arnoldb
Well-Known Member
- Joined
- Apr 8, 2009
- Messages
- 1,792
- Reaction score
- 12
Well, the weekend's gone and there are still loose ends. Fortunately the chuck adapter is done.
I started by turning a ring from some scrap HRS rod - for a light push fit into the "register" hole I bored in the RT's table. Here, it's done and I'm about to part it off:
The ring's purpose will become clear later...
Then I chucked the assembly I made yesterday in the 4-jaw, and roughly centered it - checking that I would need to remove a minimum of metal from the bottom to face it. I then faced it, drilled and reamed a 12mm hole through the center, and bored out a section to fit the ring made earlier, but with the ring a slightly tighter push fit; easily removable, but not inclined to fall out on its own:
Next I cheated a bit. The workpiece has to be accurately turned around and re-mounted to keep both concentricity and axial alignment to the mounting face. I know that my lathe's tailstock and drill chuck is VERY close to perfect alignment with the spindle - less than 0.005mm out on offset, and extremely accurate in line - I can't even measure this. So instead of setting the job up in the 4-jaw and centering it, I mounted the face plate, and with a bit of 12mm silver steel chucked in the tailstock, used it to mount the workpiece to the face plate. No mess, no fuss, and as well aligned as I could have made it with the 4-jaw; just a LOT quicker ;D :
Then I proceeded to face this side of the mounting as well; not really needed, but does look neater, and then turned a spindle nose replica of my lathe on the front section, leaving a bit of clearance so that a mounted chuck will not come into contact with cap screws used for mounting the adapter to the table. I didn't take photos of the process, as I thought I'd just link to a similar adapter I made when I built my collet chuck Turns out, back then I forgot to take some photos :-[ Next time, I won't forget.
This was the end result of the operations:
Just for fun, I put the RT to use to clean up the ugly ends of the adapter:
I'm very glad I did this trial run; it uncovered some hiccups - easily addressed once I do a strip and re-assembly of the RT. For one, the pre-load on the bearing is not enough as it is assembled now. I had the grub screws holding the worm and the wheel come loose from vibration, so at next assembly, I'll use some thread locker on them.
This is what the lot looks like with my 3-jaw chuck mounted on it:
I was wondering how I am going to keep my chucks from unscrewing from the adapter while in use, and I already had a whacky idea drawn up - but I'm not going to use it... Seeing everything assembled like this, a far simpler idea struck me; it will be easy to make "clamps" that can be mounted in the unoccupied T-slots on the table that will both lock the chuck as well as add some additional rigidity :
Regards, Arnold
I started by turning a ring from some scrap HRS rod - for a light push fit into the "register" hole I bored in the RT's table. Here, it's done and I'm about to part it off:
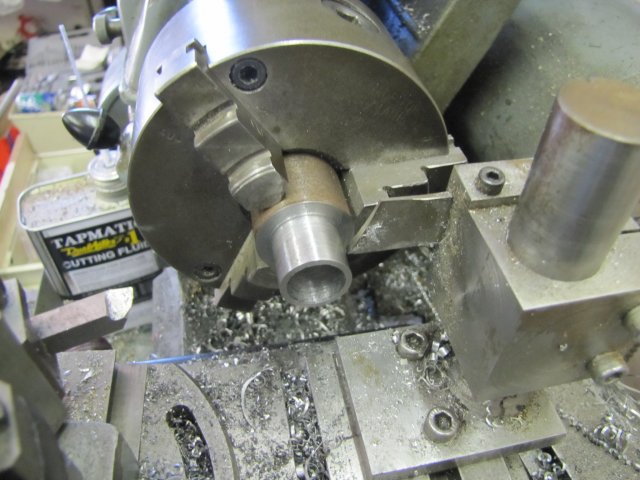
The ring's purpose will become clear later...
Then I chucked the assembly I made yesterday in the 4-jaw, and roughly centered it - checking that I would need to remove a minimum of metal from the bottom to face it. I then faced it, drilled and reamed a 12mm hole through the center, and bored out a section to fit the ring made earlier, but with the ring a slightly tighter push fit; easily removable, but not inclined to fall out on its own:
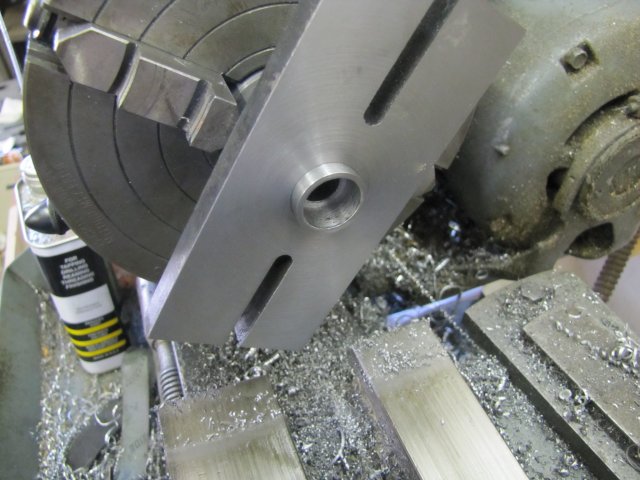
Next I cheated a bit. The workpiece has to be accurately turned around and re-mounted to keep both concentricity and axial alignment to the mounting face. I know that my lathe's tailstock and drill chuck is VERY close to perfect alignment with the spindle - less than 0.005mm out on offset, and extremely accurate in line - I can't even measure this. So instead of setting the job up in the 4-jaw and centering it, I mounted the face plate, and with a bit of 12mm silver steel chucked in the tailstock, used it to mount the workpiece to the face plate. No mess, no fuss, and as well aligned as I could have made it with the 4-jaw; just a LOT quicker ;D :
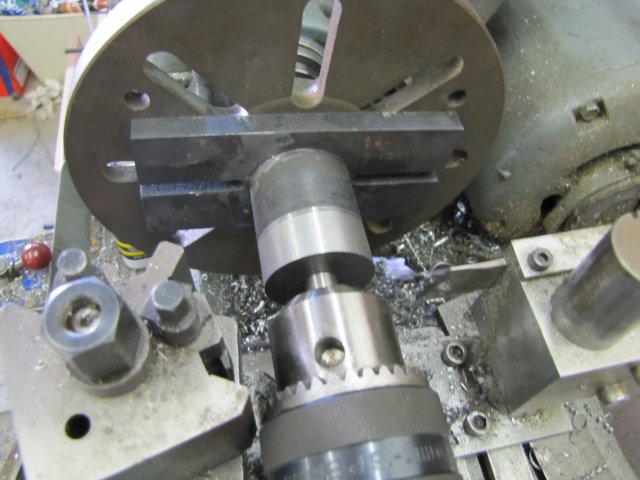
Then I proceeded to face this side of the mounting as well; not really needed, but does look neater, and then turned a spindle nose replica of my lathe on the front section, leaving a bit of clearance so that a mounted chuck will not come into contact with cap screws used for mounting the adapter to the table. I didn't take photos of the process, as I thought I'd just link to a similar adapter I made when I built my collet chuck Turns out, back then I forgot to take some photos :-[ Next time, I won't forget.
This was the end result of the operations:
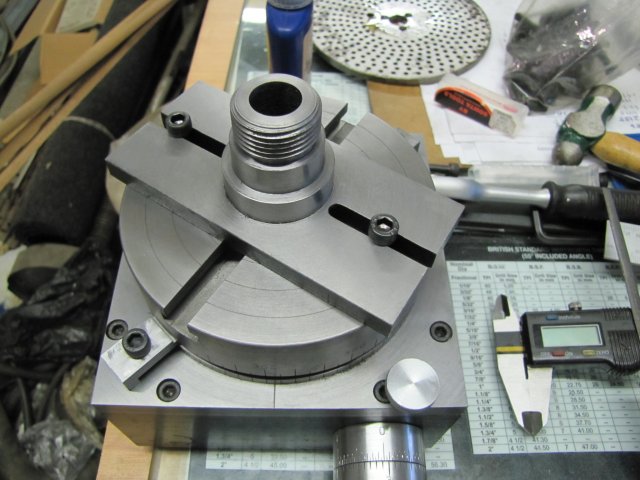
Just for fun, I put the RT to use to clean up the ugly ends of the adapter:
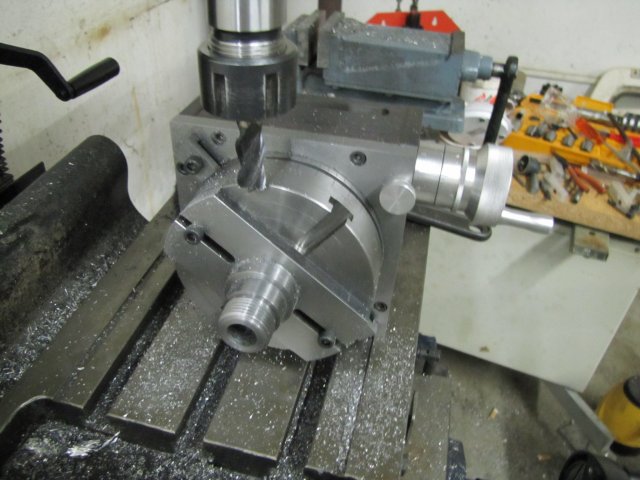
I'm very glad I did this trial run; it uncovered some hiccups - easily addressed once I do a strip and re-assembly of the RT. For one, the pre-load on the bearing is not enough as it is assembled now. I had the grub screws holding the worm and the wheel come loose from vibration, so at next assembly, I'll use some thread locker on them.
This is what the lot looks like with my 3-jaw chuck mounted on it:
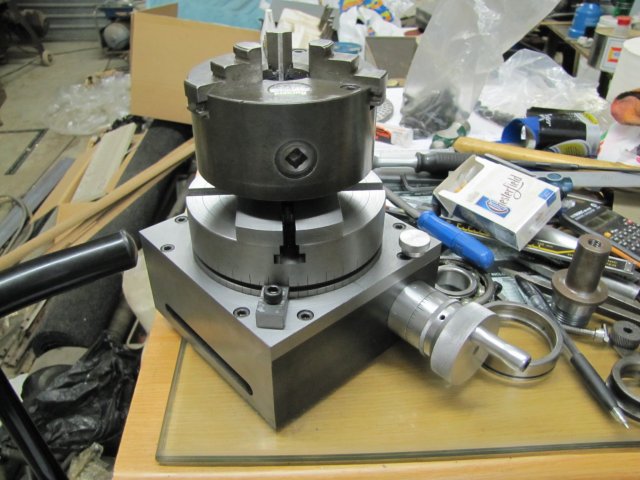
I was wondering how I am going to keep my chucks from unscrewing from the adapter while in use, and I already had a whacky idea drawn up - but I'm not going to use it... Seeing everything assembled like this, a far simpler idea struck me; it will be easy to make "clamps" that can be mounted in the unoccupied T-slots on the table that will both lock the chuck as well as add some additional rigidity :
Regards, Arnold