- Joined
- Nov 12, 2009
- Messages
- 1,427
- Reaction score
- 221
Got a little bit done this weekend.
The big end Caps are installed now so I started on the flywheel from a bit of scrap.
I have not done the 10 degree internal taper yet as the smallest boring bar ive got is 3/8,
dont ya just love cast iron :big:
Pete
The big end Caps are installed now so I started on the flywheel from a bit of scrap.
I have not done the 10 degree internal taper yet as the smallest boring bar ive got is 3/8,
dont ya just love cast iron :big:
Pete
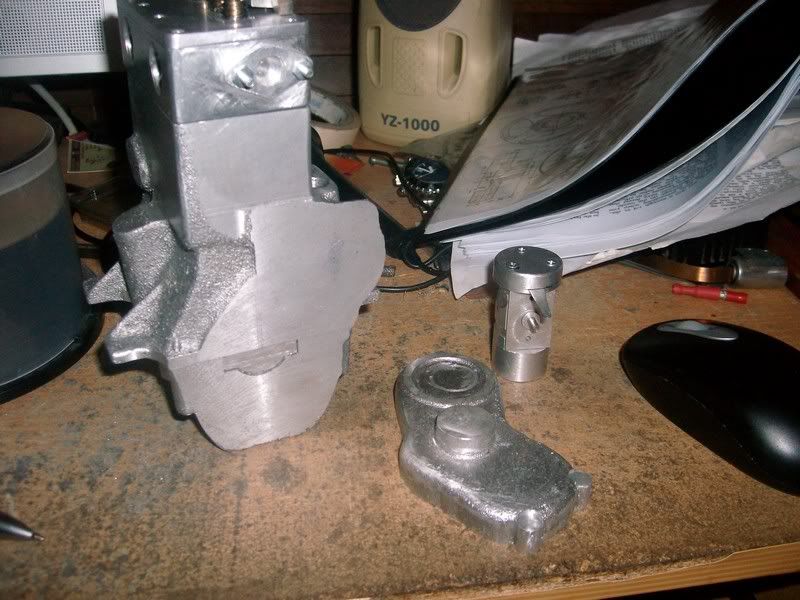
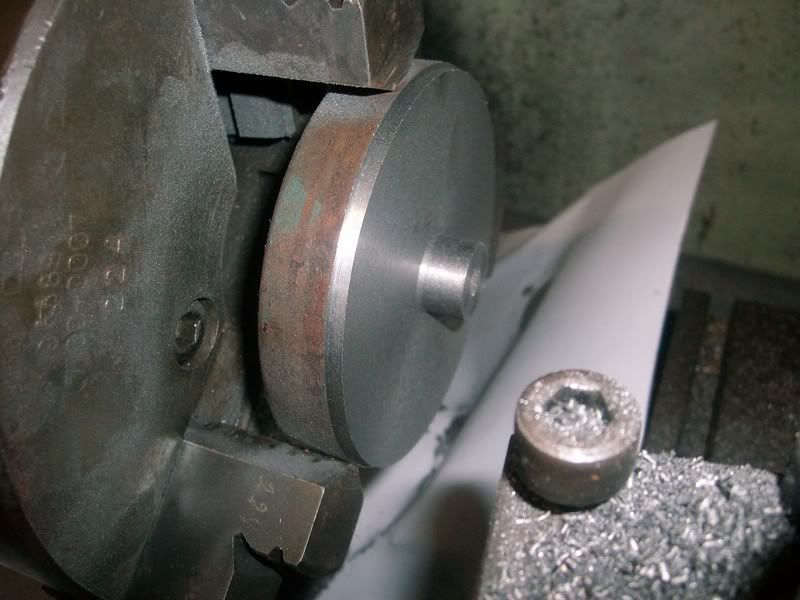
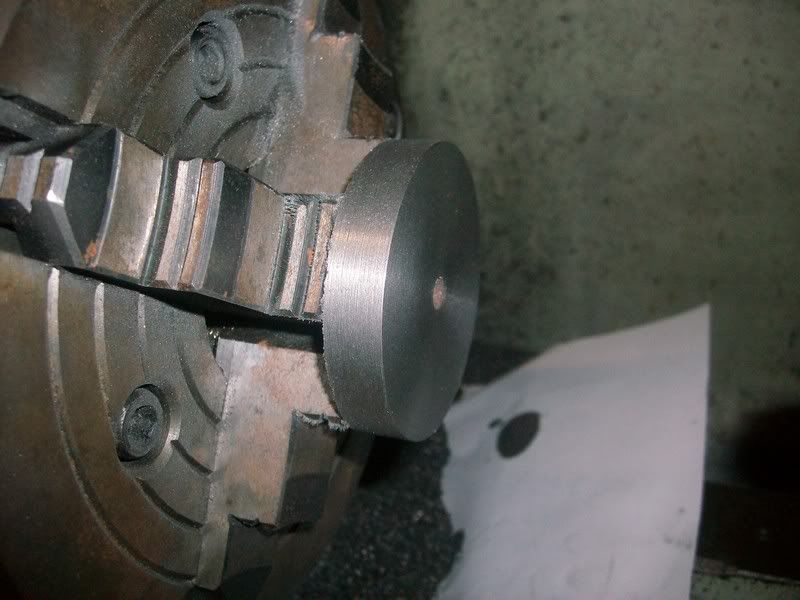