Tony Bird
Senior Member
Hi,
Some Thoughts on the Design & Construction of a Small Water Gauge suitable for Model Steam Boilers.
I have made many small steam boilers and usually make the fittings for them as well. Boiler fittings usually look better if they are small, there is a limit to how small of course, they have to work. Designing and making boiler water gauges over the years I have decided on several factors that effect how well they work.
Use the largest diameter glass tube you can, I have found that a tube 4mm OD with an ID of 2.5mm is about as small as you can hope to work. Also the minimum size of the water/steam holes in the fittings should be the same size or larger than the ID of the glass tube. Another factor to be considered is the ease of cleaning the gauge glass. The glass itself can usually be cleaned by removing the nut on the top fitting and pushing a pipe cleaner (tobacco type pipe) down into the tube. It is also a good idea to be able to clean out any mineral deposits that accumulate in the bottom fitting without having to remove it from the boiler. Good boiler hygiene can reduce this mineral deposit problem even if like me you live in a soft water area and mostly use rainwater in your boilers. If the boiler is used frequently like the one I use for testing models it is a good idea to completely fill the boiler with a mild acid such as citric or white vinegar about once a year. Leave the acid in the boiler for a few hours say over night then after emptying the acid flush well with clean water. Doing this will remove a lot of the deposits that might be in the boiler. If the boiler isnt used much it is a good idea to drain the water from it after use.
With small boilers it is often difficult to make the water gauge short enough so there is enough visible length left on the glass tube to see a reasonable length of water usage.
The design following tries to keep the height of the fittings as small as practical and its design is based on previously made gauges. First a couple of photographs of some gauges already made. They are basically of the same type.
One made using round stock for the bodies
.
One made from round stock fitted with a blow down valve. Note the glass tubes which are half white with various lines running down them are often slightly over size and out of round. They are also a little more difficult to cut.
One made from hexagonal stock.
The one that the one to be described is based on this one which is made from 7mm square stock which had to be machined specially. Note the screws which allow the holes in the brass bodies to be cleaned
Machining 7mm square stock on a shellac chuck.
The one to be described uses a slightly larger 8mm (5/16) square stock, which is a standard size rod. The extra thickness will allow easier fitting of blow down valves either directly to the fitting or by pipe to a valve, also the overall dimension of the top and bottom fitting will be the same rather than different. Two prototypes will be built from square stock and another two using 8mm (5/16) hexagonal stock to see how they compare.
Drawing of the proposed water gauge which will probably be modified as the parts are made.
Materials to be used brass stock; 8mm (5/16) square for the gauges main body, 8mm (5/16) hexagonal for nuts and prototype main body. 6.35mm (1/4) hexagonal for attaching the gauge to the boiler,
In the next couple of days I will post some photographs taken while machining the parts of the gauges.
Regards Tony.
Some Thoughts on the Design & Construction of a Small Water Gauge suitable for Model Steam Boilers.
I have made many small steam boilers and usually make the fittings for them as well. Boiler fittings usually look better if they are small, there is a limit to how small of course, they have to work. Designing and making boiler water gauges over the years I have decided on several factors that effect how well they work.
Use the largest diameter glass tube you can, I have found that a tube 4mm OD with an ID of 2.5mm is about as small as you can hope to work. Also the minimum size of the water/steam holes in the fittings should be the same size or larger than the ID of the glass tube. Another factor to be considered is the ease of cleaning the gauge glass. The glass itself can usually be cleaned by removing the nut on the top fitting and pushing a pipe cleaner (tobacco type pipe) down into the tube. It is also a good idea to be able to clean out any mineral deposits that accumulate in the bottom fitting without having to remove it from the boiler. Good boiler hygiene can reduce this mineral deposit problem even if like me you live in a soft water area and mostly use rainwater in your boilers. If the boiler is used frequently like the one I use for testing models it is a good idea to completely fill the boiler with a mild acid such as citric or white vinegar about once a year. Leave the acid in the boiler for a few hours say over night then after emptying the acid flush well with clean water. Doing this will remove a lot of the deposits that might be in the boiler. If the boiler isnt used much it is a good idea to drain the water from it after use.
With small boilers it is often difficult to make the water gauge short enough so there is enough visible length left on the glass tube to see a reasonable length of water usage.
The design following tries to keep the height of the fittings as small as practical and its design is based on previously made gauges. First a couple of photographs of some gauges already made. They are basically of the same type.
One made using round stock for the bodies
.
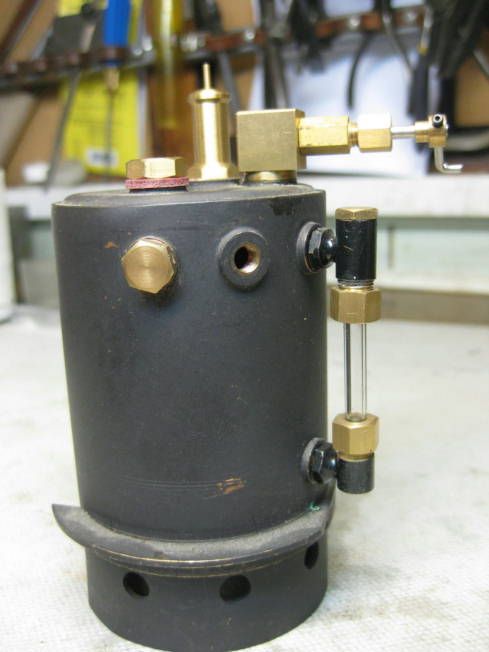
One made from round stock fitted with a blow down valve. Note the glass tubes which are half white with various lines running down them are often slightly over size and out of round. They are also a little more difficult to cut.
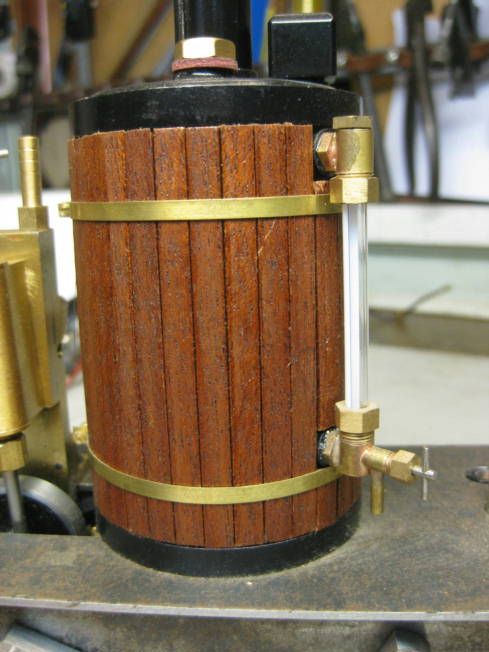
One made from hexagonal stock.
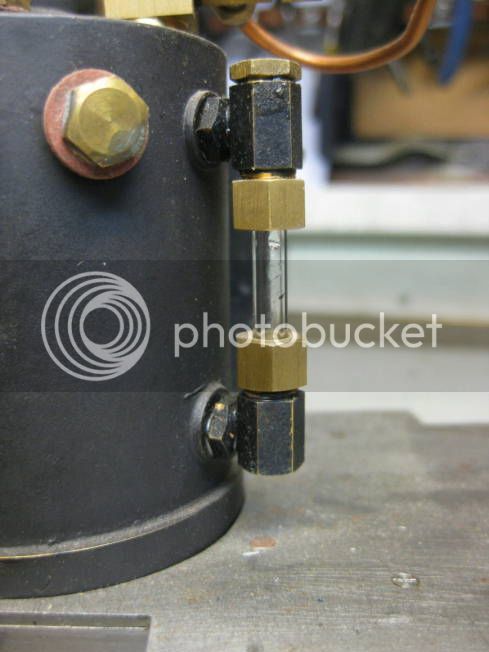
The one that the one to be described is based on this one which is made from 7mm square stock which had to be machined specially. Note the screws which allow the holes in the brass bodies to be cleaned
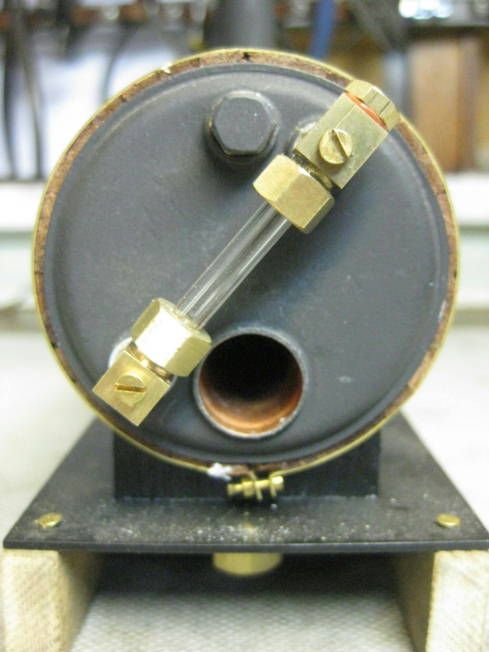
Machining 7mm square stock on a shellac chuck.
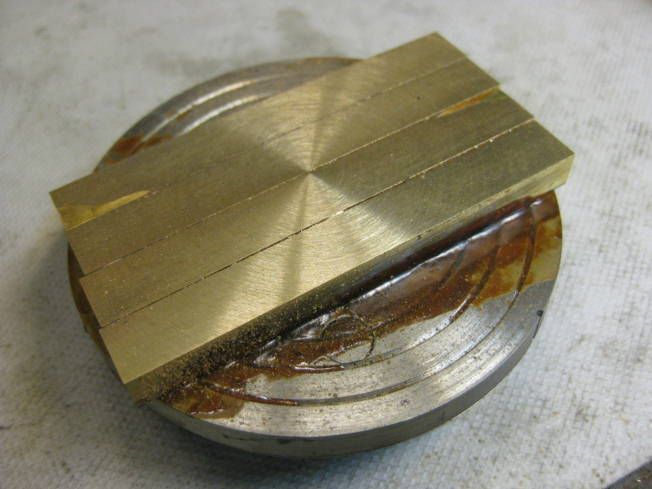
The one to be described uses a slightly larger 8mm (5/16) square stock, which is a standard size rod. The extra thickness will allow easier fitting of blow down valves either directly to the fitting or by pipe to a valve, also the overall dimension of the top and bottom fitting will be the same rather than different. Two prototypes will be built from square stock and another two using 8mm (5/16) hexagonal stock to see how they compare.
Drawing of the proposed water gauge which will probably be modified as the parts are made.
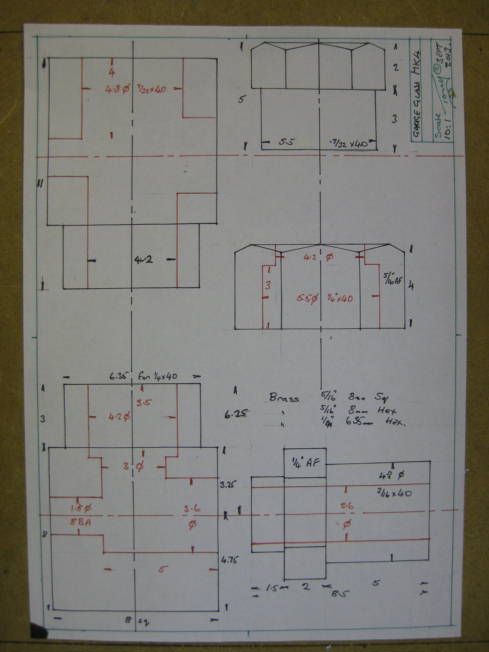
Materials to be used brass stock; 8mm (5/16) square for the gauges main body, 8mm (5/16) hexagonal for nuts and prototype main body. 6.35mm (1/4) hexagonal for attaching the gauge to the boiler,
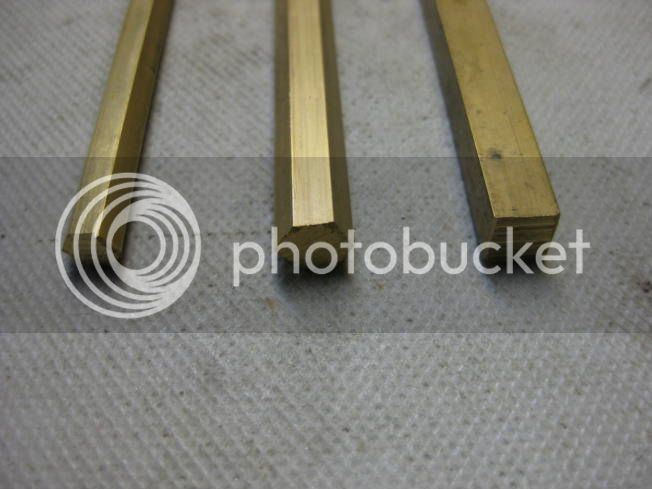
In the next couple of days I will post some photographs taken while machining the parts of the gauges.
Regards Tony.