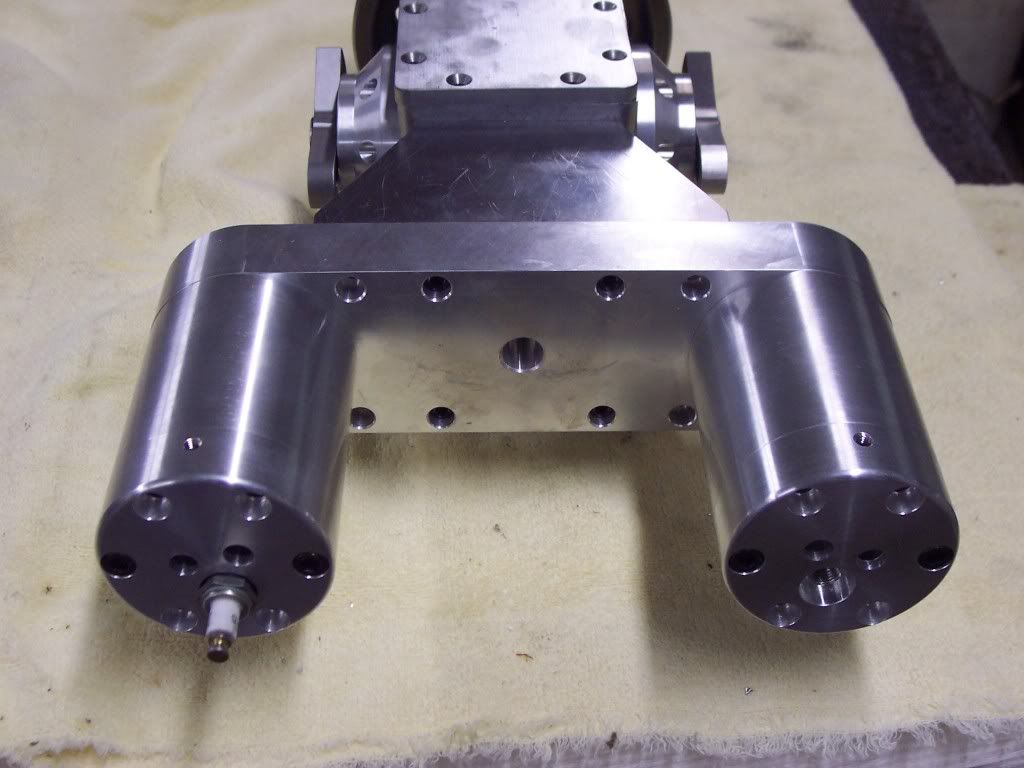