I had the devil of a time with this rocker arm tower. Had no problem making the large piece which bolts to the cylinder head. I reamed the top hole with a 3/16" reamer, and then decided that rather than silver solder the rocker pin into it, I would machine it to have a press fit. I started out with a piece of 1/4" cold rolled and machined it to be about 0.010" oversize. then I decided to take the remaining bit off with file and emery paper, aiming for 0.189" diameter for a press fit. I sanded, and I sanded and I filed and I filed, checking every 20 seconds with a micrometer so that I didn't turn it undersize. I eventually got it down to 0.189" and started to press it into place, heating the larger part with my oxy acetylene torch to expand it a little---and it went crooked!!! Then I had to take it apart, straighten it out (burned the Hell out of my finger doing so). Then I was successful in getting it pressed into place, but I'm sure glad I wasn't paying myself machinists wages, because it took about four times longer than it should of. The good news is that while I was rooting around in my box of goodies looking for a 1/4"-32 sparkplug, I found a couple of 1/8" ball bearings that I didn't know I had. They will be perfect for my cooling fan shaft.
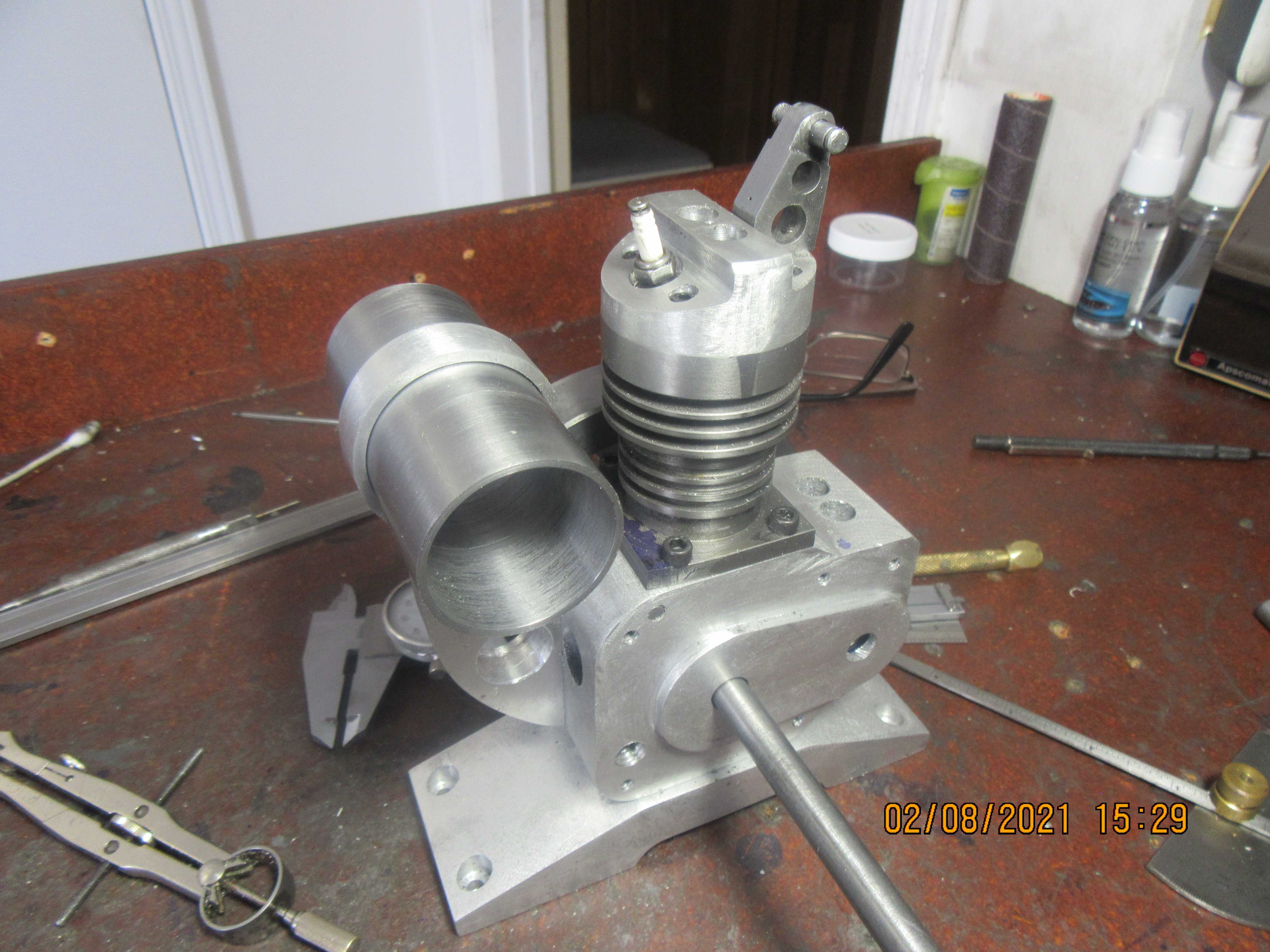
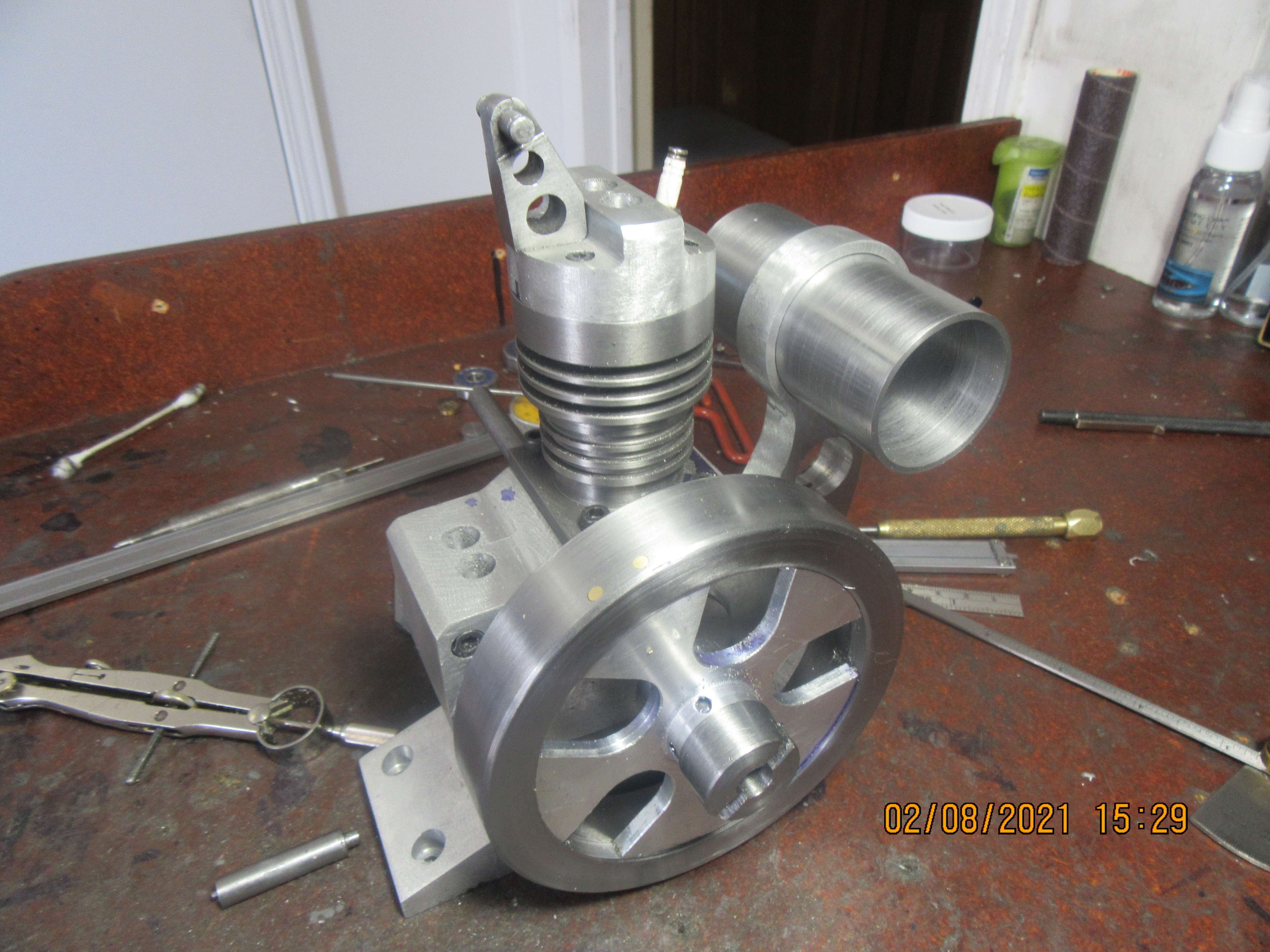