Hi everybody!
I'm making this thread of gratitude to this forum.
I'm currently working on my BS in Mechanical Engineering, as the final exam in 3D-modelling my class was given the task to make "a steam driven engine" in SolidWorks, either a copy of a working design or something new. My search for inspiration lead me to this forum where I've beed inspirated and educated.
Since English is my second language, I hope you will excuse my grammar.
I hope the radial makers of this forum does not feel "ripped off" that i have used their designs and buildthreads as guide and inspiration. (The model is only used for academic purposes)
As you may see my main inspiration has been theese threads
Time for a Radial and Radial Updates) and I therefore want to give a special thanks to the creator of those threads: cfellows.
General information:
The model is intended to be a medium/large size "table-model" of a radial engine. The pistons are Ø50mm, that should say something about the size.
Materials used are: Copper, Aluminium 3003-H18 and some Stainless 316. (Fasteners not included)
The total mass is aprox 40Kg. The base-plate may be more massive than it needs to be.
The propeller is here presented in rosewood, but was designed to be in aluminium and would serve as a counterweight.
Here is the assembly of the 5-cylinder radial, I hope this thread will serve as inspiration to others as this forums has inspired me.
The variation of scenes and light may give different visual apperances.
Brass and polished aluminium look.
A bit more realistic copper and alu look.
With cylinder transparency.
Section of cylinder. Shows ball-bearing exhaustvalve as seen in among others, the Halo engine.
Details
I'm making this thread of gratitude to this forum.
I'm currently working on my BS in Mechanical Engineering, as the final exam in 3D-modelling my class was given the task to make "a steam driven engine" in SolidWorks, either a copy of a working design or something new. My search for inspiration lead me to this forum where I've beed inspirated and educated.
Since English is my second language, I hope you will excuse my grammar.
I hope the radial makers of this forum does not feel "ripped off" that i have used their designs and buildthreads as guide and inspiration. (The model is only used for academic purposes)
As you may see my main inspiration has been theese threads
General information:
The model is intended to be a medium/large size "table-model" of a radial engine. The pistons are Ø50mm, that should say something about the size.
Materials used are: Copper, Aluminium 3003-H18 and some Stainless 316. (Fasteners not included)
The total mass is aprox 40Kg. The base-plate may be more massive than it needs to be.
The propeller is here presented in rosewood, but was designed to be in aluminium and would serve as a counterweight.
Here is the assembly of the 5-cylinder radial, I hope this thread will serve as inspiration to others as this forums has inspired me.
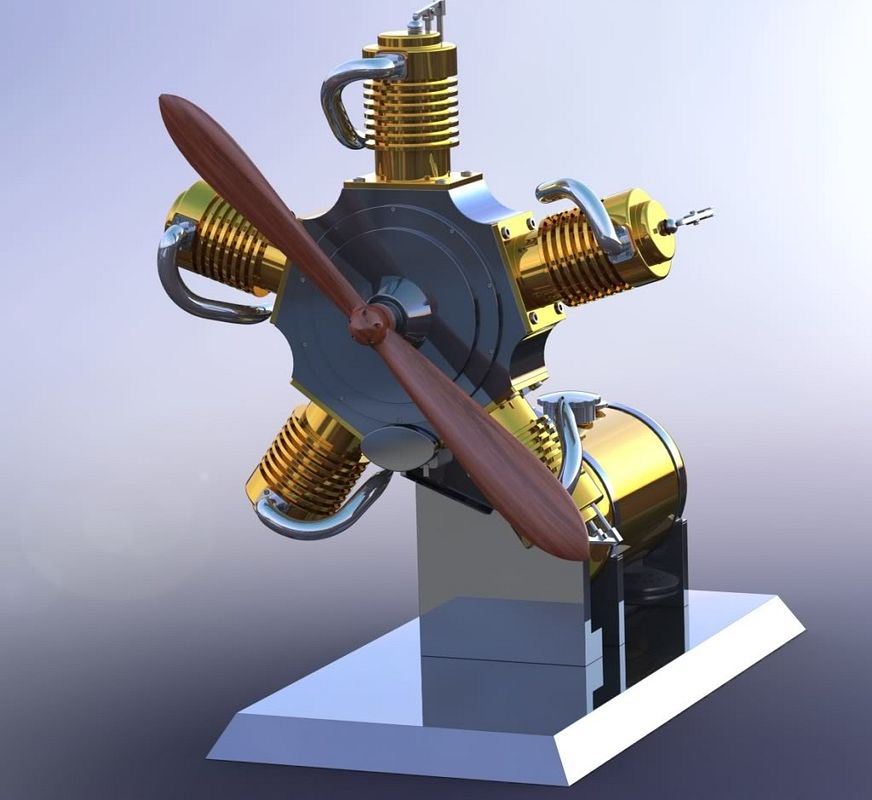
The variation of scenes and light may give different visual apperances.
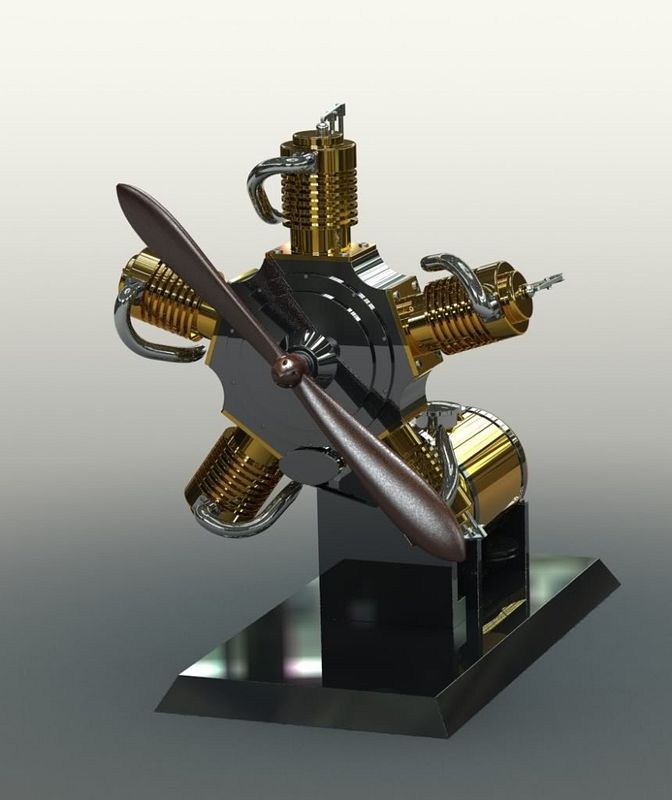
Brass and polished aluminium look.
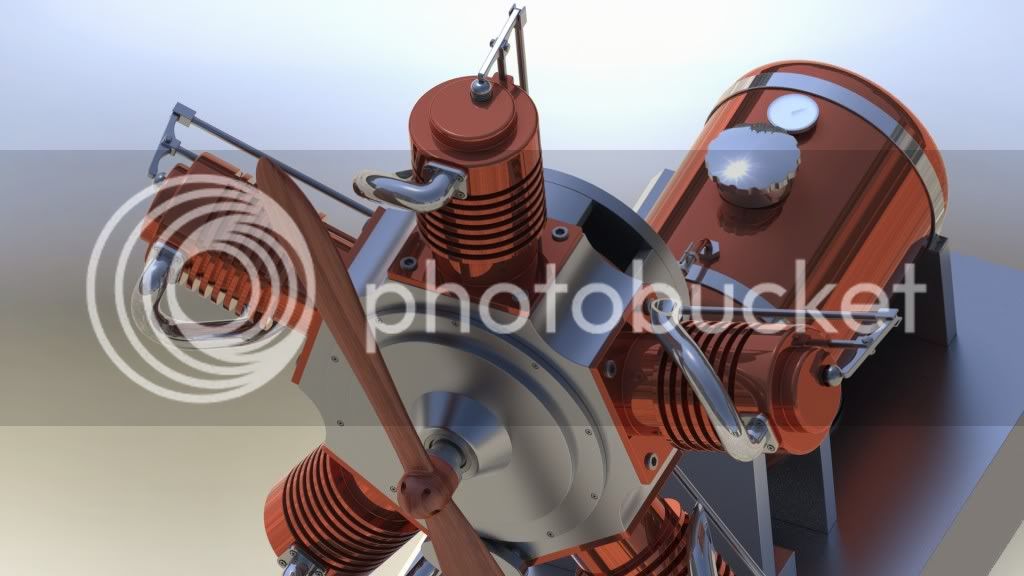
A bit more realistic copper and alu look.
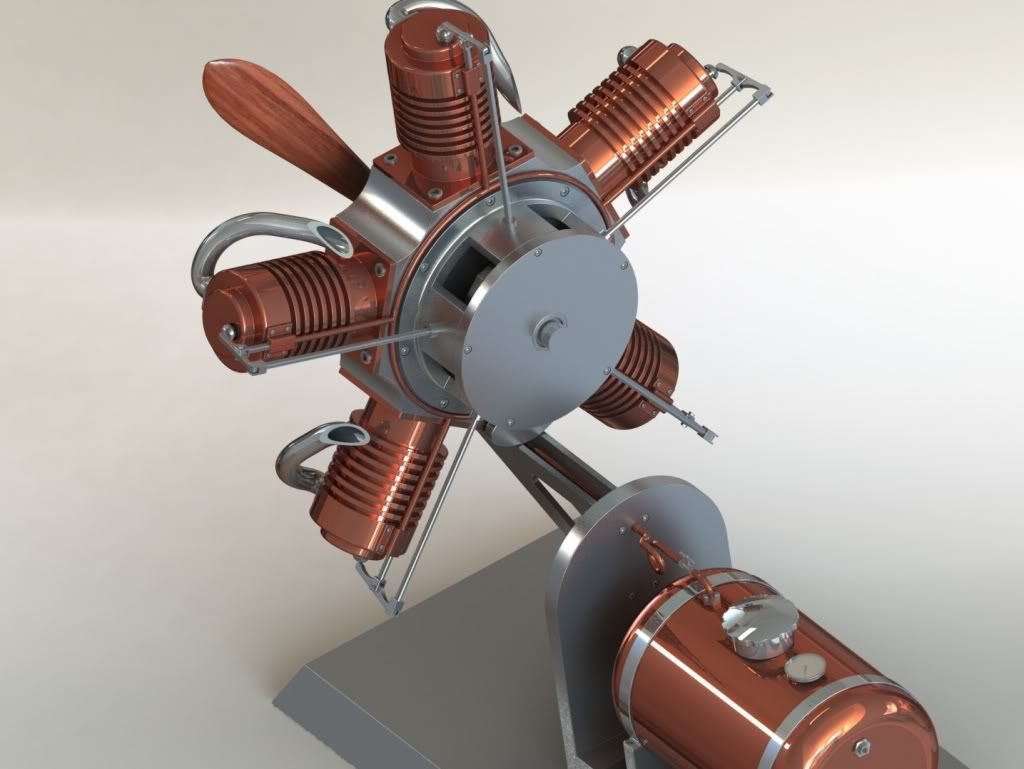
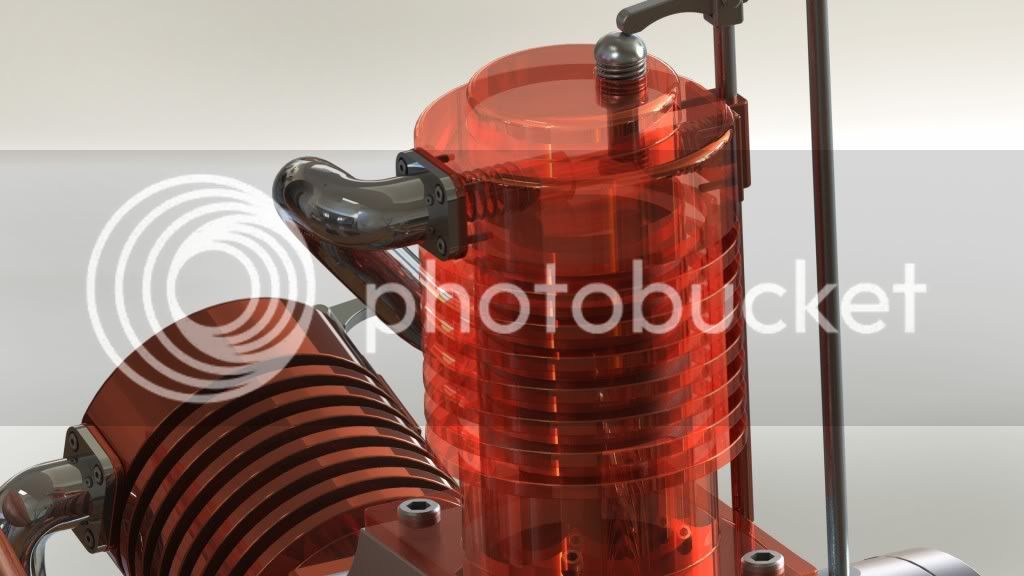
With cylinder transparency.
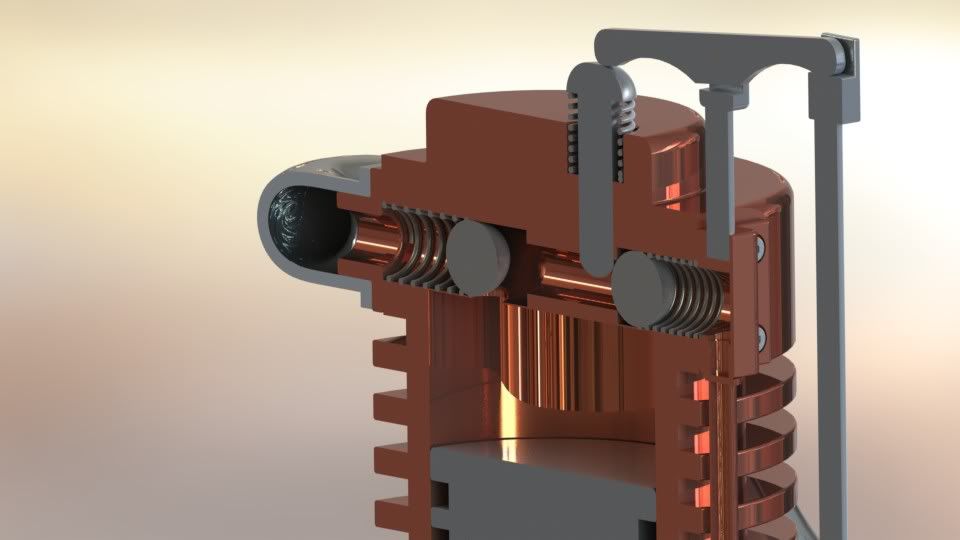
Section of cylinder. Shows ball-bearing exhaustvalve as seen in among others, the Halo engine.
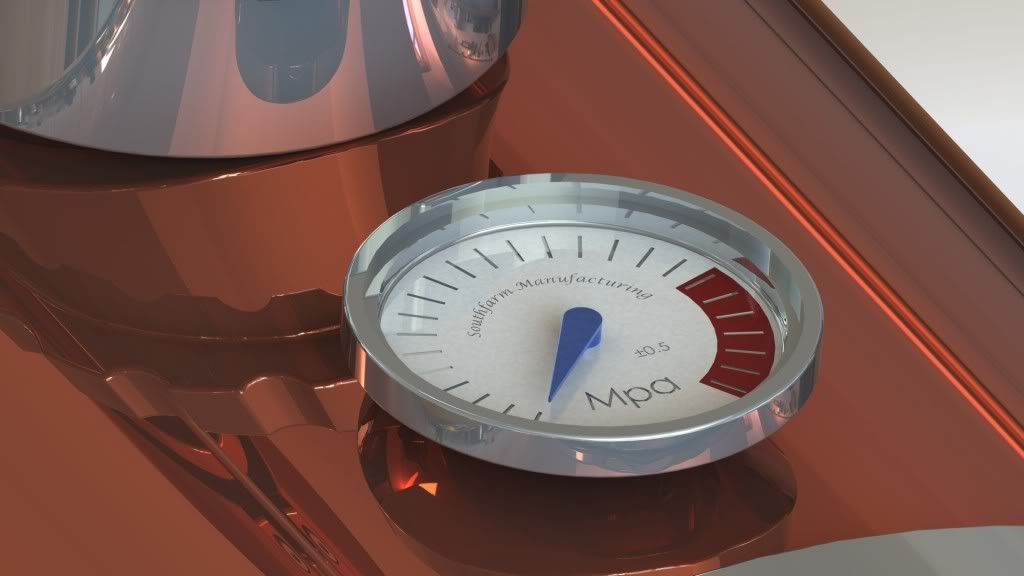
Details