BobWarfield
Well-Known Member
- Joined
- Dec 27, 2007
- Messages
- 1,151
- Reaction score
- 1
Rounding over involves using a pin so you can rotate a workpiece close to a milling cutter to round over one end. As part of my Team Build for a little Elmer Verburg steam engine, I had to round over a bunch of connecting rods on the small end. Here is the fixture I hit on after looking over the bits and pieces in my shop:
Take an unused drill chuck, a v-block, your mill vise, and an upside down twist drill of appropriate pin size. The chuck holds the pin very nicely and at a convenient height for my Kurt vise. I centered the pin on the end mill along the X axis, and positioned Y so I am a little ways back from cutting. It pays to keep up with this initial position on your mill dials!
I'm going to use that little bit of aluminum soda can to make sure I don't damage my con rods holding them with the vise grips....
We just clamp the big end using the soda can as protection from the vise grip's serrated jaws...
<continued>
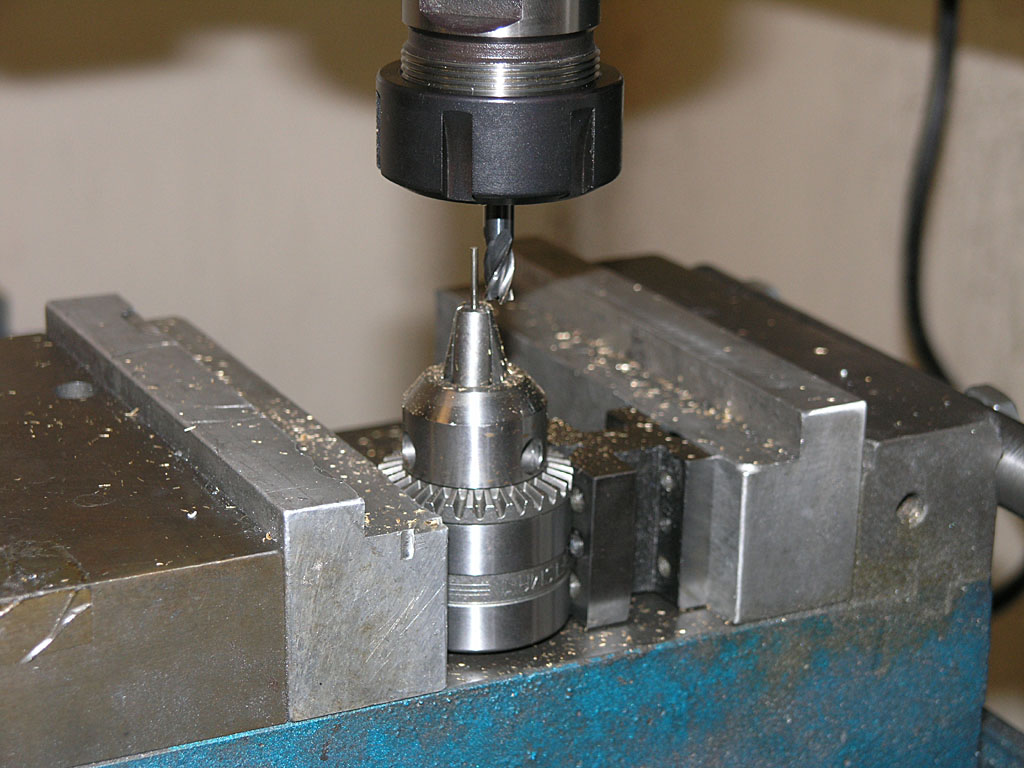
Take an unused drill chuck, a v-block, your mill vise, and an upside down twist drill of appropriate pin size. The chuck holds the pin very nicely and at a convenient height for my Kurt vise. I centered the pin on the end mill along the X axis, and positioned Y so I am a little ways back from cutting. It pays to keep up with this initial position on your mill dials!
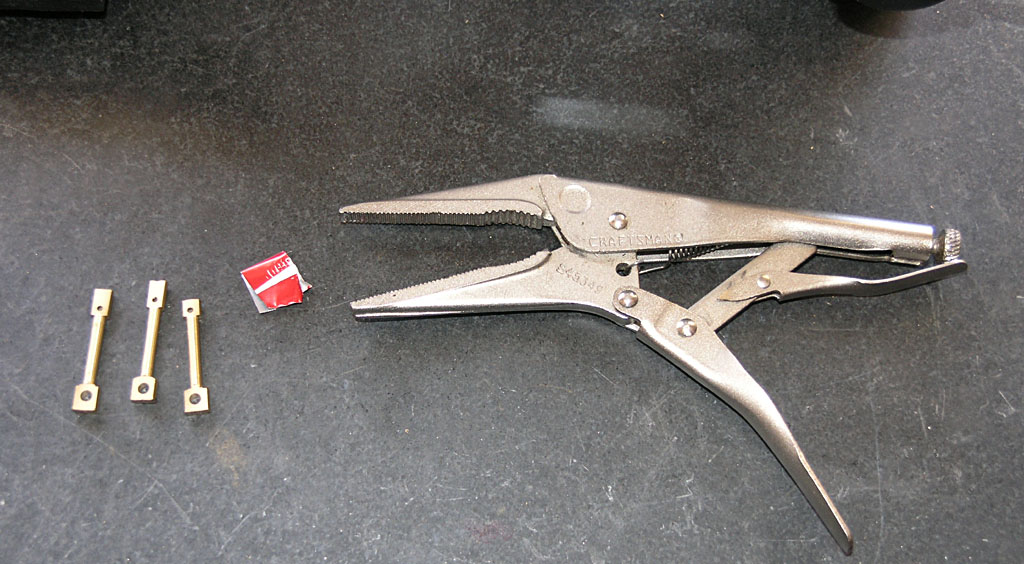
I'm going to use that little bit of aluminum soda can to make sure I don't damage my con rods holding them with the vise grips....
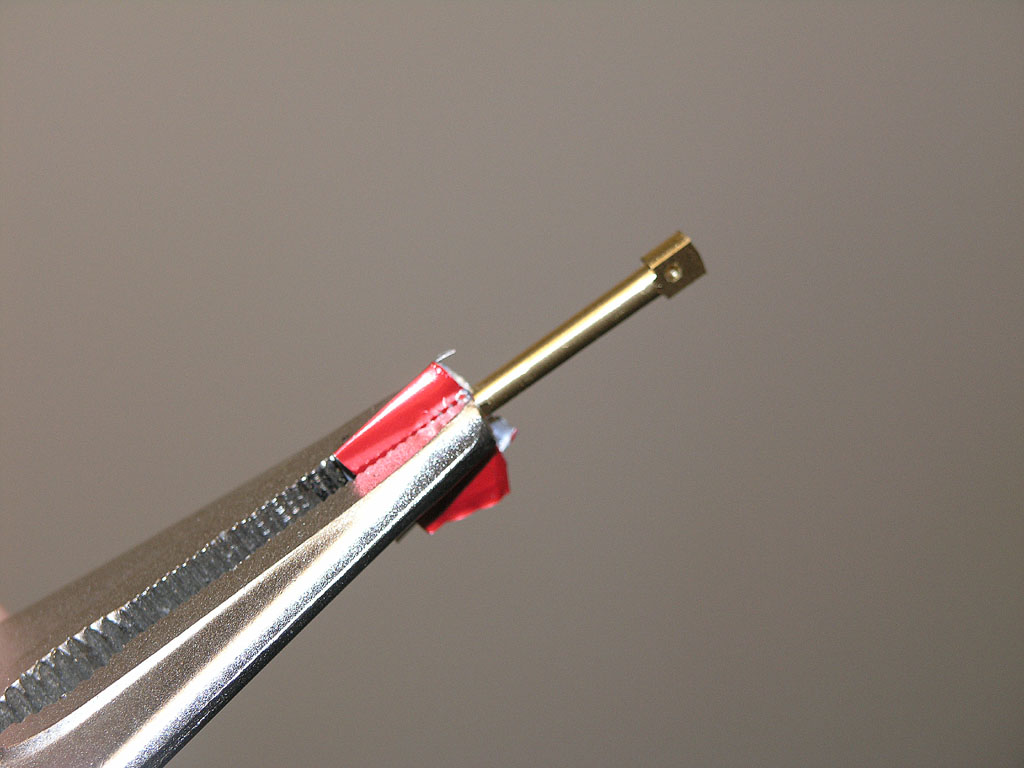
We just clamp the big end using the soda can as protection from the vise grip's serrated jaws...
<continued>