- Joined
- Oct 29, 2011
- Messages
- 284
- Reaction score
- 2
I finally got some time to finish off the main bearings. First job was to clamp the soleplate to an angle plate, taking care to get it aligned, and ensure that the bearings were screwed in tight.
Then onto the mill, lined up and drilled in increments:
I stoned the drills to reduce the tendency to grab in gunmetal, which mostly worked. I was careful to drill slowly, and keep pressure on the quill feed to avoid the drill getting pulled in too fast.
After drilling to 1/64" undersize, I switch to the reamer.
This is a right-hand rotation, left-hand spiral reamer. It's a hand reamer, which means it has a taper. [Please note warning in later reply about using hand reamers in the mill.] Because of that I can't go through both bearings from the same side, so I went as deep as I could from one side, flipped over the entire setup (one of the G-clamps had to be moved, but the other kept the soleplate aligned), and relocated on the hole:
I then reamed from that side, and cleaned up the edges with a light touch of the countersink. Now for the acid test: did I mess up the alignment?
Phew, things seem to line up!
Now the crankshaft still doesn't fit because of the radii:
Oddly the plans show zero clearance between the bearings and the crank throws, but I'd reduced the bearings a little to leave some room, and the radii keep the crankshaft from moving side-to-side. However, the bearings needed some relief to fit the radii, which I did by hand with a countersink and some wet & dry:
Then I did some initial settling in with some Brasso as abrasive, turning the crank by hand:
The final fit seems pretty good.
Then onto the mill, lined up and drilled in increments:
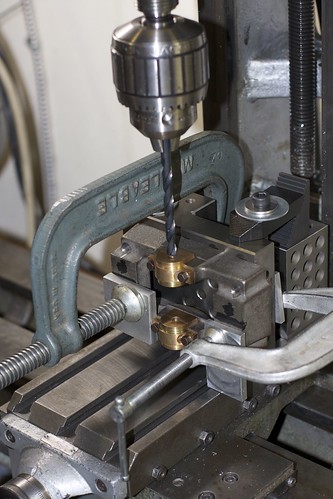
I stoned the drills to reduce the tendency to grab in gunmetal, which mostly worked. I was careful to drill slowly, and keep pressure on the quill feed to avoid the drill getting pulled in too fast.
After drilling to 1/64" undersize, I switch to the reamer.
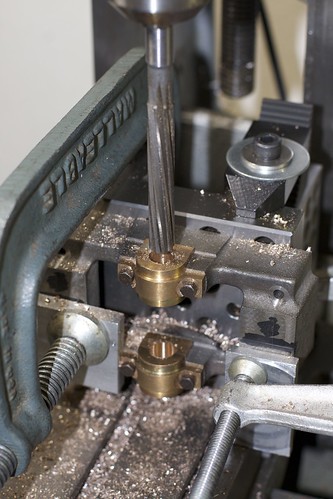
This is a right-hand rotation, left-hand spiral reamer. It's a hand reamer, which means it has a taper. [Please note warning in later reply about using hand reamers in the mill.] Because of that I can't go through both bearings from the same side, so I went as deep as I could from one side, flipped over the entire setup (one of the G-clamps had to be moved, but the other kept the soleplate aligned), and relocated on the hole:
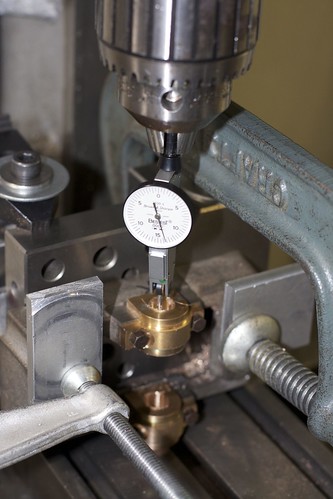
I then reamed from that side, and cleaned up the edges with a light touch of the countersink. Now for the acid test: did I mess up the alignment?
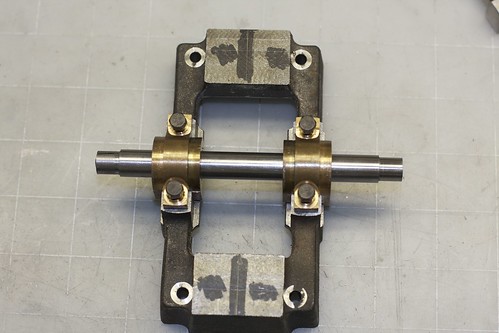
Phew, things seem to line up!
Now the crankshaft still doesn't fit because of the radii:
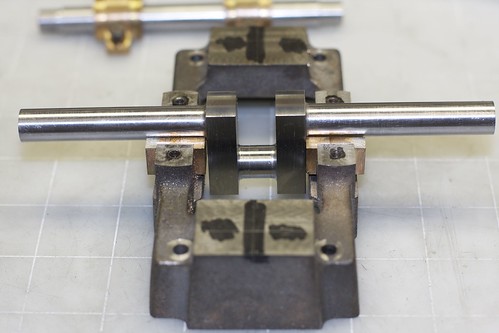
Oddly the plans show zero clearance between the bearings and the crank throws, but I'd reduced the bearings a little to leave some room, and the radii keep the crankshaft from moving side-to-side. However, the bearings needed some relief to fit the radii, which I did by hand with a countersink and some wet & dry:
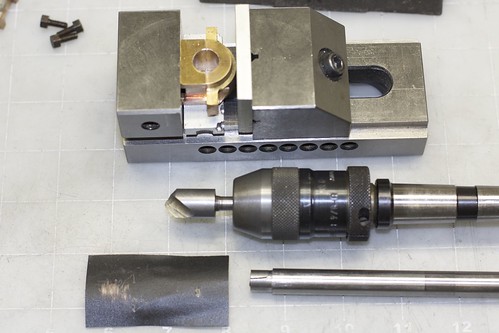
Then I did some initial settling in with some Brasso as abrasive, turning the crank by hand:
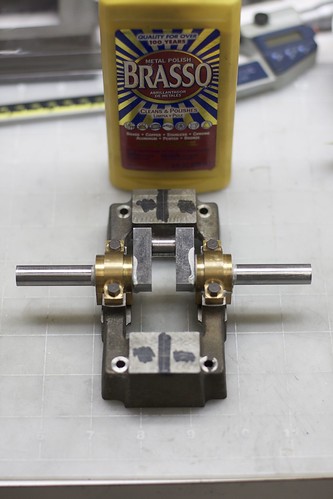
The final fit seems pretty good.