- Joined
- Oct 29, 2011
- Messages
- 284
- Reaction score
- 2
I plucked up the courage to thread the bottom cylinder cover for the piston rod gland today this evening. To hold the cover, I put the soft jaws onto the 3-jaw chuck, clamped the jaws down onto a bit of stuck, and cut a lip to fit the cylinder cover, then removed the stock and clamped down on the part. Here I'm checking with the dial indicator; runout was about a thou, which seemed reasonable.
Then I put a small bevel on the bore so that the tap would start concentrically:
I was concerned about tap alignment, so fiddled around for a bit with shims under the leading edge of tailstock, and the drill in the chuck that I'd use to drill the part earlier, and got the drill sliding nicely into the hole. Then it was replaced with the tap, and tapping started under hand power, with the taper tap:
With this size tap it wasn't long before the tap was starting to rotate in the chuck (despite backing out the tap often to clean the chips), so more desperate measures were called for! The steady rest made a handy way to keep the tap straight so I could apply more force with the tap wrench:
I switched to the bottoming tap, then back to the taper tap, then back to the bottoming tap, and by the end was using two wrenches to turn the thing (but carefully!), and finally was done.
Hey, I can make it finger-tight, and the piston rod still slides through
The threads in the cast iron look terrible, but I'm not sure how much of that is my fault. These are HSS taps from Tracy Tools in Devon, UK, but they don't seem to cut as nicely as the HQS taps I have from Tap & Die.
Simon
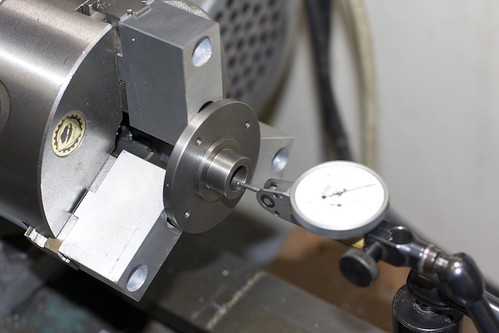
Then I put a small bevel on the bore so that the tap would start concentrically:
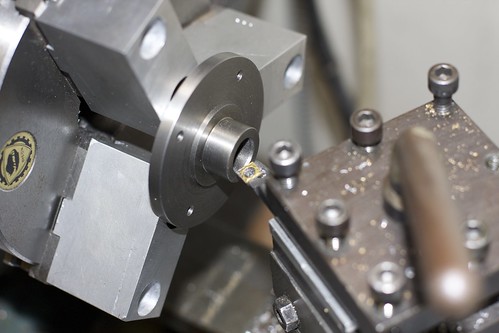
I was concerned about tap alignment, so fiddled around for a bit with shims under the leading edge of tailstock, and the drill in the chuck that I'd use to drill the part earlier, and got the drill sliding nicely into the hole. Then it was replaced with the tap, and tapping started under hand power, with the taper tap:
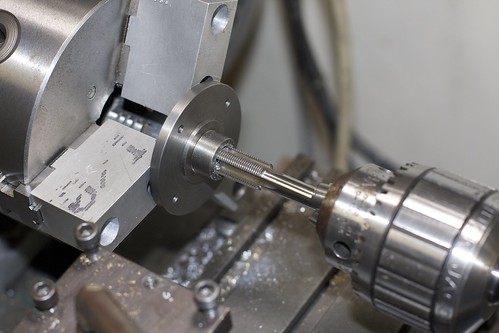
With this size tap it wasn't long before the tap was starting to rotate in the chuck (despite backing out the tap often to clean the chips), so more desperate measures were called for! The steady rest made a handy way to keep the tap straight so I could apply more force with the tap wrench:
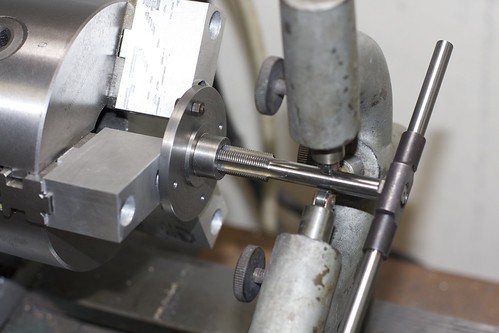
I switched to the bottoming tap, then back to the taper tap, then back to the bottoming tap, and by the end was using two wrenches to turn the thing (but carefully!), and finally was done.
Hey, I can make it finger-tight, and the piston rod still slides through

The threads in the cast iron look terrible, but I'm not sure how much of that is my fault. These are HSS taps from Tracy Tools in Devon, UK, but they don't seem to cut as nicely as the HQS taps I have from Tap & Die.
Simon