Sharp eyes above will also notice that I rounded the cylinder.
The way to do this was with my rotary table, so I first indicated both Y & Z along the phantom lines with my Interapid. I had about a 2-inch run without hitting the outer chamfer or the centering ring so I was able to get it pretty close.
Next I gripped one end of the cylinder in my split bushing and used the lathe to get the 4-jaw close. I later fine tuned it on the RT because I know the threaded chuck mount misses center by a thou or two. Some beginners can be intimidated by a 4-jaw independent chuck but I find it is actually pretty easy to use. eyeballing the alignment within .010 with a bit of practice is quite doable and truing it up from there is pretty quick.
In the left image below I am zeroing the indicator with one pair of jaws horizontal. Once I do that I use the hex key to rotate it 180 and note the runout, shown on the right side at about .008. I now insert a ball driver into the far chuck and tweek the two jaws at the same time to split the difference. With that done I rotate the chuck 90 and repeat with the second jaw pair. A final check on the first pair will usually show it well within what I need before moving it to the rotary table for final truing. I've done it a few times now and can get to within .001 TIR within a minute or so. Not as fast as a centering 3-jaw, but a lot more accurate.
With the chuck moved I have to spin the RT to fine tune the centering and this is a great excuse for a CNC RT. I wouldn't want to hand crank it around too many times centering the chuck.
You can see below that I used one of the aluminum heads and Sherline's adjustable tail stock to support the outer end of the cylinder. I don't know if it was necessary with my light cuts, but it did make me feel better. No point risking that many hours to find out I should have...
I hand-wrote a little G-code file to clean off the corner of the cylinder first at 45 degrees to the original reductions and ultimately stepping around to 16 facets through the 90 degrees. From here a little quick file work got it ready for primer.
As always, let me know if you have any questions or if I am doing anything wrong.
The way to do this was with my rotary table, so I first indicated both Y & Z along the phantom lines with my Interapid. I had about a 2-inch run without hitting the outer chamfer or the centering ring so I was able to get it pretty close.
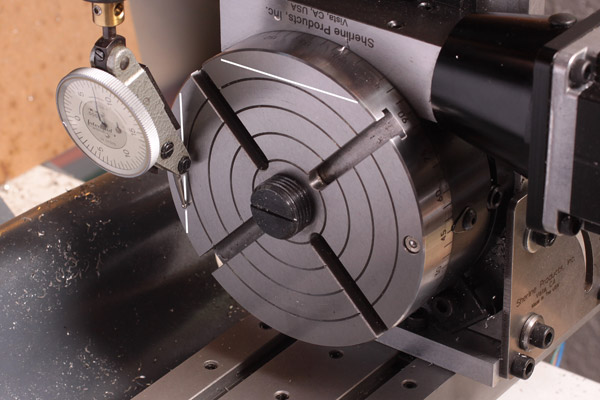
Next I gripped one end of the cylinder in my split bushing and used the lathe to get the 4-jaw close. I later fine tuned it on the RT because I know the threaded chuck mount misses center by a thou or two. Some beginners can be intimidated by a 4-jaw independent chuck but I find it is actually pretty easy to use. eyeballing the alignment within .010 with a bit of practice is quite doable and truing it up from there is pretty quick.
In the left image below I am zeroing the indicator with one pair of jaws horizontal. Once I do that I use the hex key to rotate it 180 and note the runout, shown on the right side at about .008. I now insert a ball driver into the far chuck and tweek the two jaws at the same time to split the difference. With that done I rotate the chuck 90 and repeat with the second jaw pair. A final check on the first pair will usually show it well within what I need before moving it to the rotary table for final truing. I've done it a few times now and can get to within .001 TIR within a minute or so. Not as fast as a centering 3-jaw, but a lot more accurate.
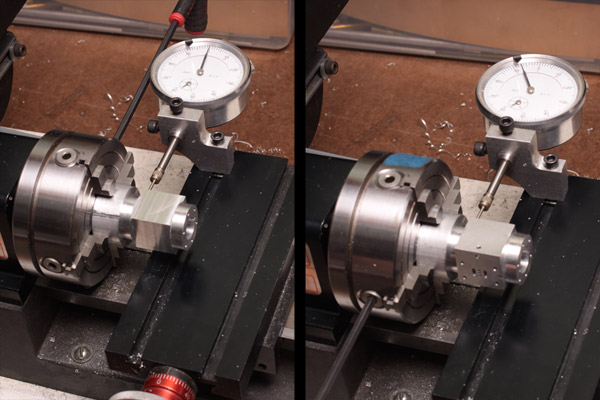
With the chuck moved I have to spin the RT to fine tune the centering and this is a great excuse for a CNC RT. I wouldn't want to hand crank it around too many times centering the chuck.
You can see below that I used one of the aluminum heads and Sherline's adjustable tail stock to support the outer end of the cylinder. I don't know if it was necessary with my light cuts, but it did make me feel better. No point risking that many hours to find out I should have...
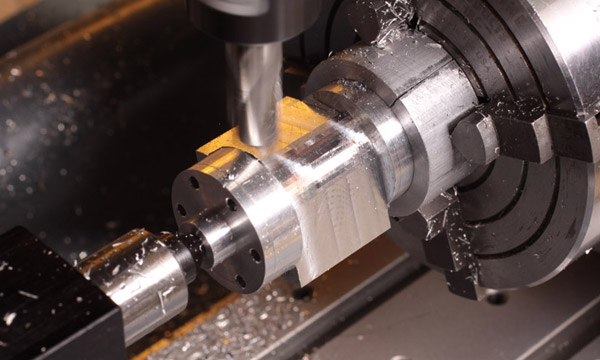
I hand-wrote a little G-code file to clean off the corner of the cylinder first at 45 degrees to the original reductions and ultimately stepping around to 16 facets through the 90 degrees. From here a little quick file work got it ready for primer.
As always, let me know if you have any questions or if I am doing anything wrong.
Last edited: