Holt
Well-Known Member
- Joined
- Oct 14, 2010
- Messages
- 164
- Reaction score
- 4
The handle on the tailstock is mounted. I turned a bush from some of the stainless i got with the lathe, then i turned the hole in the handle to fit the bush.
I don't have a boring bar yet, so i use a long 8mm carbide mill i got from work. the normal carbide mills are send to regrind, but this one was a ball nose mill, they don't regrind those. I just grounded the ball nose away, and grounded a cutting edge at the end of one of the flutes, it works really well.
Bush mounted
Handle mounted on the spindle
I just happened to have an old 1/4 UNC tap, the same size as the treated hole in the handle, so i drilled a hole in the bush, and cut treats in it.
Holt
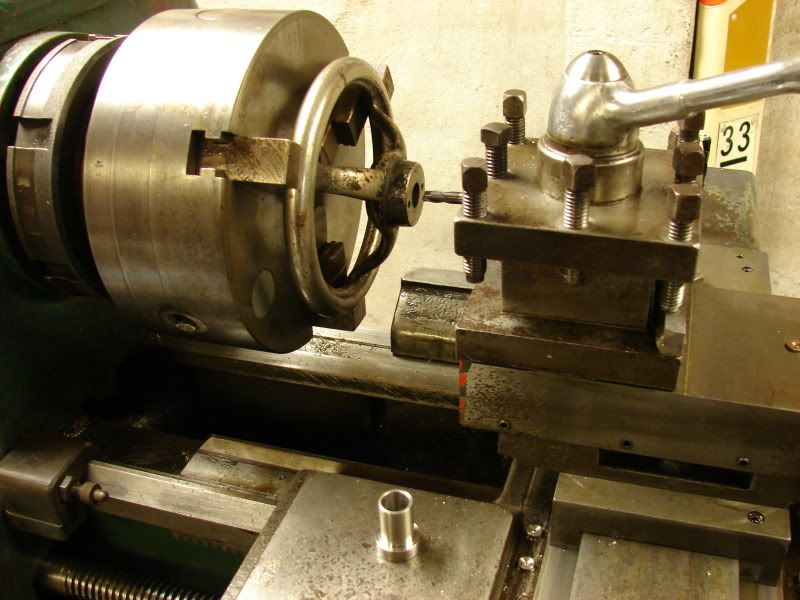
I don't have a boring bar yet, so i use a long 8mm carbide mill i got from work. the normal carbide mills are send to regrind, but this one was a ball nose mill, they don't regrind those. I just grounded the ball nose away, and grounded a cutting edge at the end of one of the flutes, it works really well.
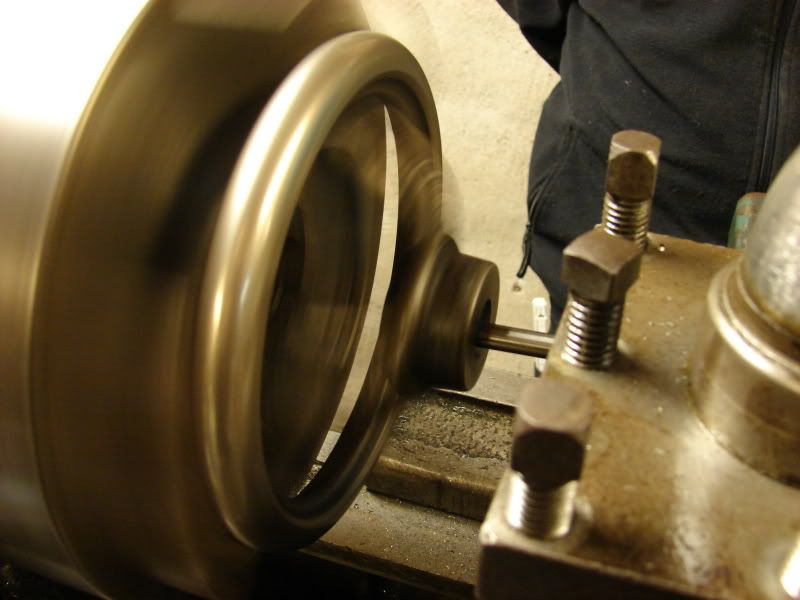
Bush mounted
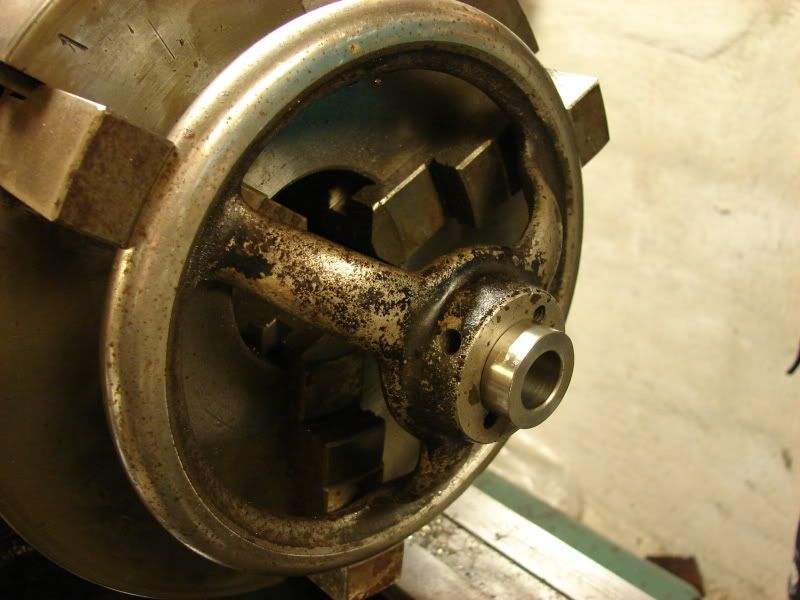
Handle mounted on the spindle
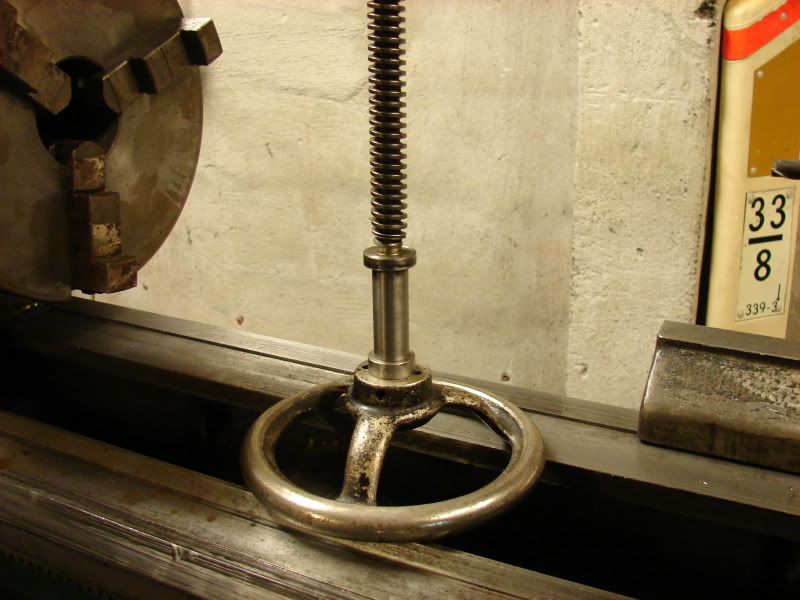
I just happened to have an old 1/4 UNC tap, the same size as the treated hole in the handle, so i drilled a hole in the bush, and cut treats in it.
Holt