The pistons finished up nicely. One of the issues I always have when making pistons, is how to put the wrist pin hole in and be perfectly sure it is at 90 degrees to the counterbored slot for the con-rod, and at perfect right angles to the central axis of the piston. I was given this tip some time ago, but never got to try it until yesterday.--The secret---set up in the rotary table chuck, on the mill bed, as shown here. Align the chuck jaws as shown, and put a "sacrificial" spacer between the side of the piston and the right hand jaw. My rotary table is "keyed" to the tee- slots in the top of my milling machine bed, so I am sure of it's position when it is bolted to the Tee slots. Make the slot which the con-rod fits into runs between you and the mill column (the Z axis).--Remember now, you have the rotary table locked in position---we are not going to rotate the attached chuck. Once the slot is finished to size, undo the bolts which hold the rotary table to the tee slots and turn the rotary table with chuck attached (still gripping the piston) 90 degrees to the right so the centerline of the piston is parallel to the milling machine bed. Use a square to make sure the rotary table is setting 90 degrees to the milling machine bed and bolt it down to the tee slots again. Use your center finding device (whatever it may be) to find the centerline of the piston, zero your tool on the exposed end of the piston skirt, and move the table in the right to left (X-travel) to position the chuck directly above the position you want the wrist pin hole to be. Now you have the chuck jaws positioned so that you can run the drill down between them from the top with no interference, and you can drill (and ream) right on through the far side of the piston into the sacrificial aluminum spacer. This ensures that the wrist pin hole will be "square and true" to all the other surfaces. If you are following this thread, please say Hi and let me know you are interested. I am about to embark on a pair of connecting rods.---Brian
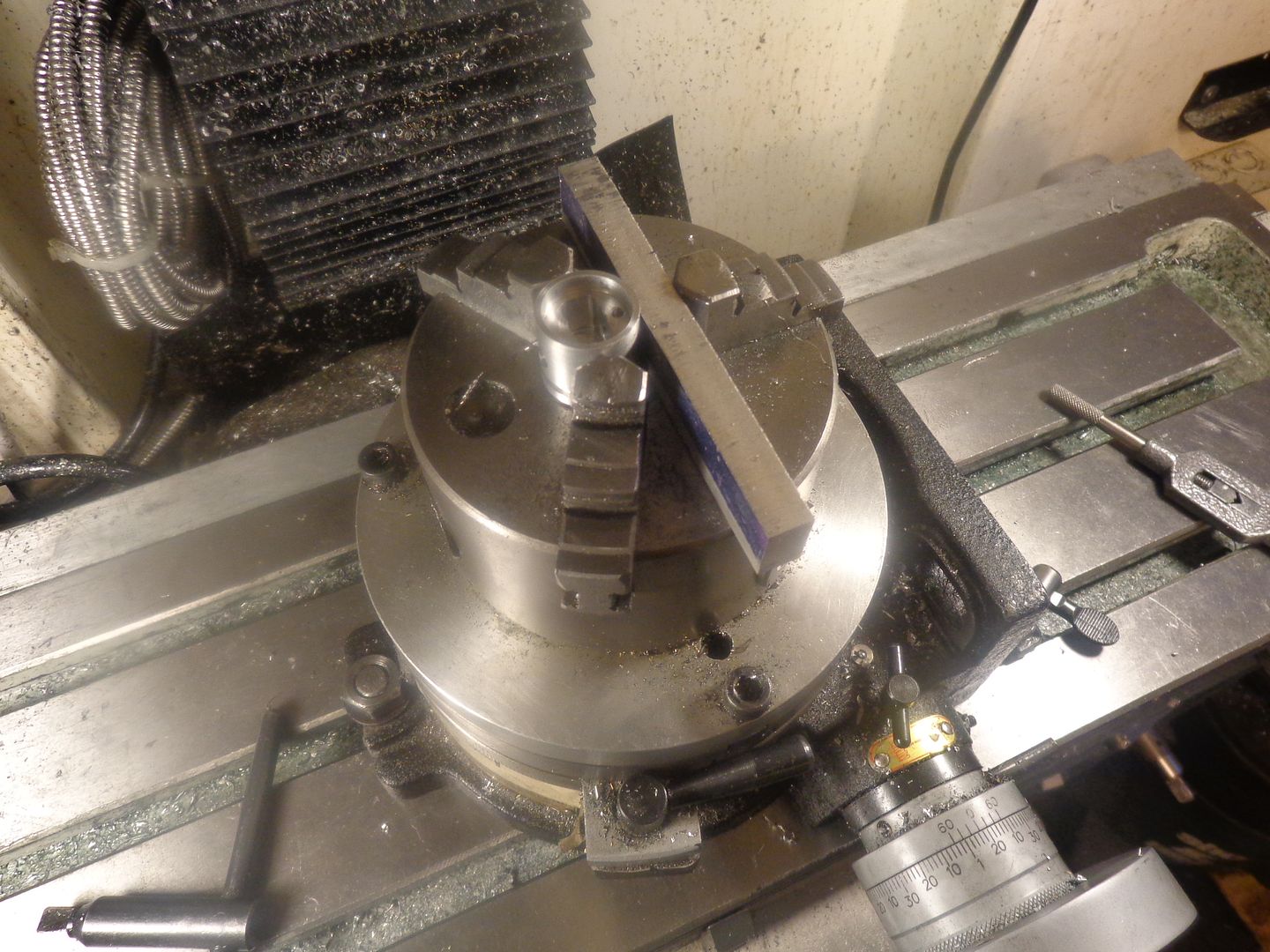