Harold Lee
Well-Known Member
- Joined
- Apr 23, 2008
- Messages
- 236
- Reaction score
- 2
Rudy, Doc and Jeff - I appreciate your encouragement. I am also getting anxious to see it run but that will wait a few more days (weeks?). One comment and a question regarding the collet. There are three holes that are tapped on the flywheel for tightening everything up. There are three holes that are tapped on the collet for removing the flywheel. While the following step would be purely cosmetic I was wonder if the three tapped holes should have short bolts put in them. If I wanted to remove the collet the three dummy bolts would be removed and the three longer bolts put in their place.... Pondering...
Today I was able to complete the valve bodies. The first step was to put a .125 mandrel in the valve stem hole and use that as a reference for truing up the part in the four jaw chuck.
After that the valve guide was turned to dimensions.
After this was completed the part was moved to the mill to locate, drill, and in some cases tap the holes.
After all of the holes were completed the part was milled to final dimensions and the sides were beveled.
At this point the valve bodies are complete. The remaining work on this part of the engine is to make the valve keepers and the valve cover plates.
All in all a pretty good day...
Today I was able to complete the valve bodies. The first step was to put a .125 mandrel in the valve stem hole and use that as a reference for truing up the part in the four jaw chuck.
After that the valve guide was turned to dimensions.
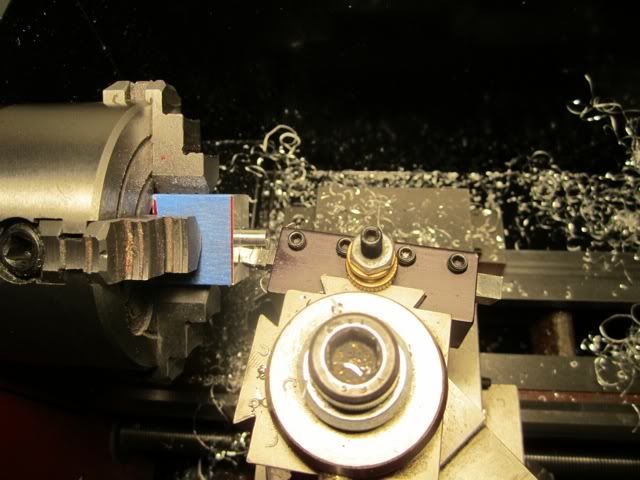

After this was completed the part was moved to the mill to locate, drill, and in some cases tap the holes.
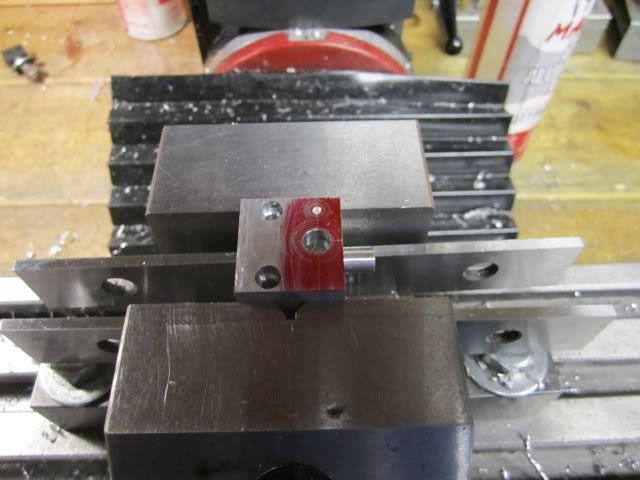
After all of the holes were completed the part was milled to final dimensions and the sides were beveled.
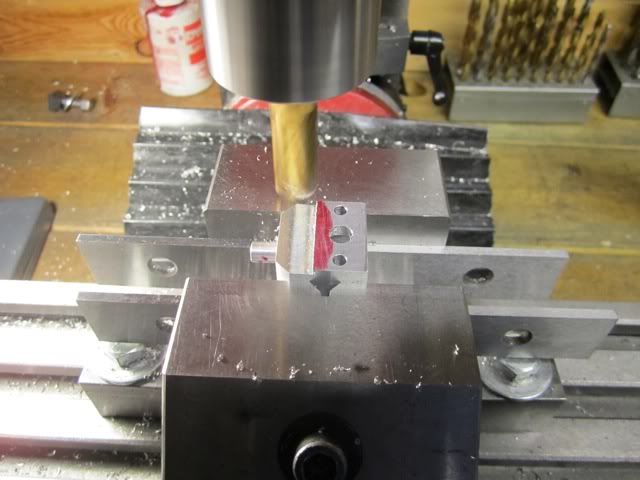
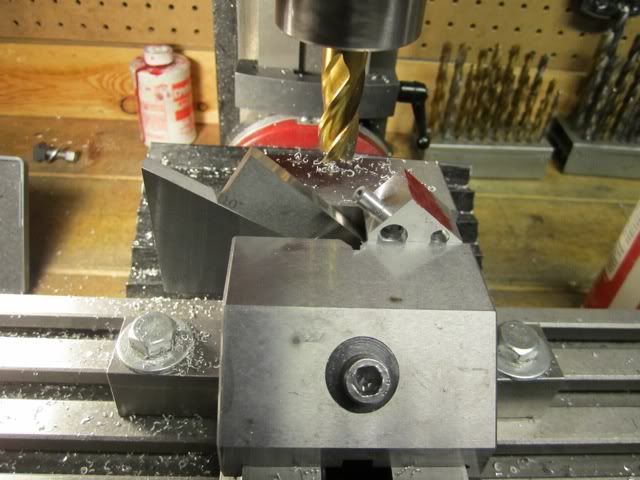
At this point the valve bodies are complete. The remaining work on this part of the engine is to make the valve keepers and the valve cover plates.
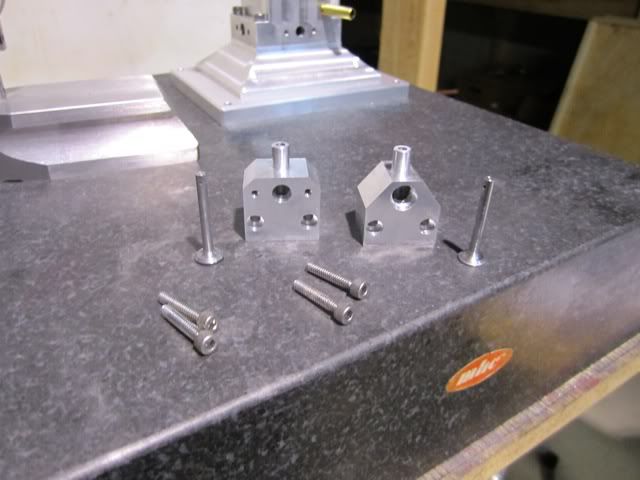
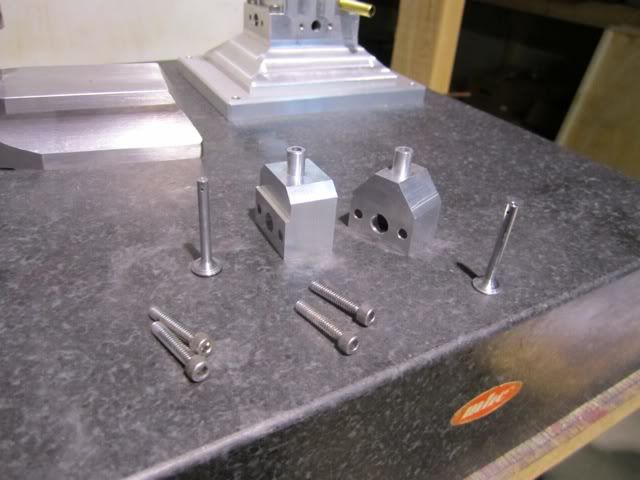
All in all a pretty good day...
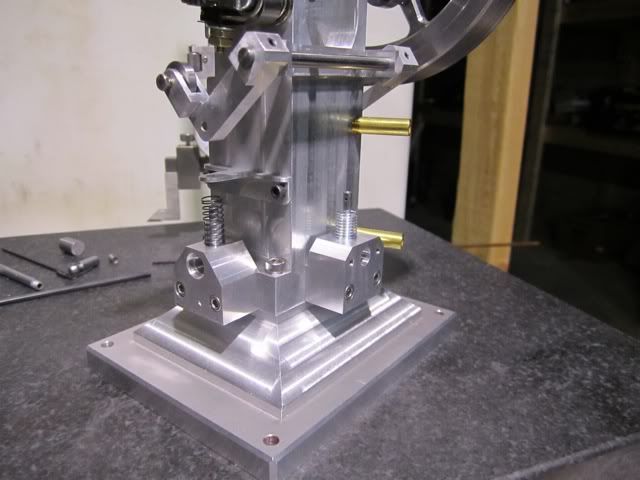
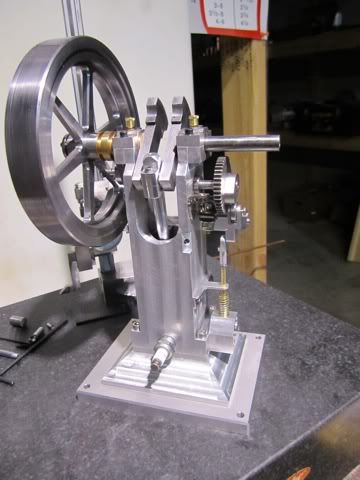
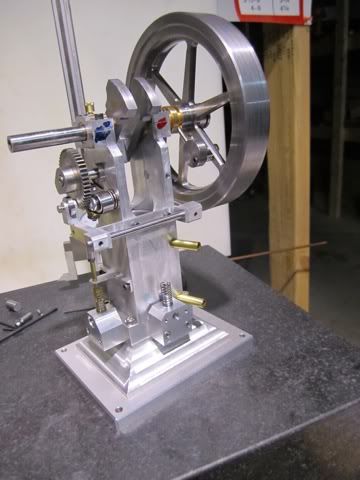