- Joined
- Feb 17, 2008
- Messages
- 2,330
- Reaction score
- 445
The cylinders were turned up same as the Mk1 and the porting cut into them. Then they were rough lapped to about 0.0005 under size. By careful planning I was going to cook a brisket in a slow oven for about 5 to 6 hours today to ward off starvation for a few days. So the oven was set to 550 deg F and I went about cleaning all traces of oil off the cylinders. Oven was up to temperature so the cylinders went in the oven for 20 minutes to produce a blue/black oxide coating. In the intervening time I prepared the brisket for the oven. Remove the cylinders and replace with brisket and turn down the oven temperature.
I turned up a dummy piston to an easy slip fit in the cylinders and made up the wrist pins. I knew that the connecting rod was going to hit the bottom of the cylinder skirt. There are three options. One is to countersink the bottom of the skirt with a 60 degree included angle countersink for about 0.050 inches. Second would be to just reduce the length of the cylinder by 0.050 inches. Both of these options leave the bottom of the piston skirt unsupported as it passes bottom dead center. This would not be a problem as there are only very small side loads near BDC, but it just never seemed very neat to leave it that way. The third option, which is what is on the drawing, is to relieve the bottom of the cylinder with a burr with a notch about 0.150 wide by 0.050 deep at about 30 degrees. That is what I did. Carbide burr in the rotary hand tool and 10 minutes later they were finished. The reason for the dummy piston was so I could check that the rods were not touching. Just hold the cylinder in place on the crankcase and turn the engine over. When the rod quits touching, take off an extra 0.005 or so for safety and it's done.
One other thing that could be done is to round the edges of the rectangular cross section of the rod. This almost gives enough clearance. I did not do this.
All that remains on the cylinders is the final lapping and polishing.
Gail in NM
I turned up a dummy piston to an easy slip fit in the cylinders and made up the wrist pins. I knew that the connecting rod was going to hit the bottom of the cylinder skirt. There are three options. One is to countersink the bottom of the skirt with a 60 degree included angle countersink for about 0.050 inches. Second would be to just reduce the length of the cylinder by 0.050 inches. Both of these options leave the bottom of the piston skirt unsupported as it passes bottom dead center. This would not be a problem as there are only very small side loads near BDC, but it just never seemed very neat to leave it that way. The third option, which is what is on the drawing, is to relieve the bottom of the cylinder with a burr with a notch about 0.150 wide by 0.050 deep at about 30 degrees. That is what I did. Carbide burr in the rotary hand tool and 10 minutes later they were finished. The reason for the dummy piston was so I could check that the rods were not touching. Just hold the cylinder in place on the crankcase and turn the engine over. When the rod quits touching, take off an extra 0.005 or so for safety and it's done.
One other thing that could be done is to round the edges of the rectangular cross section of the rod. This almost gives enough clearance. I did not do this.
All that remains on the cylinders is the final lapping and polishing.
Gail in NM
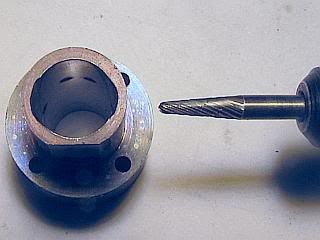
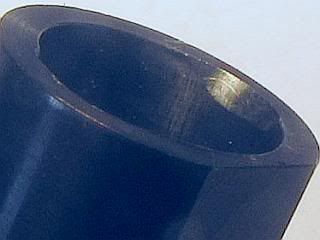

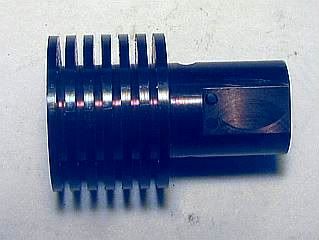