- Joined
- Dec 28, 2008
- Messages
- 1,731
- Reaction score
- 9
20) I decided to have a go at making the piston rings. I bored the ID and turned the OD on a cast iron bar (Sorry no pictures, I either forgot to take them or deleted them by accident) and used a parting tool to cut off the rings. A dial indicator and travel rod arrangement was used to get each one the same width. I needed 10 rings for the project, but only enough material to cut 16 rings. I would have liked more as a safety net since cutting then them of was quick and easy. I followed Hamilton's plans that specify the ring blanks to be .003" larger than the bore. The 'X' is pointing to the first one that came off undersized in width by a few thousands.
21) I set the rings off to the side and turned my attention to making the pistons. Nothing out of the ordinary here, just your basic aluminum pistons.
22) To anneal the rings I made a fixture with a rod that would hold the rings open and gaped to the specified amount. The fixture along with the rings were placed in my heat treating furnace. The temperature was brought up to 1000-F and held for just over an hour. Treating them all together in a controlled furnace would assure that the rings would be all good, (or bad). :'(
23) Before the rings got a good baking, I clamped each ring in my scrap filing/sawing vice and cut the split's with an Ex-acto saw. This gave me the .010" cut specified in the plans.
24) Here the rings are all lined up in tight formation for their trip to a warmer place. The nuts hold them together were snugged up by hand, just in-case one of them were to object and get bent out of shape over the temperature increase! Rof}
25) My easy bake oven. When the temperature dropped down to about 450-F I pulled out the fixture and rings for further cooling. I immediately shut the door and went up stairs to grab a ham-n-cheese sandwich. After wraping it up in foil I pop'd it in the oven. No sense in wasting good heat, besides I was hungry! :big:
26) After the fixture cooled enough to handle with gloves, I removed the rings. They were sanded with #600 to width, and finished up with #1200 sand paper. They would not fit into the cylinder bores until I sanded the gaps out about .003". I pushed each one through its respective bore using the end of the piston, and double checked each gap and adjusted them till they measured .004 using a feeler gauge. After proper gaping they were installed on the pistons and pushed back and forth in the cylinder to make sure there was contact all the way around each ring. All the rings but one were making contact. After pushing it back and forth for quite a while the other ring became polish up (A) but the bad one made contact in just a few spots (rings on (B) show contact all around after being pushed through only twice) I pulled it off (A) and replaced it. The replacement ring showed contact all the way around after pushing it through a dozen times and checking. Problem solved! I took the offending ring (D) and spread it out till it finally bent and then broke in two! That'l teach ya ta mess with me! *knuppel2*
27) This close up (A) shows the top ring in full contact and smooth, and the lower replacement in full contact but still mostly discolored on the working surface. After a few strokes through the bore (B) is showing contact all the way around, as are the three other pistons/rings shown in their respective cylinders. (C) shows the rings left over due to zero breakage. Am I lucky or what!
It turns out that making piston rings is not difficult at all. Since this was my first attempt, I made mistakes along the way, and I learned a lot. Next time they will turn out much better and with a little less fuss. Thm:
-MB
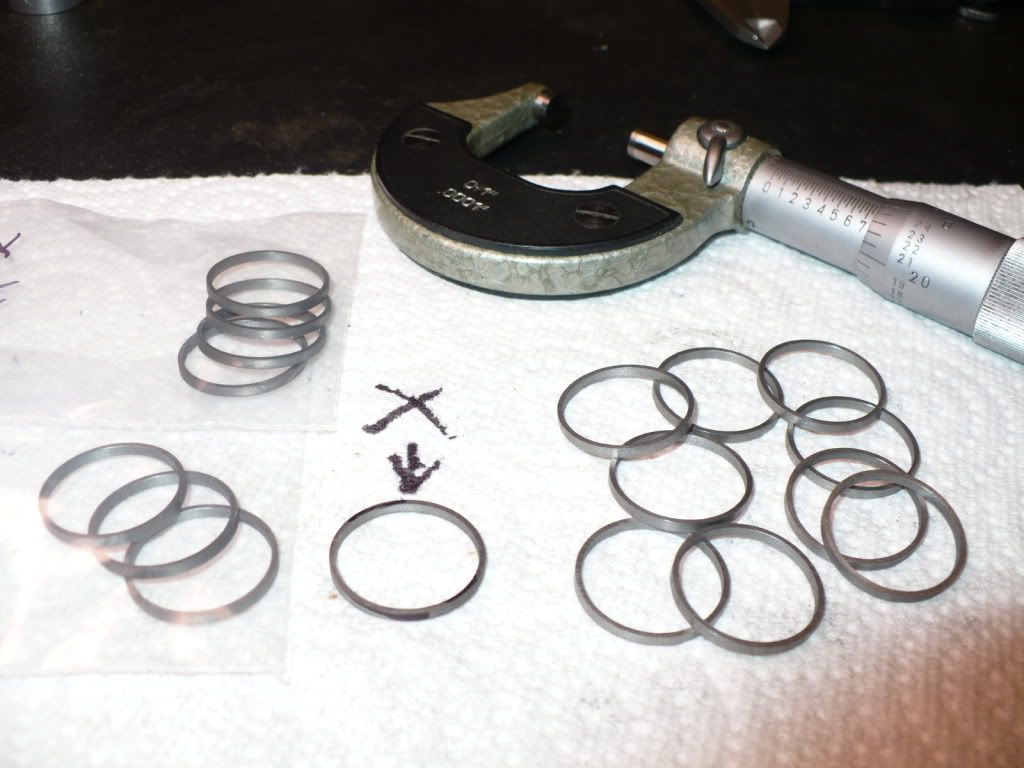
21) I set the rings off to the side and turned my attention to making the pistons. Nothing out of the ordinary here, just your basic aluminum pistons.
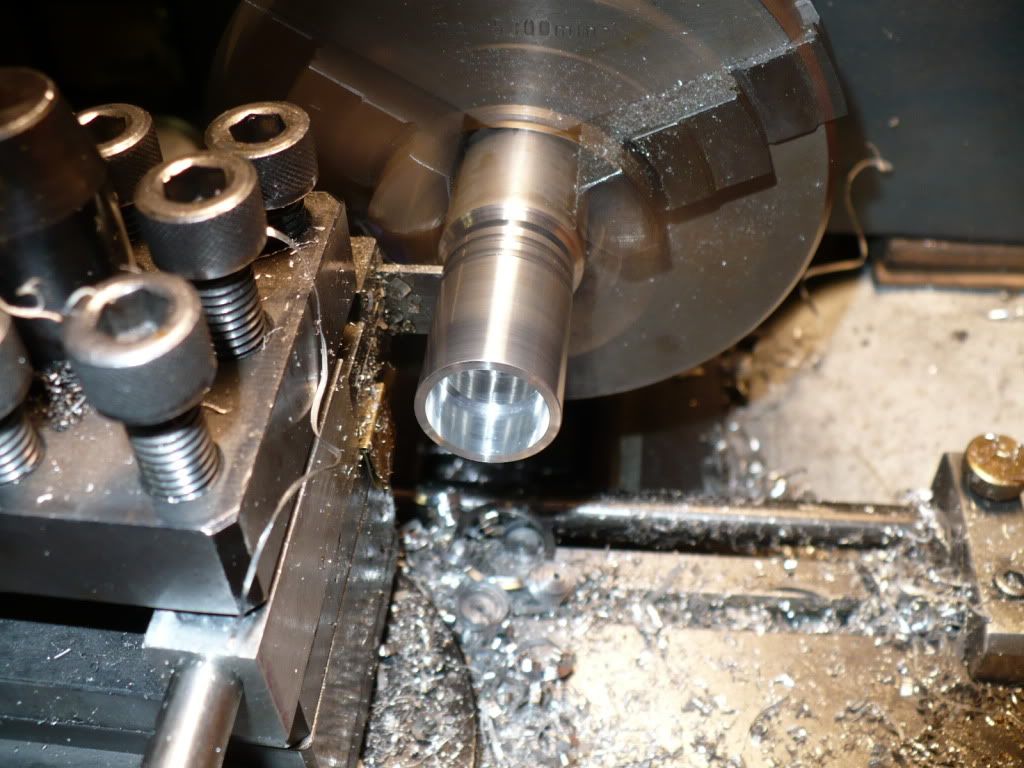
22) To anneal the rings I made a fixture with a rod that would hold the rings open and gaped to the specified amount. The fixture along with the rings were placed in my heat treating furnace. The temperature was brought up to 1000-F and held for just over an hour. Treating them all together in a controlled furnace would assure that the rings would be all good, (or bad). :'(
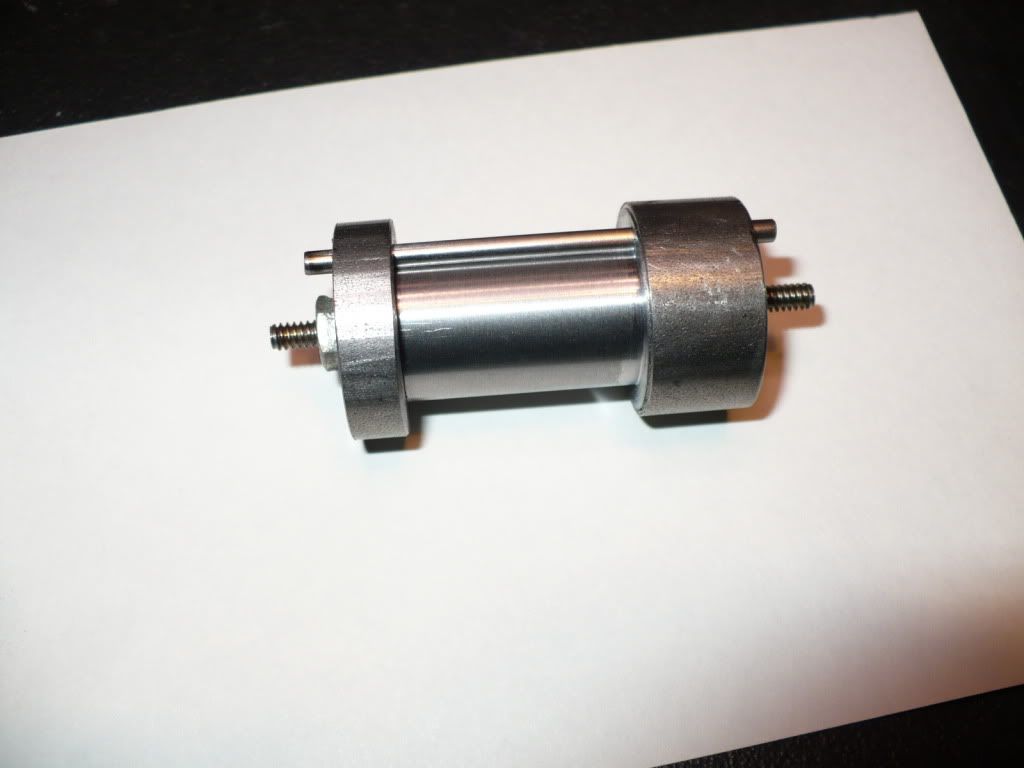
23) Before the rings got a good baking, I clamped each ring in my scrap filing/sawing vice and cut the split's with an Ex-acto saw. This gave me the .010" cut specified in the plans.
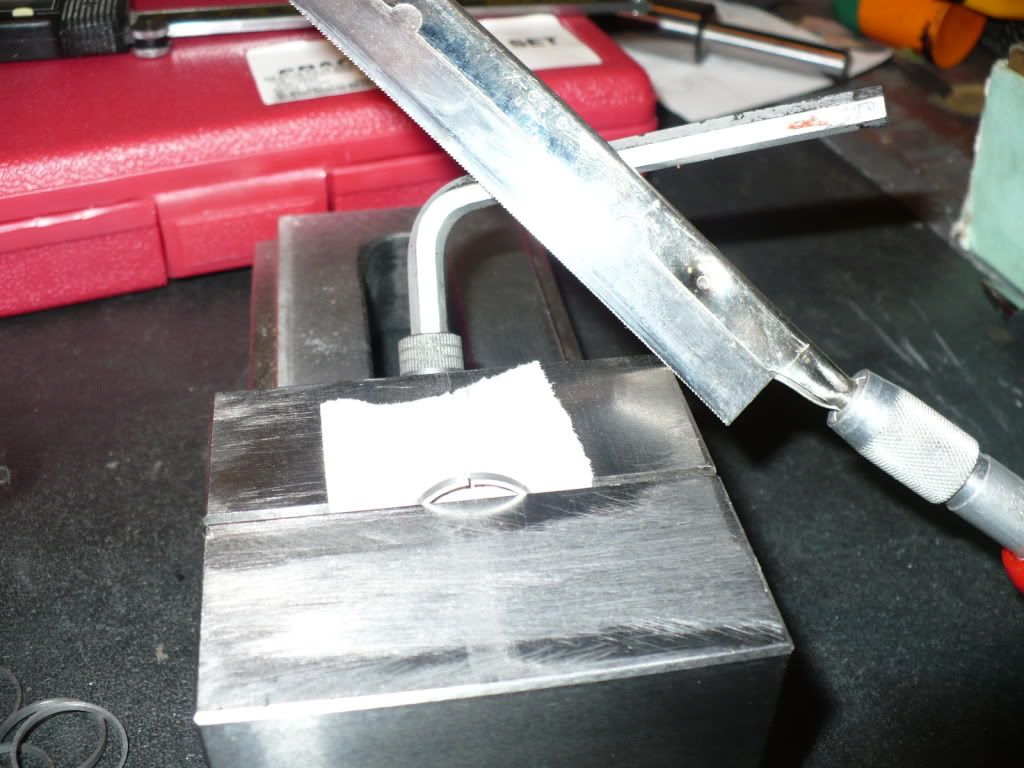
24) Here the rings are all lined up in tight formation for their trip to a warmer place. The nuts hold them together were snugged up by hand, just in-case one of them were to object and get bent out of shape over the temperature increase! Rof}
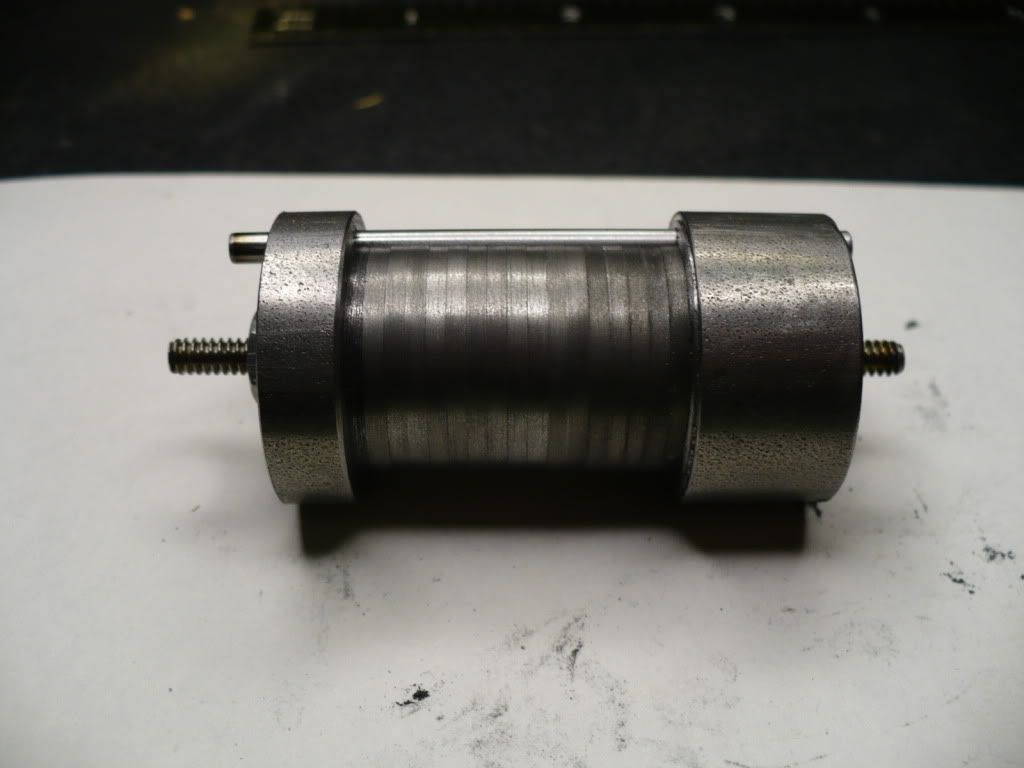
25) My easy bake oven. When the temperature dropped down to about 450-F I pulled out the fixture and rings for further cooling. I immediately shut the door and went up stairs to grab a ham-n-cheese sandwich. After wraping it up in foil I pop'd it in the oven. No sense in wasting good heat, besides I was hungry! :big:
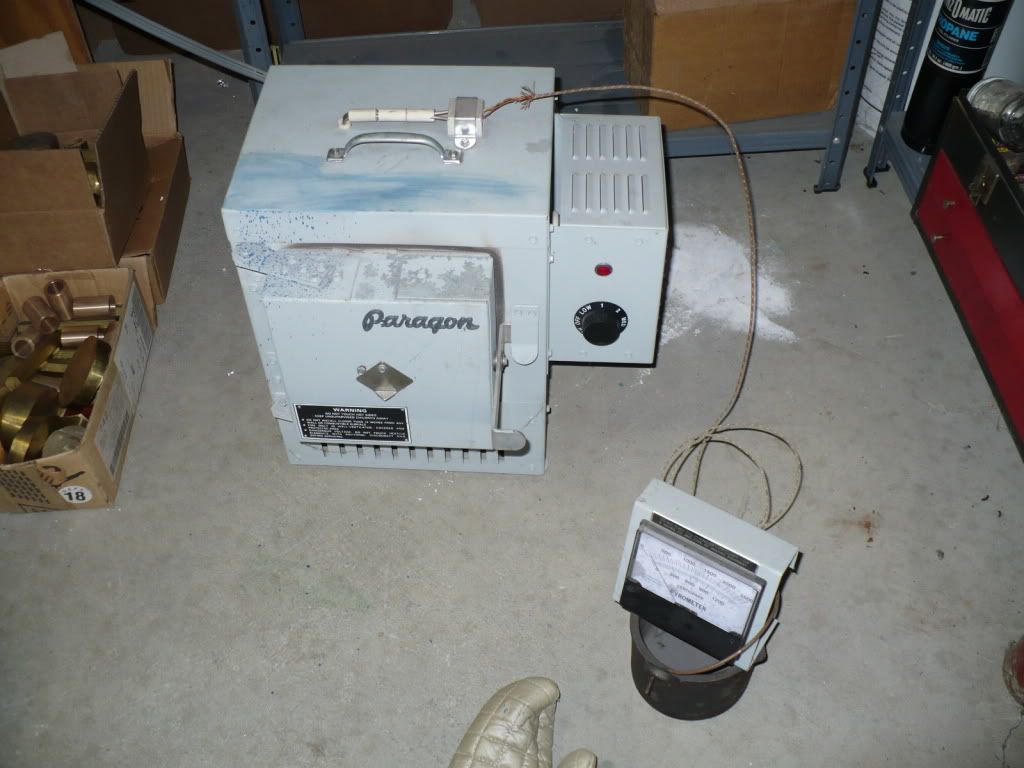
26) After the fixture cooled enough to handle with gloves, I removed the rings. They were sanded with #600 to width, and finished up with #1200 sand paper. They would not fit into the cylinder bores until I sanded the gaps out about .003". I pushed each one through its respective bore using the end of the piston, and double checked each gap and adjusted them till they measured .004 using a feeler gauge. After proper gaping they were installed on the pistons and pushed back and forth in the cylinder to make sure there was contact all the way around each ring. All the rings but one were making contact. After pushing it back and forth for quite a while the other ring became polish up (A) but the bad one made contact in just a few spots (rings on (B) show contact all around after being pushed through only twice) I pulled it off (A) and replaced it. The replacement ring showed contact all the way around after pushing it through a dozen times and checking. Problem solved! I took the offending ring (D) and spread it out till it finally bent and then broke in two! That'l teach ya ta mess with me! *knuppel2*
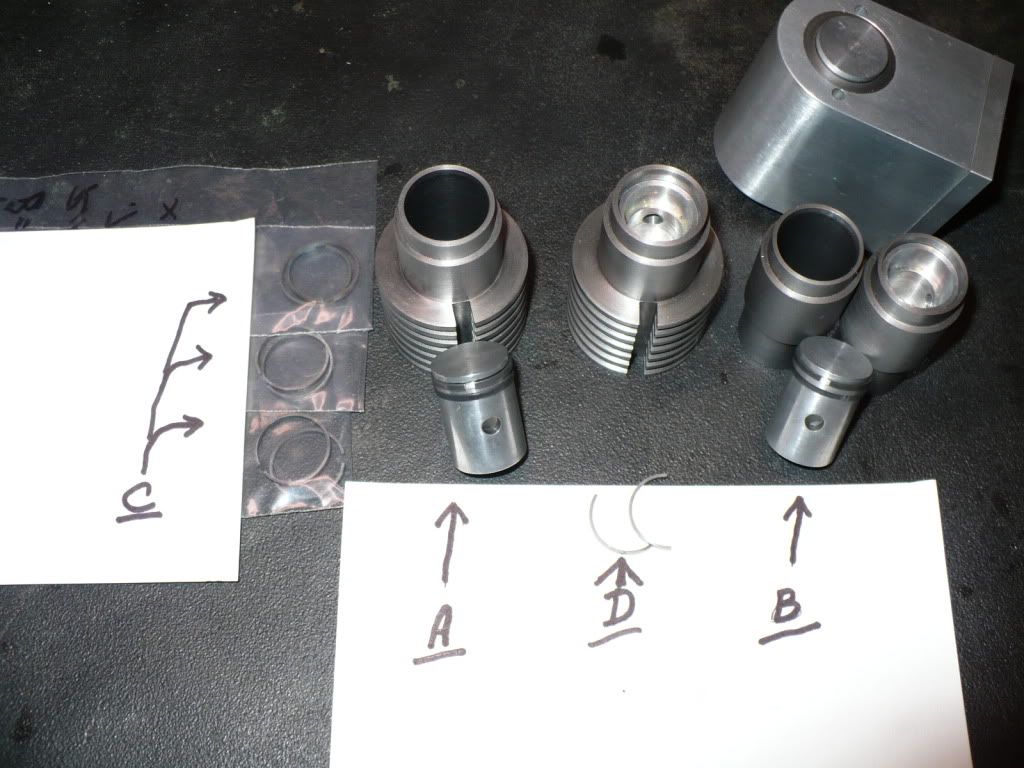
27) This close up (A) shows the top ring in full contact and smooth, and the lower replacement in full contact but still mostly discolored on the working surface. After a few strokes through the bore (B) is showing contact all the way around, as are the three other pistons/rings shown in their respective cylinders. (C) shows the rings left over due to zero breakage. Am I lucky or what!
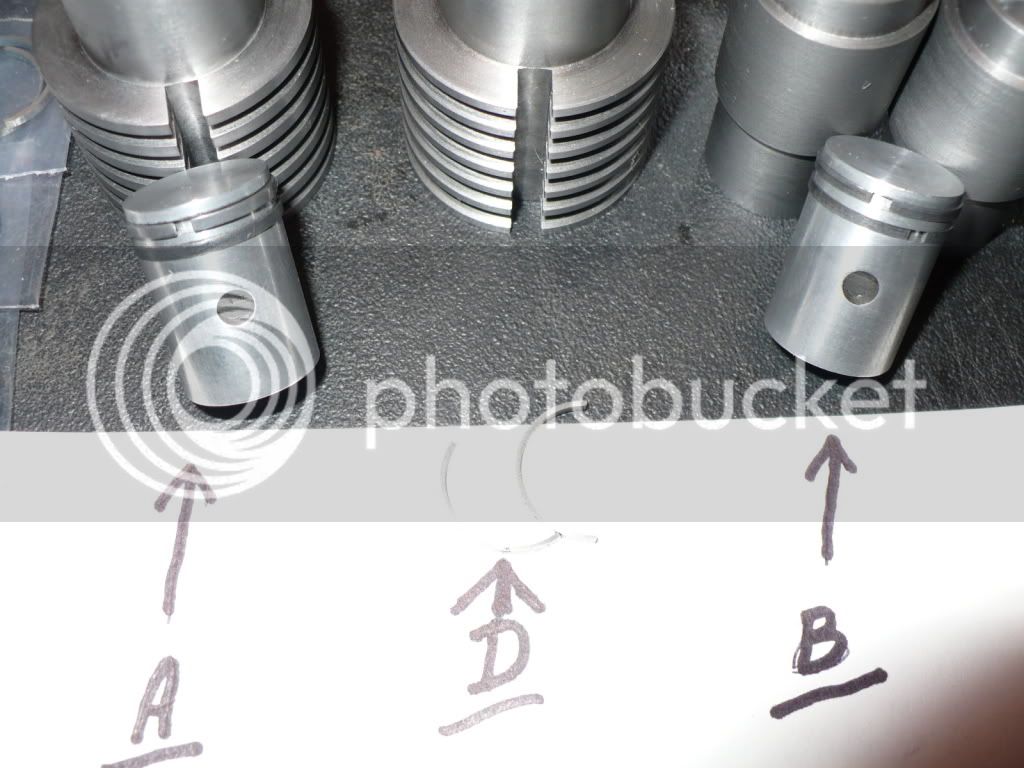
It turns out that making piston rings is not difficult at all. Since this was my first attempt, I made mistakes along the way, and I learned a lot. Next time they will turn out much better and with a little less fuss. Thm:
-MB