DavesWimshurst
DavesWimshurst
- Joined
- Dec 7, 2008
- Messages
- 102
- Reaction score
- 3
Carl,
Another thing that can help on small shafts is a half center which can be made from a dead center by grinding part of it away:
It gives more room for the tool but of course must be carefully adjusted and lubricated like any other dead center used in the tailstock.
Dave
Another thing that can help on small shafts is a half center which can be made from a dead center by grinding part of it away:
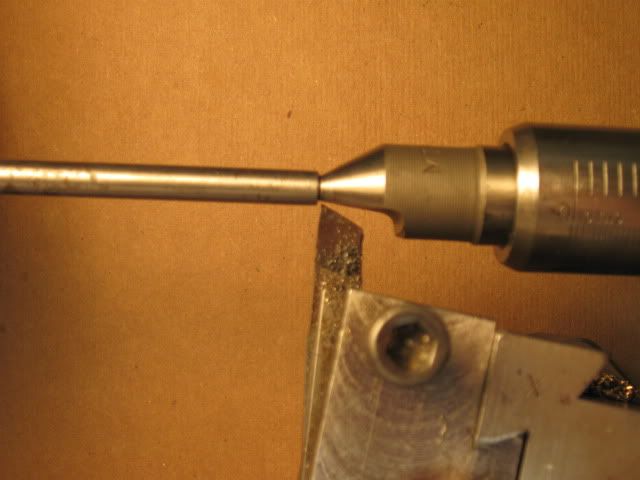
It gives more room for the tool but of course must be carefully adjusted and lubricated like any other dead center used in the tailstock.
Dave