Today I machined the crankshaft extension for the Odds and Ends engine. There is more to this extension than meets the eye. It has two counterbores machined on the far end, one to precisely fit the flywheel hub, and one to match the 1/2" length of crankshaft that extended past the flywheel hub. The end you can't see is drilled and tapped six places to match the clearance holes in the flywheel. You can see that in the pulley I removed in order to fit the extension on. In a perfect world, there will be no wobble in the end of that shaft extension when the engine is running. The 20 tooth gear, bushing, and drive dog will all be fitted to this extension. I machined two grooves in the large outside diameter of the extension in case I want at some point to drive o-ring drive belts with this engine.
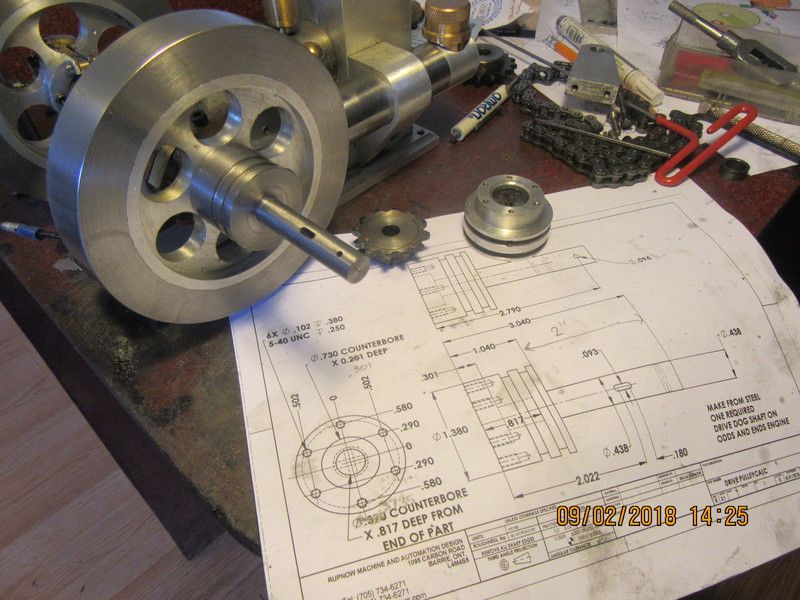