I took a look through my aluminum scrap stockpile and of course, as luck will have it, I didn't have any 1/4" plate.--So---I used a peice of 3/8" material. (I will flycut it down to 1/4" thick.) I have layed out the overall outlines with a scriber and compass and protractor. The black marker is only there to make things show up in the photograph. You will also see that I have marked one side of the plate as "good side" in marker---thats to make sure all my measurements are taken fron the same side of the plate. My little milling vice will only open to about 2 7/8" wide, so I will use a peice of "sacrificial" aluminum plate and clamp this plate directly over it to my mill table to drill all the holes in it. While I have it clamped down I will also drill the five 9/16" diameter holes in the crotch of all 5 spokes to form the 0.281" radii between them. I will flip the plate over and flycut the far side to prevent milling away all my layout lines. After all the holes are drilled, I will use the bandsaw to cut the material away from between the spokes, then stand the plate up in my mill vice to drill the 1/16" holes thru from the ends of the spokes to the center air annulus.
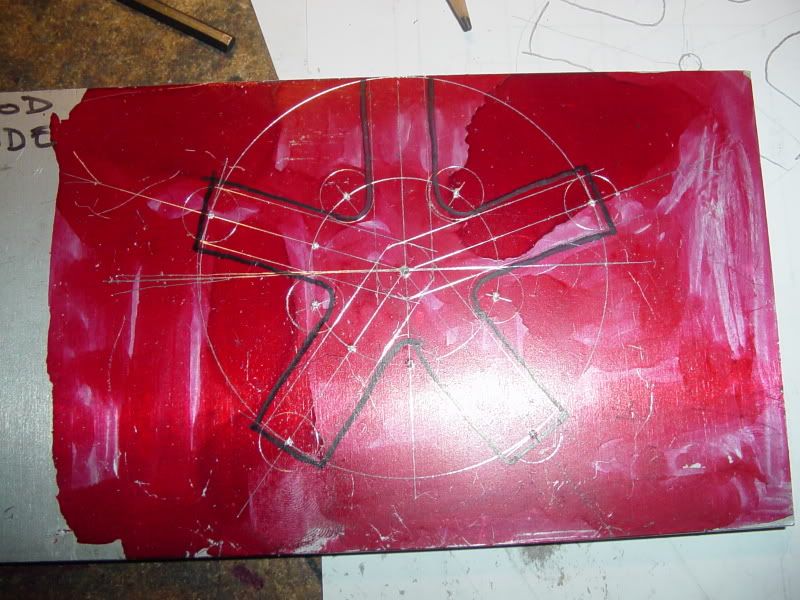