Hi at this moment I'm making my third small engine and Ive been folowing all the builds here with intrest and looking at the fantastic finish you chaps achieve i am trying to 'up my game' with regard to finish etc.
Here is where I'm up to
I've read books and posts on tools and tool sharpening but can't find any thing on
fly cutters
I am using a 3/16 cutter and would appreciate some pointers as how it should be sharpend.
or direct me to a post.
Also Witch is the preferred way to cut (feed in or drag it across) ???
this is my result up til now
Lots of regard and thanks
steve
Here is where I'm up to
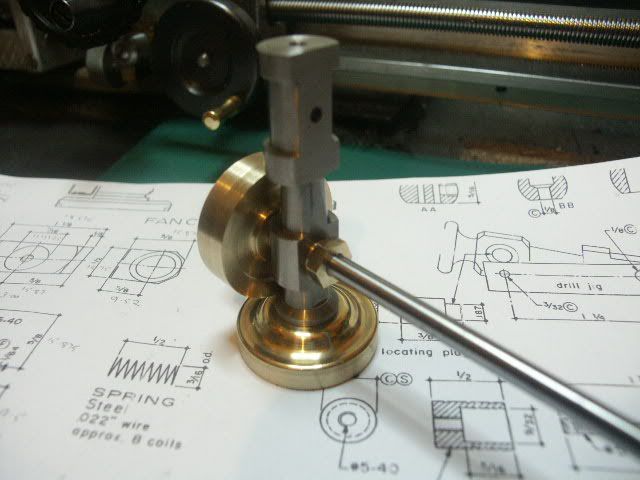
I've read books and posts on tools and tool sharpening but can't find any thing on
fly cutters
I am using a 3/16 cutter and would appreciate some pointers as how it should be sharpend.
or direct me to a post.
Also Witch is the preferred way to cut (feed in or drag it across) ???
this is my result up til now
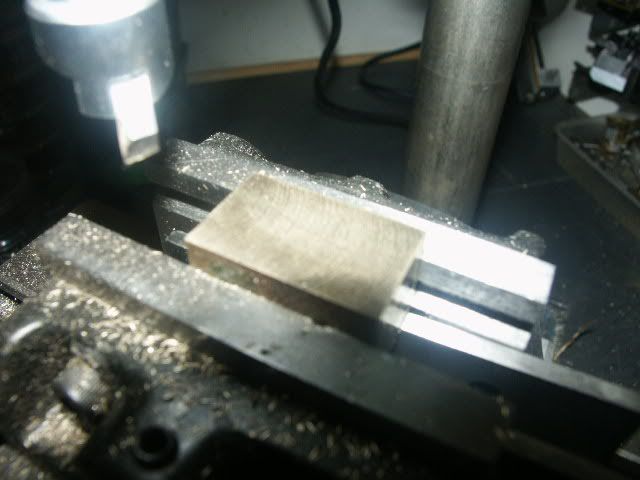
Lots of regard and thanks
steve