This morning I lapped the brass cylinders. I have brass expanding laps, but didn't want to risk brass on brass. The cylinders were originally reamed to 0.500" with a machine reamer. A piece of cold rolled steel 1/2" shafting is always about .0005 to .001" undersize, which makes it unsuitable for a lap. 01 Steel however, comes in exactly on size, at a full 0.500" diameter, and will not pass freely thru the hole in the cylinder---but very close. So--I chuck up a piece of 1/2" diameter 01 steel, coat the end of it with 600 grit lapping paste, and with the lathe running on it's lowest speed, I SLOWLY AND CAREFULLY work the brass cylinder onto the lap. Not all in one go.--Maybe an eighth of an inch, then back off, then maybe a 1/4" and then back off and keep at it in 1/8" increments until the lap passes all the way thru the cylinder. Generally it sticks solid at some point and requires a trip out to my arbor press to press the stuck 01 steel out of the cylinder. You have to be damned sure that when it begins to seize that you can let go cleanly and not wrap yourself up in the lathe. After the lap passes completely thru the cylinder, work it back and forth slowly about 20 times, and you are finished.
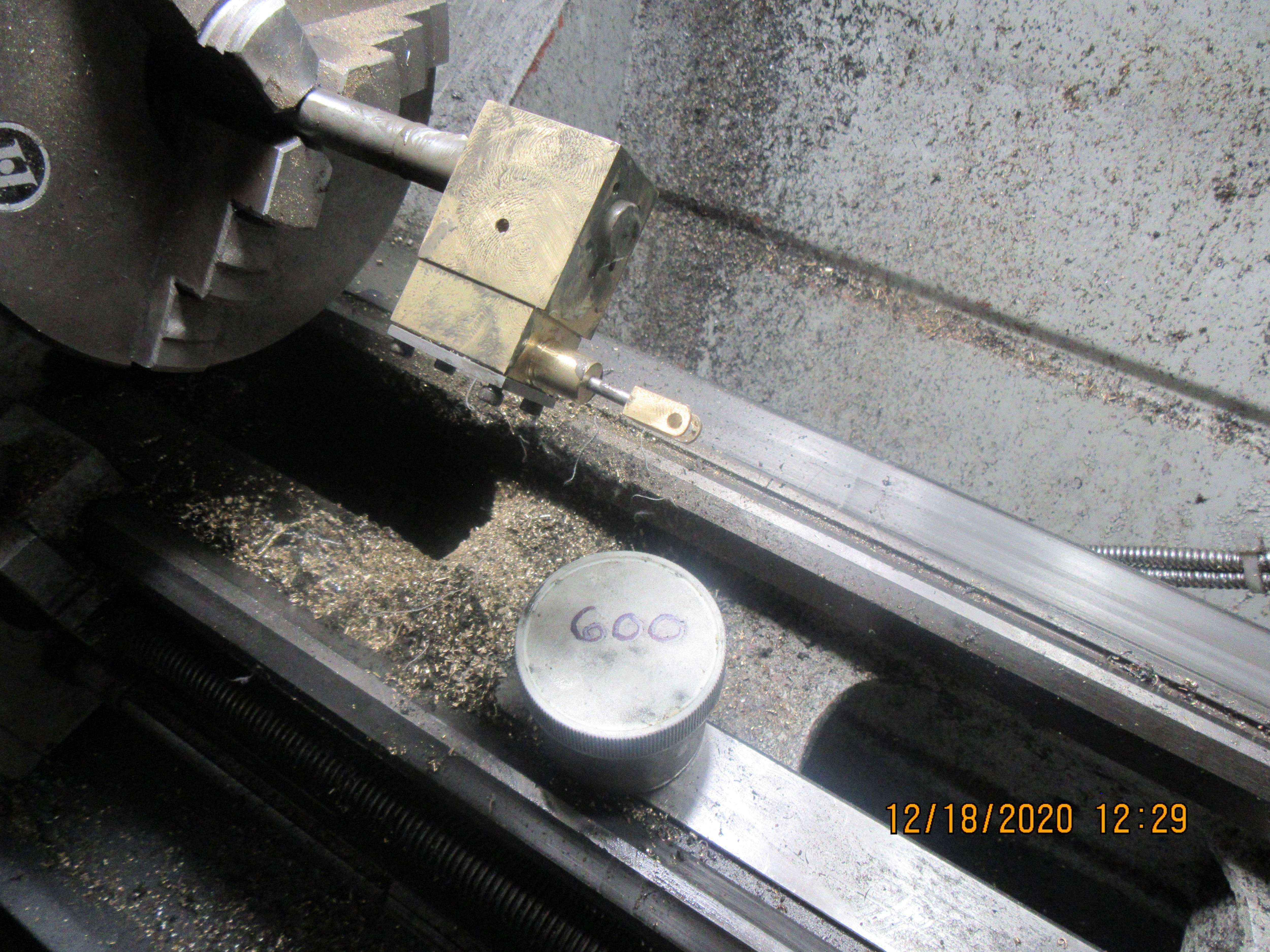
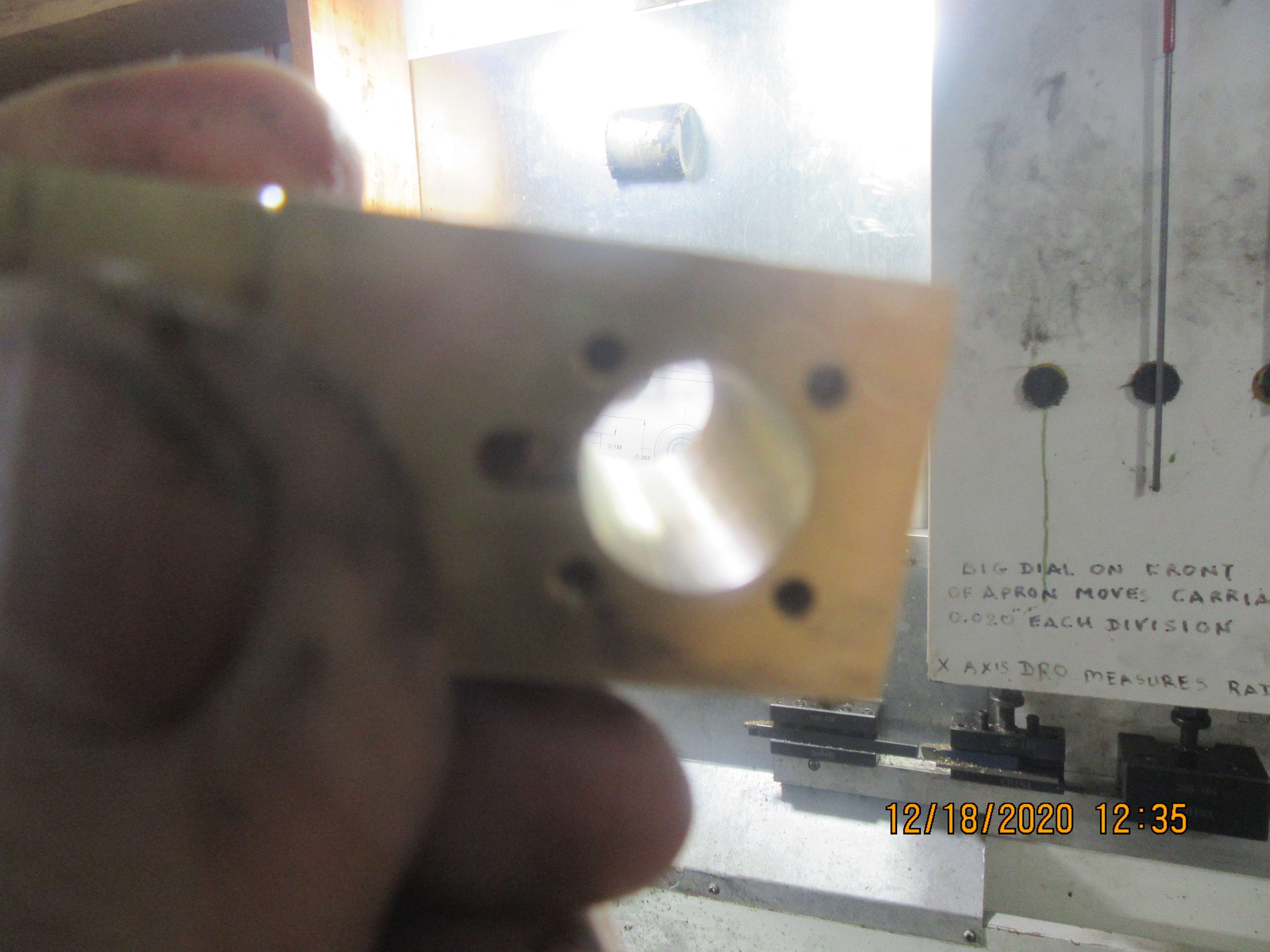
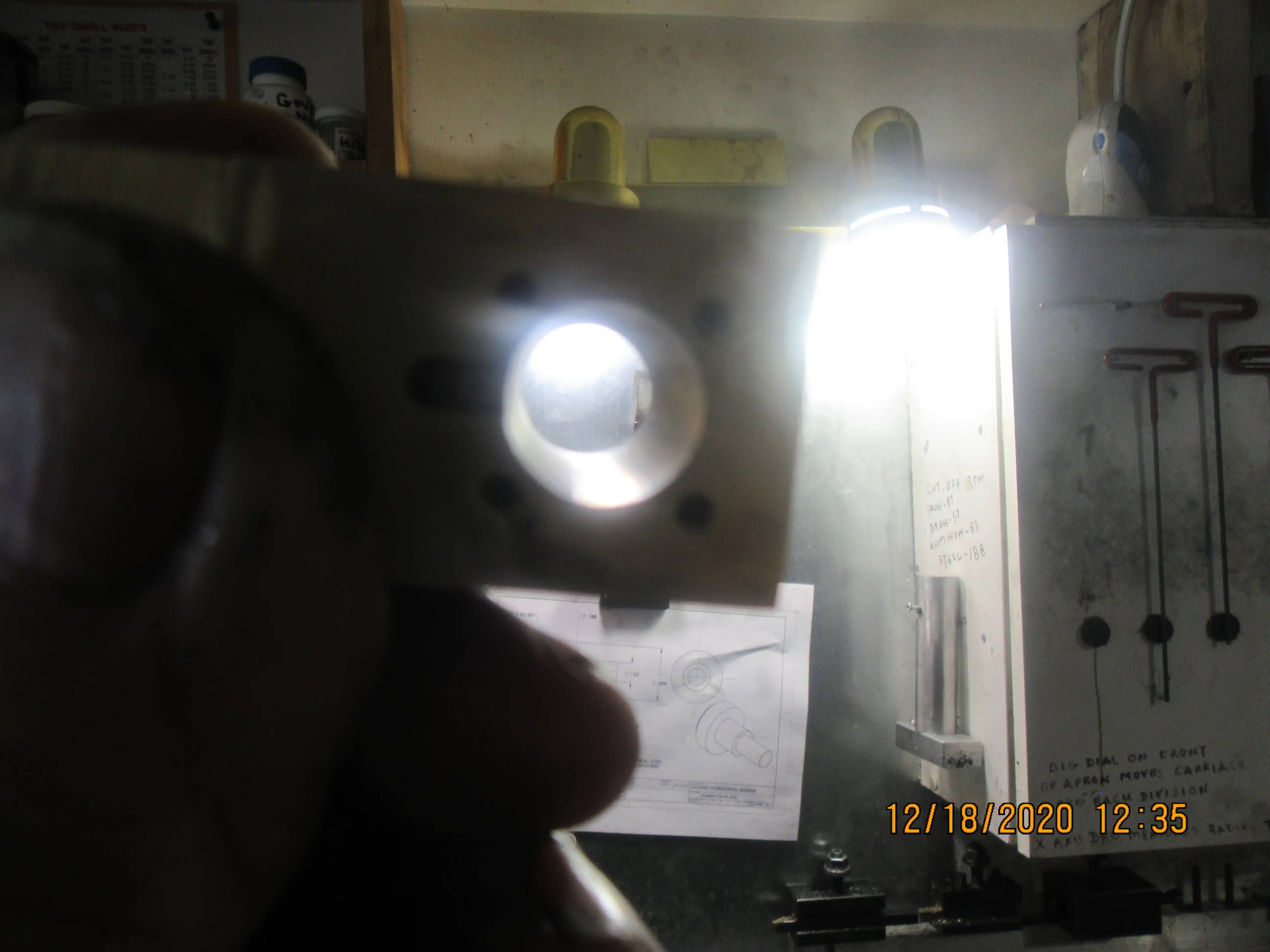