arnoldb
Well-Known Member
- Joined
- Apr 8, 2009
- Messages
- 1,792
- Reaction score
- 12
Well, Saturday turned into a no-shop day for me, so I got an early start this morning.
First up was a new stand for the pump. This stainless steel is a bit of a challenge to work; I found that wit LOTS of synthetic oil/water coolant and aggressive feed it works well. First I drilled a 5mm pilot hole, then the plunged the 12mm drill bit through at lowest speed on my drill press (220RPM). A photo after I finished drilling the 12mm hole for the pump body in the new block; the white puddles is the coolant:
I also drilled out holes for the top link mounting, and a 5mm hole on the side for threading M6 for a grub screw to hold the pump cylinder in place. My bandsaw didn't like the stainless very much either; normally it cuts pretty square, but at the top and bottom of the piece you can see how the cut ran off at an angle when I cut the block from bar:
After that I hacksawed most of the excess metal off around the link connection, and milled away the rest; slowest high-range speed on the Myford, once again with lots of coolant. This time things worked out ;D. I turned the base of the stand square with the 4-jaw - and the stand was finished. Some brass plate and bar was sawn and filed to shape for the handle and linkages, stainless steel pins turned up and threaded, and a new brass fork for the piston-handle connection made. No photos; I got too busy and was working at a good clip.
Next up was the 2 valves, also from stainless rod; simple turning job with the collet chuck, and then using 3 marks in the collet nut as "basic indexing" and some filing with a small flat file; three flats on each valve. Parted off, and clamped in toolmaker's clamp then in big vice, and used a hacksaw to cut 2 grooves on the top of each valve; then some more filing for additional clearance on the valve top. A photo of one of the finished valves:
A quick assembly of the lot and a test in a bowl of water and it pumps ;D - I don't know to what pressure yet, as I still have to do some plumbing work for that, but was out of time for today:
I'll most likely be quiet until next Saturday, as I'm flying to Johannesburg tomorrow for a week-long course, with very limited - if any - Internet connectivity.
Regards, Arnold
First up was a new stand for the pump. This stainless steel is a bit of a challenge to work; I found that wit LOTS of synthetic oil/water coolant and aggressive feed it works well. First I drilled a 5mm pilot hole, then the plunged the 12mm drill bit through at lowest speed on my drill press (220RPM). A photo after I finished drilling the 12mm hole for the pump body in the new block; the white puddles is the coolant:
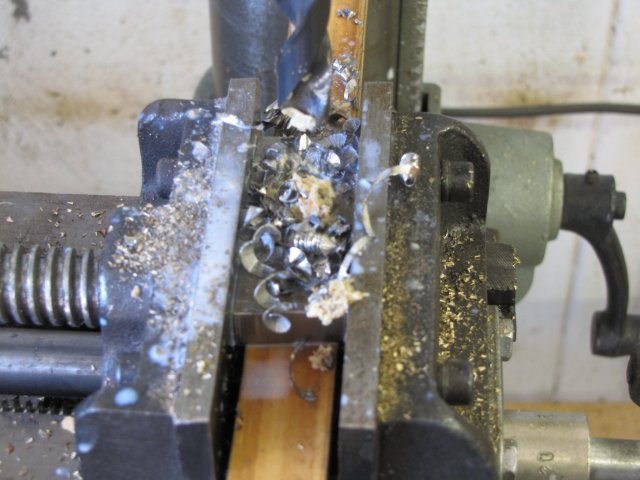
I also drilled out holes for the top link mounting, and a 5mm hole on the side for threading M6 for a grub screw to hold the pump cylinder in place. My bandsaw didn't like the stainless very much either; normally it cuts pretty square, but at the top and bottom of the piece you can see how the cut ran off at an angle when I cut the block from bar:
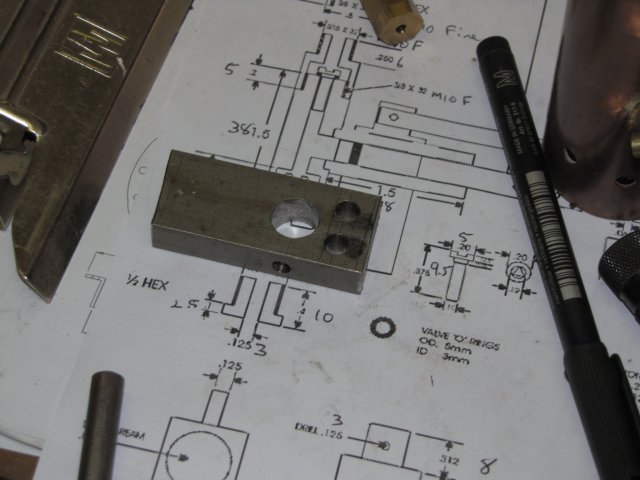
After that I hacksawed most of the excess metal off around the link connection, and milled away the rest; slowest high-range speed on the Myford, once again with lots of coolant. This time things worked out ;D. I turned the base of the stand square with the 4-jaw - and the stand was finished. Some brass plate and bar was sawn and filed to shape for the handle and linkages, stainless steel pins turned up and threaded, and a new brass fork for the piston-handle connection made. No photos; I got too busy and was working at a good clip.
Next up was the 2 valves, also from stainless rod; simple turning job with the collet chuck, and then using 3 marks in the collet nut as "basic indexing" and some filing with a small flat file; three flats on each valve. Parted off, and clamped in toolmaker's clamp then in big vice, and used a hacksaw to cut 2 grooves on the top of each valve; then some more filing for additional clearance on the valve top. A photo of one of the finished valves:
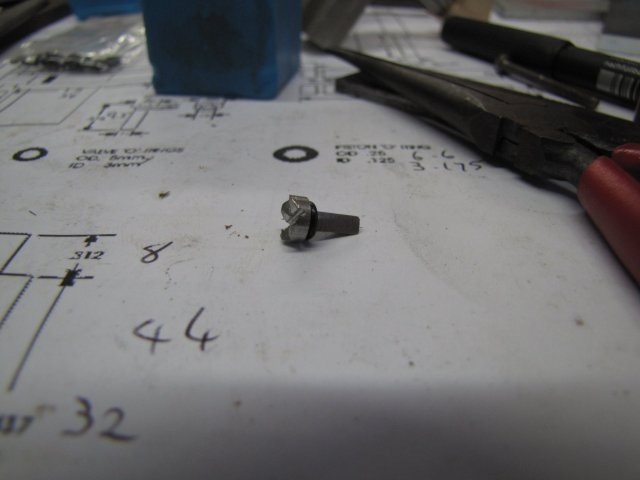
A quick assembly of the lot and a test in a bowl of water and it pumps ;D - I don't know to what pressure yet, as I still have to do some plumbing work for that, but was out of time for today:
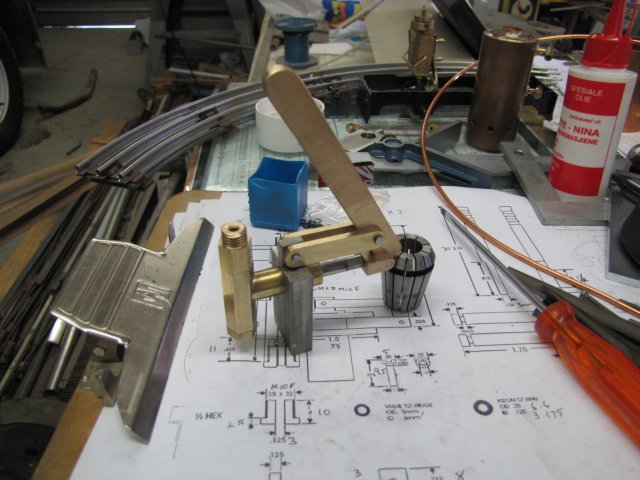
I'll most likely be quiet until next Saturday, as I'm flying to Johannesburg tomorrow for a week-long course, with very limited - if any - Internet connectivity.
Regards, Arnold