- Joined
- Jan 3, 2008
- Messages
- 2,085
- Reaction score
- 17
I am adding this as a separate thread so as not to extend the friendly debate in the "two-cylinder mill engine" thread on engines doing productive work. Actually one of mine...a Tiny Power i built maybe 12-13 years ago does in fact get its annual exercise from just after Thanksgiving until Christmas break...60-70 rpm's all day long turning a little dorm sized Christmas tree resting on a cabinet type turntable. The belt and pulley arrangement isn't fancy but it gets the job done. It sits atop a riser on my desk and faces out into the hallway where all the engineering technology labs are located. The fun for me is not just looking up to see the engine running smoothly and almost silently, or seeing the tree turning, but rather seeing the reactions of the students as they walk by or stop and come in. Amazing how many actually ask what it is or what makes it work!!
Anyway enjoy, along with an early wish for a Happy Holiday Season!
Bill
Anyway enjoy, along with an early wish for a Happy Holiday Season!
Bill
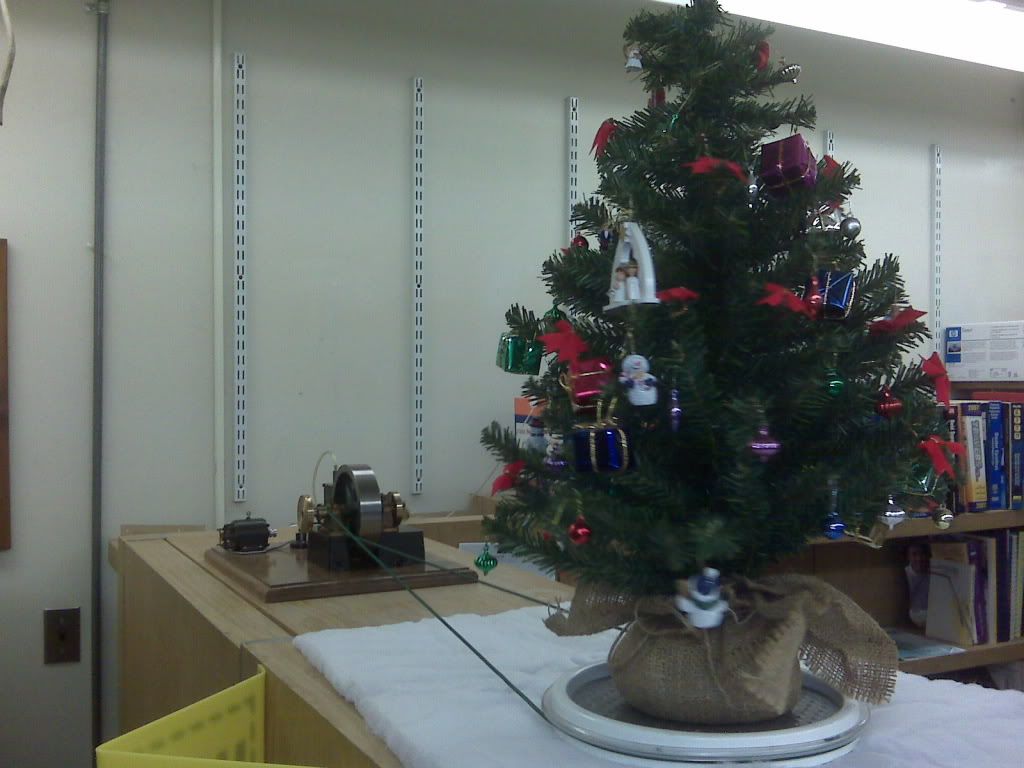