Xlmyford
Well-Known Member
- Joined
- Mar 8, 2009
- Messages
- 97
- Reaction score
- 4
Hello.
In November I´ve started my new project.It´s a steam engine, based on drawings by Mr.Erich Jenczok.
Since then,I did some of the necessary parts already.
In the forefront,I had some respect, not to say fear of fabricating the main block,drilling all the steam holes.Fortunately,it worked out very well.
To save some money,I used aluminum for the cylinder block and locktited brass liners into it.
The only real disaster I experienced, has been a broken M2 tap, while tapping hole 11 or 12.
Because of that evil beast of tap,which is still laughing at me from the hole,I had to drill some new holes around the right cylinder.To avoid asymmetry, I did the same to the left one.
Some of the parts I made.
A new experience has been excentric turning.
I did it that way.
The first thing I did,was turning a piece of stainless down to 16mm.
On the mill,looking for the center.
2.7 mm out of center,that´s what the drawing said.
center drilled
drilled out to 5mm.Gentlemen,please regard my automatic brush lubrication system
Back to the lathe,finding the center of the excentric hole by two dead centers and a dial indicator.
I took the parting tool to turn the excenter.
and a very moderate feed rate.
Nevertheless,at the beginning it banged hefty.
Low revs.
Voila,the excenter.Looks good to me.
Looking for the "normal" middle again,
to cut the groove.
Parting off
Next part to make will be the crank shaft.
I hope my English is not too bad and that this report is not boring you too much.
Ralph
t.b.c.
In November I´ve started my new project.It´s a steam engine, based on drawings by Mr.Erich Jenczok.
Since then,I did some of the necessary parts already.
In the forefront,I had some respect, not to say fear of fabricating the main block,drilling all the steam holes.Fortunately,it worked out very well.
To save some money,I used aluminum for the cylinder block and locktited brass liners into it.
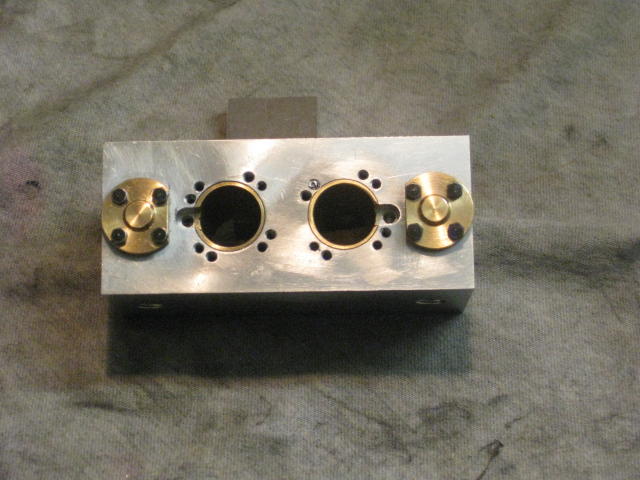
The only real disaster I experienced, has been a broken M2 tap, while tapping hole 11 or 12.
Because of that evil beast of tap,which is still laughing at me from the hole,I had to drill some new holes around the right cylinder.To avoid asymmetry, I did the same to the left one.

Some of the parts I made.
A new experience has been excentric turning.
I did it that way.
The first thing I did,was turning a piece of stainless down to 16mm.
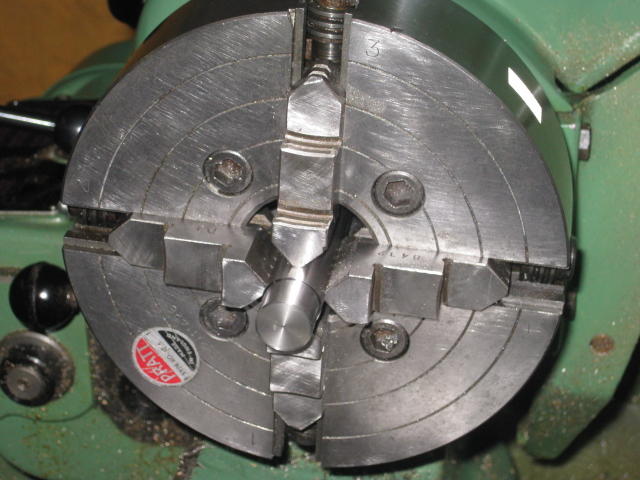
On the mill,looking for the center.
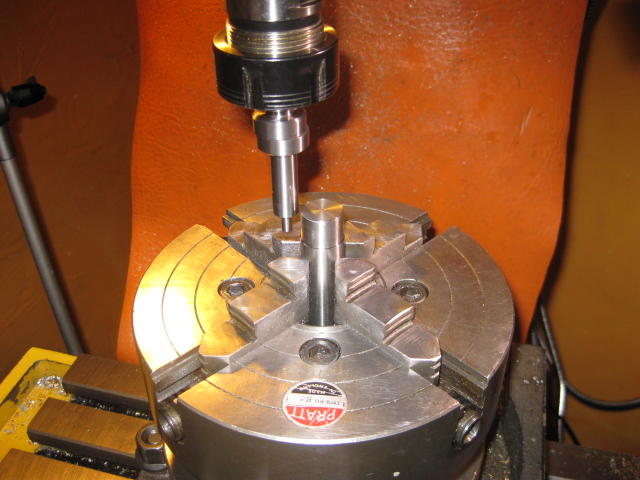
2.7 mm out of center,that´s what the drawing said.
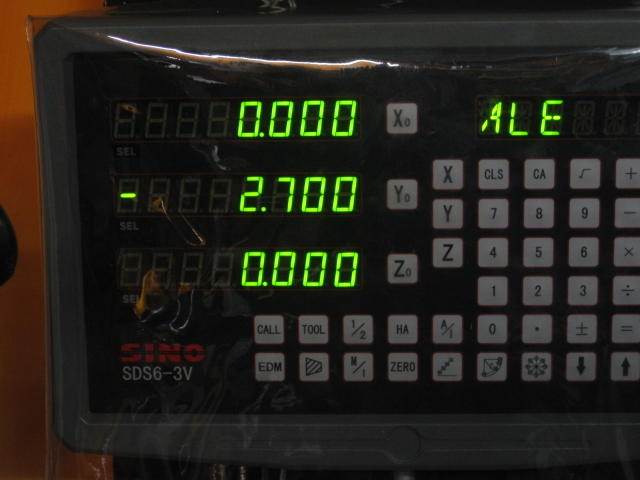
center drilled
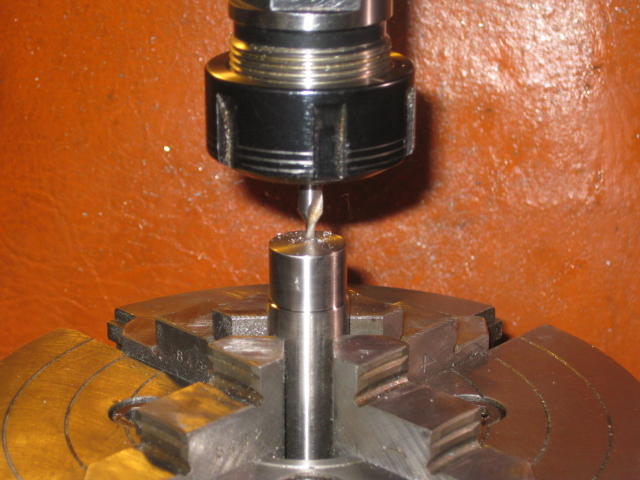
drilled out to 5mm.Gentlemen,please regard my automatic brush lubrication system
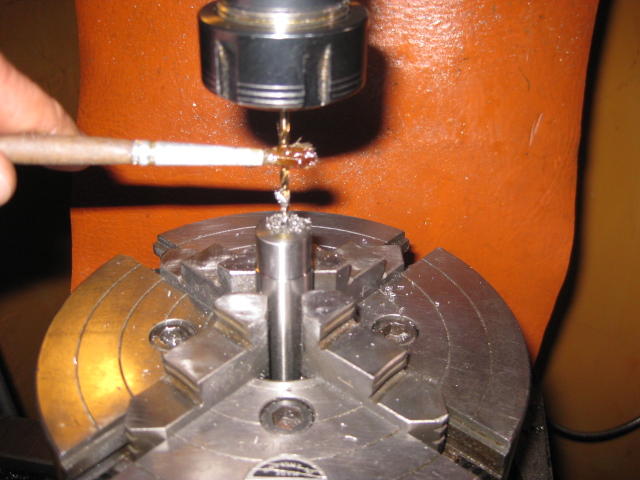
Back to the lathe,finding the center of the excentric hole by two dead centers and a dial indicator.
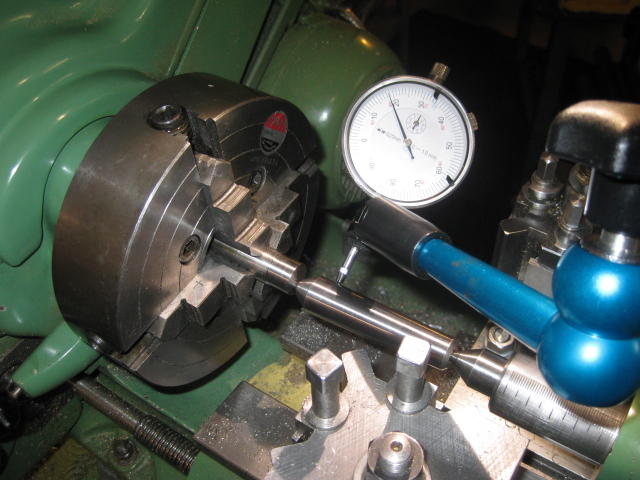
I took the parting tool to turn the excenter.
and a very moderate feed rate.
Nevertheless,at the beginning it banged hefty.
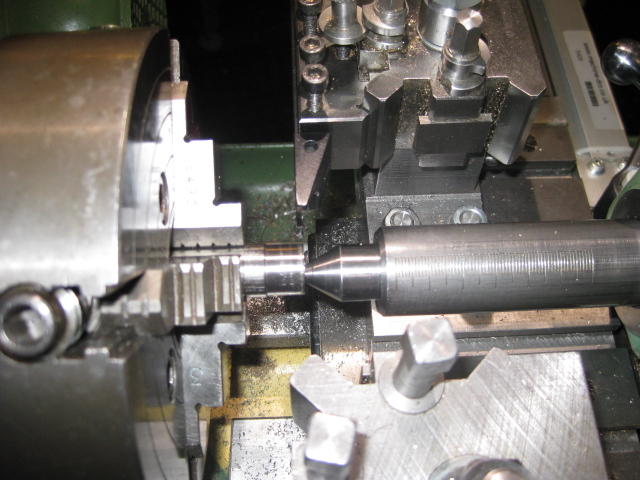
Low revs.
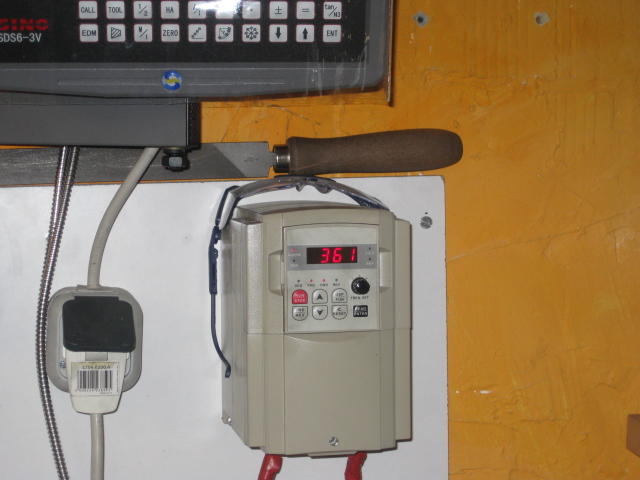
Voila,the excenter.Looks good to me.
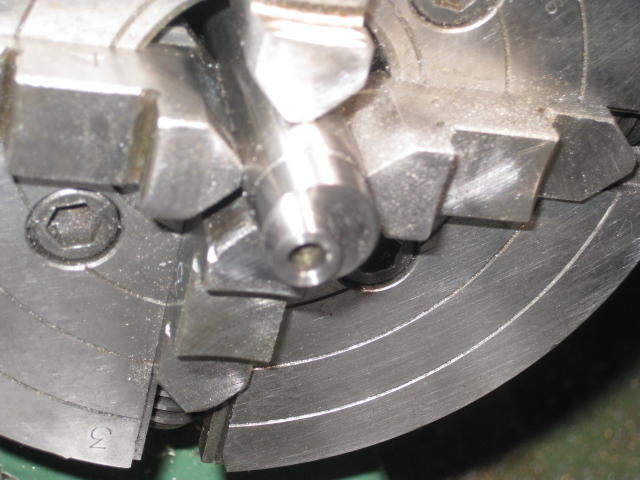
Looking for the "normal" middle again,
to cut the groove.
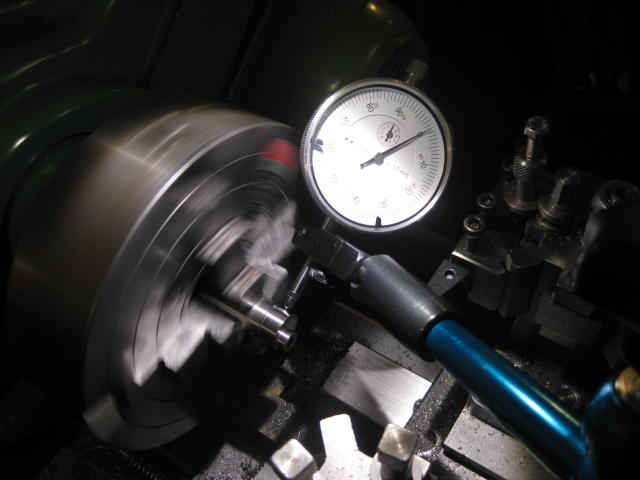
Parting off
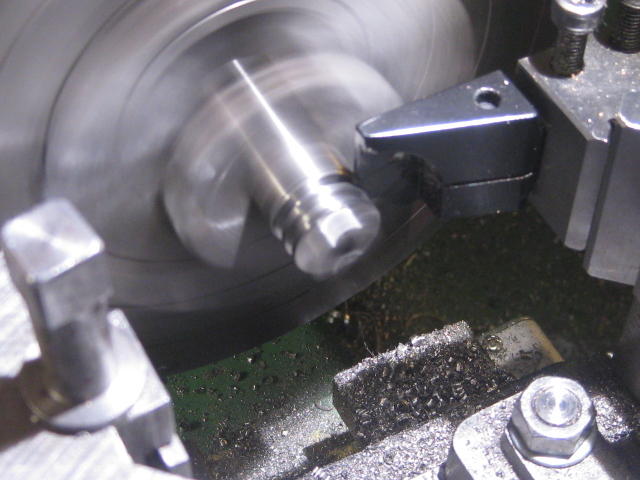
Next part to make will be the crank shaft.
I hope my English is not too bad and that this report is not boring you too much.
Ralph
t.b.c.