- Joined
- Dec 28, 2008
- Messages
- 1,731
- Reaction score
- 9
#325 For today's post I'll show how the pig tails with Futaba connectors are attached to the hall sensors, and mounted into the adjustable sensor carrier with epoxy.
I shortened the prongs on the Hall Sensors by cutting them down to 3/8". This will place the solder joints out side of the carrier allowing for a full support of the prongs inside the added block. The added solder on block was channeled out with an end mill in a previous post.
#326 I made a small aluminum combination heat sink and support fixture to minimize the danger of over-heating the sensor, and to hold it steady during the process of soldering on the wires. The hold down bar is .110" x .110" held down with 2x 0-80 cap screws.
#327 I had to criss-cross the red and black wires to make the proper connections on the hall sensor. I ordered and used 22 ga. wires with the connectors already attached. The wires turned out to be too thick for the close proximity of the prongs on the sensor. It was necessary to solder the center wire on top, and to solder on the outside wires from underneath to have enough clearance. After the soldering was complete I slide two short pieces of shrink tube over the out side solder joints and shrunk them with a lighter. The center solder joint bare and will be protected by the insulation on both side wires.
#328 To finish up the assembly a larger and longer piece of shrink tube was slid into place and shrunk to complete the assembly. The shrink tubing should be on the wires prior to soldering. I learned this the hard way on the first one and had to un-solder the connections to get it in place and ready on the wires.
#329 I had previously made up an extra carrier for the sensor, and I also made up an extra sensor assembly in case a sensor fails. This will make the replacement quick and simple. In the picture below you can see one installed. I will need to cover the epoxy and prongs that are showing through with some thin brass shim stock, or some brass colored paint.
#330 Here's how the assembly looks prior to adding the epoxy. The area around the prongs is wider and deeper than the area around the head of the sensor. This will all be filled with epoxy to encapsulate the prongs and prevent any bending that could lead to sensor failure.
#331 This last picture shows the second hall sensor assembly set in epoxy. I temporarily wired the ignition system to test the sensors and all 6 are firing a plug beautifully! I decided to stop at this point and take a break by posting my progress.
Fire in the hole! Rof} Rof}
-MB
I shortened the prongs on the Hall Sensors by cutting them down to 3/8". This will place the solder joints out side of the carrier allowing for a full support of the prongs inside the added block. The added solder on block was channeled out with an end mill in a previous post.
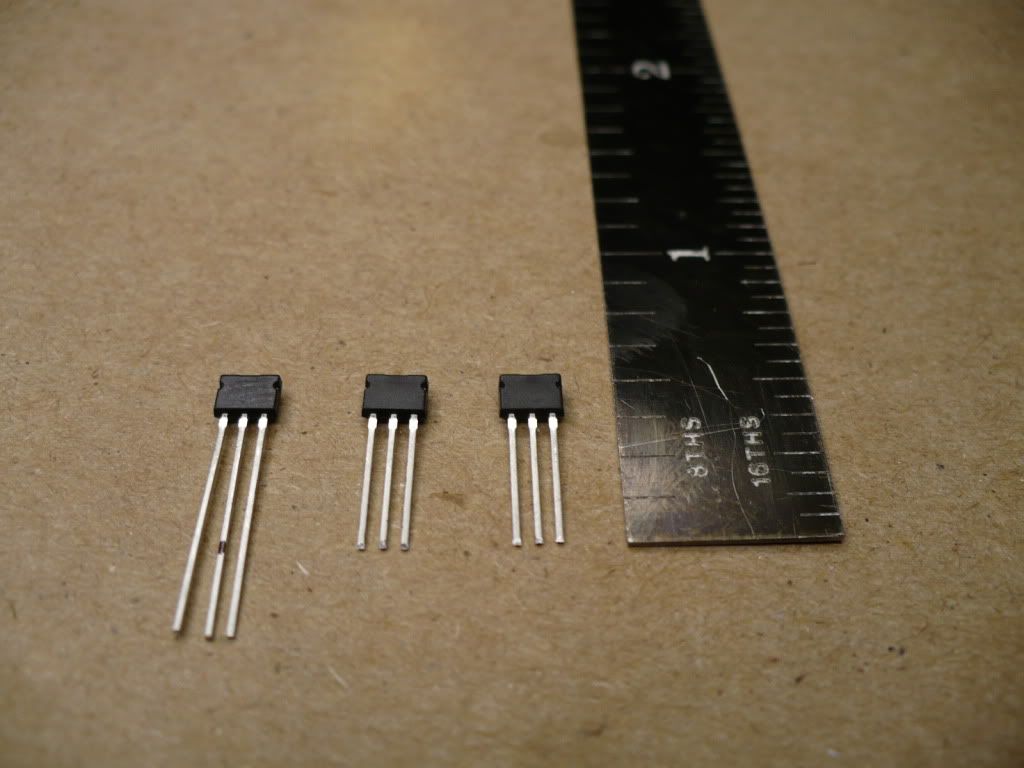
#326 I made a small aluminum combination heat sink and support fixture to minimize the danger of over-heating the sensor, and to hold it steady during the process of soldering on the wires. The hold down bar is .110" x .110" held down with 2x 0-80 cap screws.
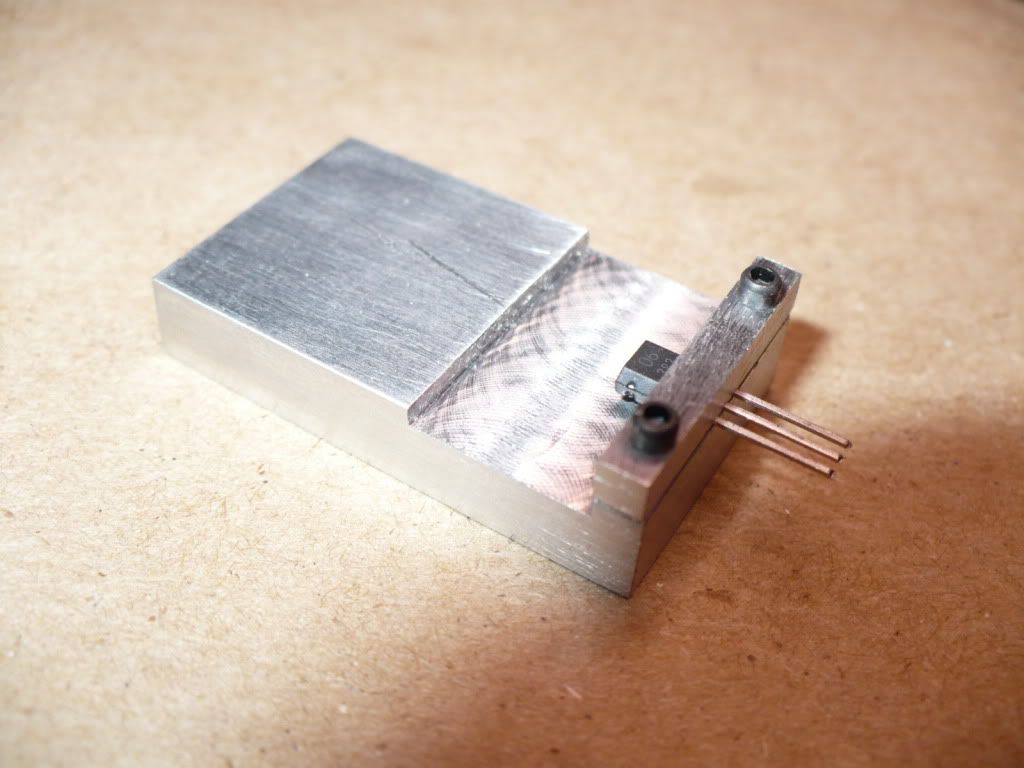
#327 I had to criss-cross the red and black wires to make the proper connections on the hall sensor. I ordered and used 22 ga. wires with the connectors already attached. The wires turned out to be too thick for the close proximity of the prongs on the sensor. It was necessary to solder the center wire on top, and to solder on the outside wires from underneath to have enough clearance. After the soldering was complete I slide two short pieces of shrink tube over the out side solder joints and shrunk them with a lighter. The center solder joint bare and will be protected by the insulation on both side wires.
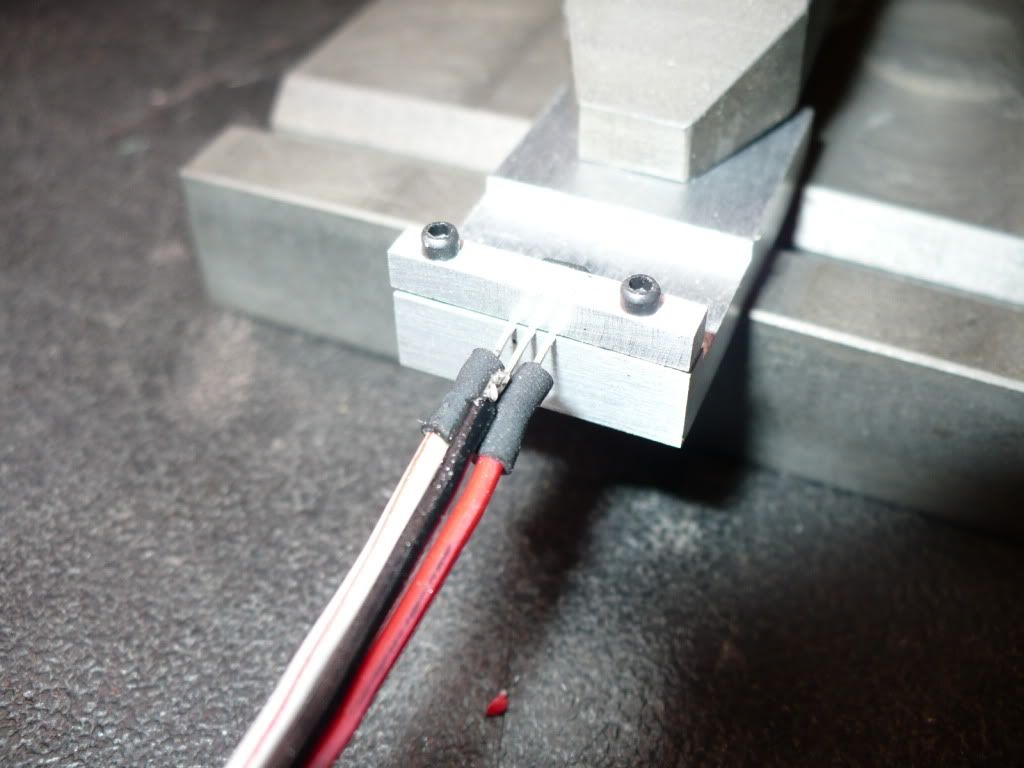
#328 To finish up the assembly a larger and longer piece of shrink tube was slid into place and shrunk to complete the assembly. The shrink tubing should be on the wires prior to soldering. I learned this the hard way on the first one and had to un-solder the connections to get it in place and ready on the wires.
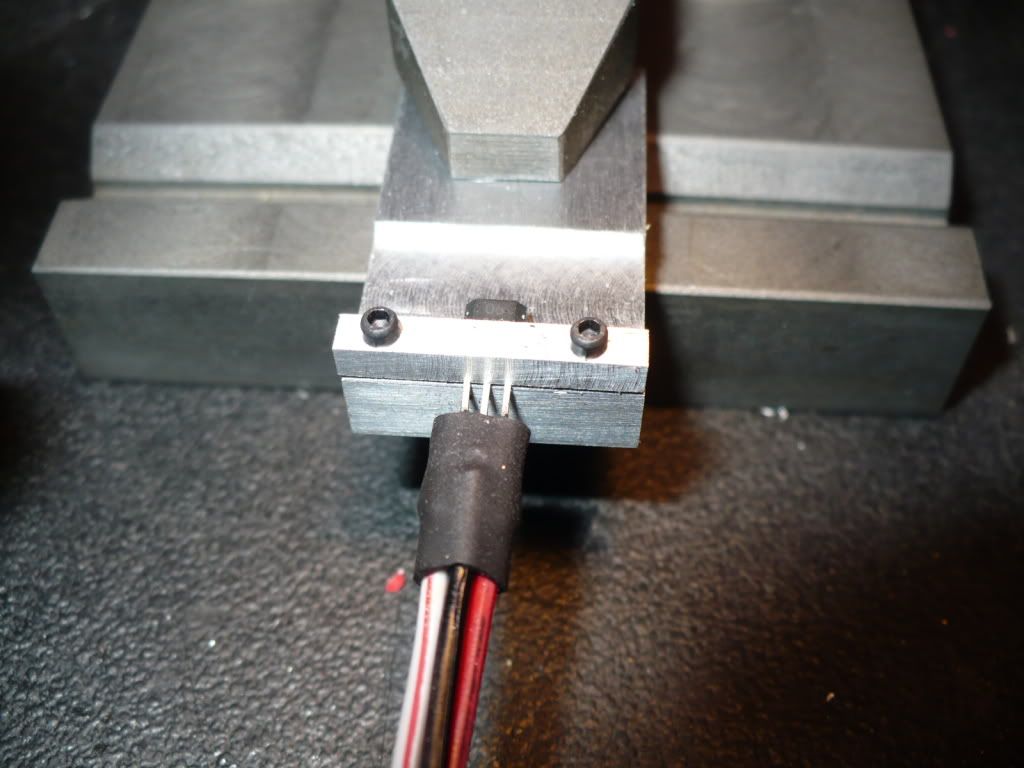
#329 I had previously made up an extra carrier for the sensor, and I also made up an extra sensor assembly in case a sensor fails. This will make the replacement quick and simple. In the picture below you can see one installed. I will need to cover the epoxy and prongs that are showing through with some thin brass shim stock, or some brass colored paint.
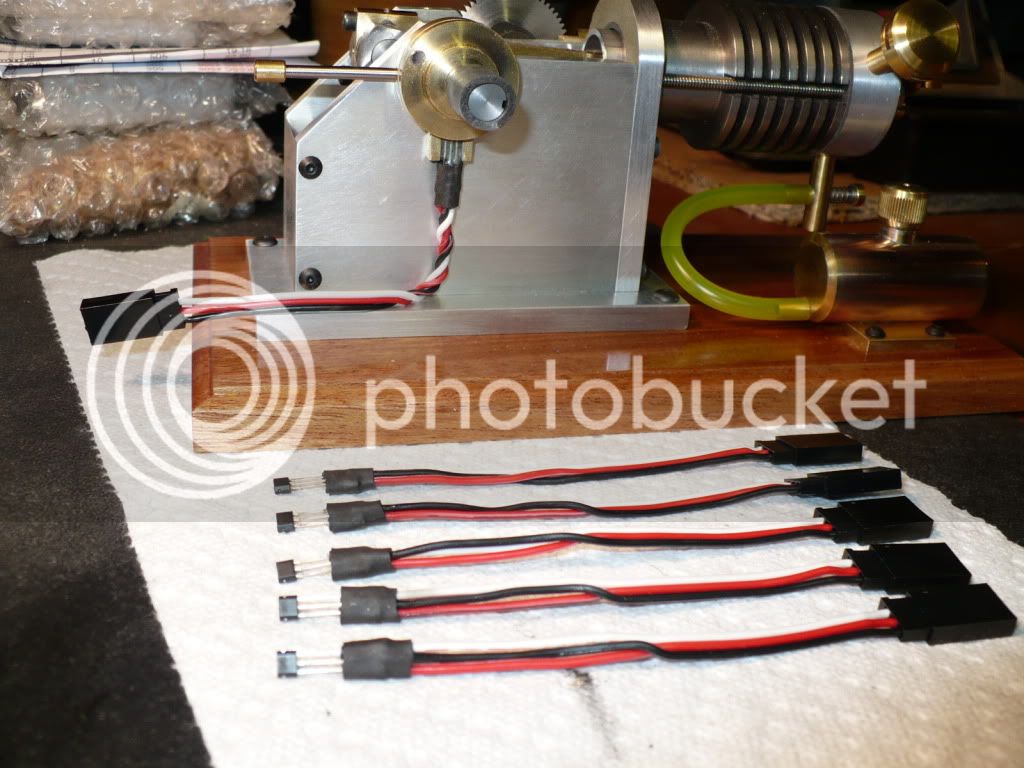
#330 Here's how the assembly looks prior to adding the epoxy. The area around the prongs is wider and deeper than the area around the head of the sensor. This will all be filled with epoxy to encapsulate the prongs and prevent any bending that could lead to sensor failure.

#331 This last picture shows the second hall sensor assembly set in epoxy. I temporarily wired the ignition system to test the sensors and all 6 are firing a plug beautifully! I decided to stop at this point and take a break by posting my progress.
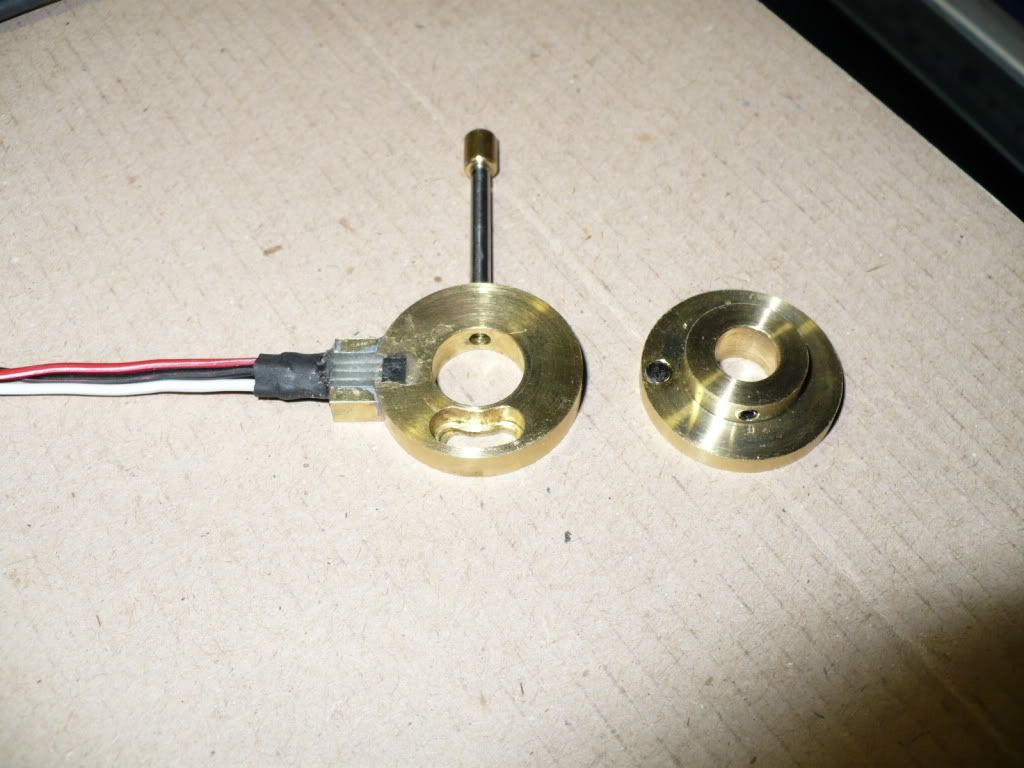
Fire in the hole! Rof} Rof}
-MB