- Joined
- Aug 25, 2007
- Messages
- 3,890
- Reaction score
- 715
I settled on a design for the push rod carrier. Started with a piece of 1/4" thick steel, 3/8" wide and a little over 1" long. Mostly used the milling machine to shape it...
A single screw will go through a horizontal slot in the push rod and attach to the threaded hole at the top of the mount.
Chuck
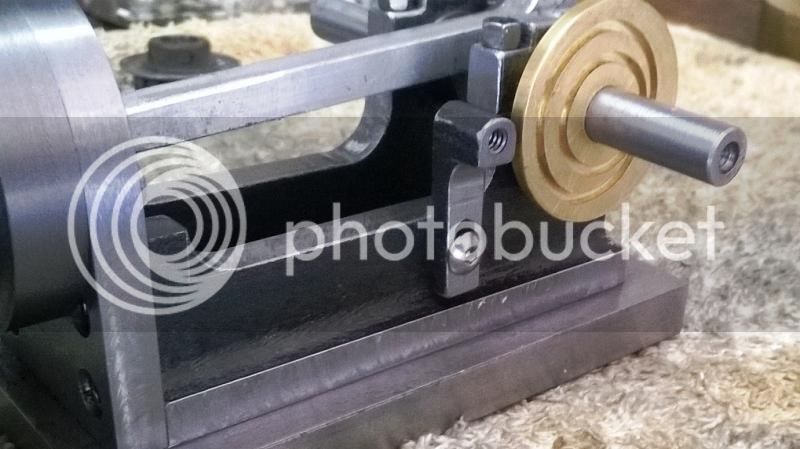
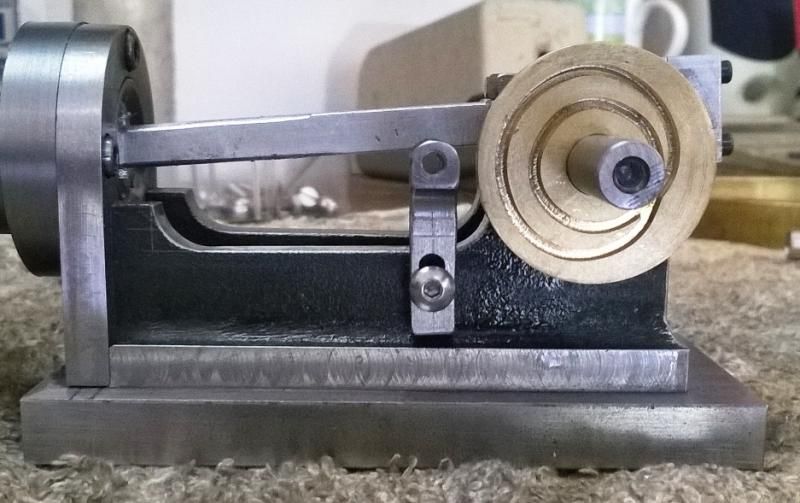
A single screw will go through a horizontal slot in the push rod and attach to the threaded hole at the top of the mount.
Chuck