ChooChooMike
Well-Known Member
- Joined
- Jan 5, 2008
- Messages
- 863
- Reaction score
- 13
Think this is pretty neat to see the before and after shots of my flywheel (1.5" o.d. aluminum). This is for Liney Machines RV-1 engine that I'll be finishing in the next few weeks. All mill/rotary table and lathe work. I'll upload some pix of the machining if there is any interest
Of course all this could have been done CNC in about 2 minutes (not counting the CAD/CAM/setup time), but where is the fun in that ??
This one took about 15-20 hours of my time being very careful to screw it up as little as possible. There's a couple of tiny spots where I dug in a little too far, but that's life ! Great experience to do this manually !
Here's THEIR completed engine picture from their website :
http://lineymachine.googlepages.com/
Hope I can get mine that polished up !! BLING BLING !
Edit : fixed the picture viewing.
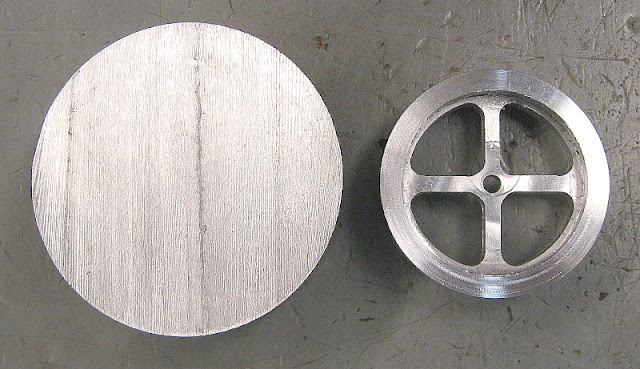
Here's THEIR completed engine picture from their website :
http://lineymachine.googlepages.com/

Hope I can get mine that polished up !! BLING BLING !
Edit : fixed the picture viewing.