Now we're going to engage in a little foolery here. The part shown is part #1 of a theoretical reversing valve. All you really need to know is that with an oscillating engine, if you put air in port "A" and let the air go thru the engine and come out port "B" the engine will revolve clockwise. However, if you put the air in thru port "B" and let it run thru the engine and out port "A", the engine will revolve counter-clockwise. The third hole with no designation is going to be a pivot for a reversing lever.---Use your imagination---It helps.
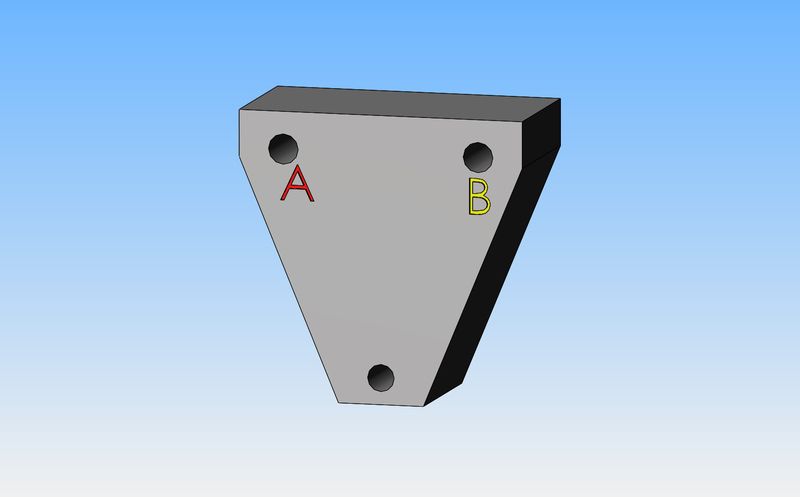