How are you going with those Mod 1 cutters you bought, Bazmak?
Just to throw in my two cents' worth, here's a few pics of my latest gearcutting, using a 32DP cutter from RDG tools to make the secondary worm wheel for my GH Thomas dividing head I am making from welded-together bits of scrap. I used a Myford 60T changewheel for the main gear and turned a worm to fit it. I got away from having to offset the worm at the helix angle to mesh with the straight gear by turning the thread a bit thin and angling the worm around straight.
But to cut the second, smaller wormwheel for the ultra fine adjustment on this dividing head, I ended up angling the blank at 4.2 degrees to the cutter and so the teeth are at the right angle to match the helix of the worm. Not a helical gear, but more a straight cut gear with angled teeth! And it works a treat.
Cutting the gear teeth in the lathe (1937 Drummond M-type). The vertical slide is stretched about as high as it can go. Should really have a spacer block underneath, but hey we got away with it! Used a jury rigged plunger on the main wormwheel for direct indexing.
The resulting gear, with 4.2 degree "helical" teeth
And matching worm
How it all fits together
Index plates will attach to the small wormwheel on the left. A graduated micro-adjustment goes on the worm spindle on the right for dividing prime numbers etc, and making the dividing head's own indexing plates from scratch.
In the end, I was glad I spent the money on the commercial cutter. The two inch diameter steel gear, 5/16 thick would have been a long slow job with a single tooth flycutter and I don't think the vertical slide would be stout enough to take much of a cut, it was bouncing about enough under the smooth sailing of the commercial cutter.
Just to throw in my two cents' worth, here's a few pics of my latest gearcutting, using a 32DP cutter from RDG tools to make the secondary worm wheel for my GH Thomas dividing head I am making from welded-together bits of scrap. I used a Myford 60T changewheel for the main gear and turned a worm to fit it. I got away from having to offset the worm at the helix angle to mesh with the straight gear by turning the thread a bit thin and angling the worm around straight.
But to cut the second, smaller wormwheel for the ultra fine adjustment on this dividing head, I ended up angling the blank at 4.2 degrees to the cutter and so the teeth are at the right angle to match the helix of the worm. Not a helical gear, but more a straight cut gear with angled teeth! And it works a treat.
Cutting the gear teeth in the lathe (1937 Drummond M-type). The vertical slide is stretched about as high as it can go. Should really have a spacer block underneath, but hey we got away with it! Used a jury rigged plunger on the main wormwheel for direct indexing.
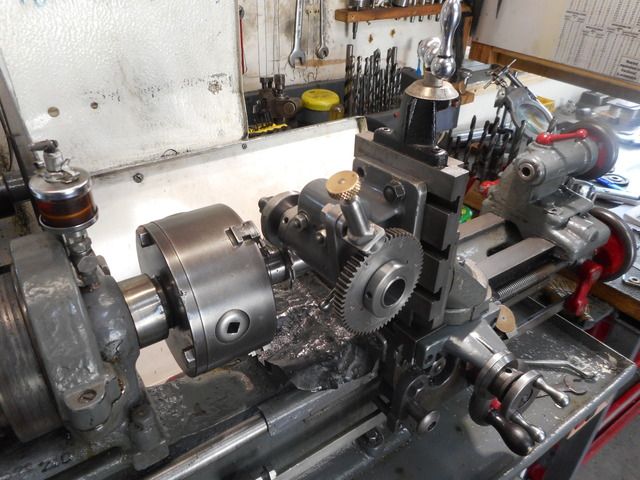
The resulting gear, with 4.2 degree "helical" teeth
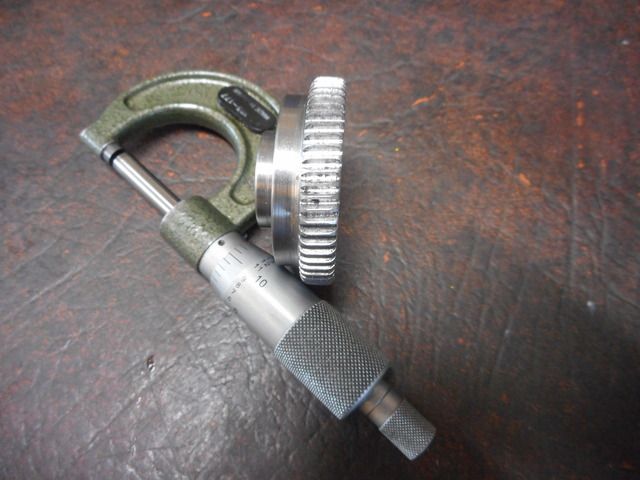
And matching worm
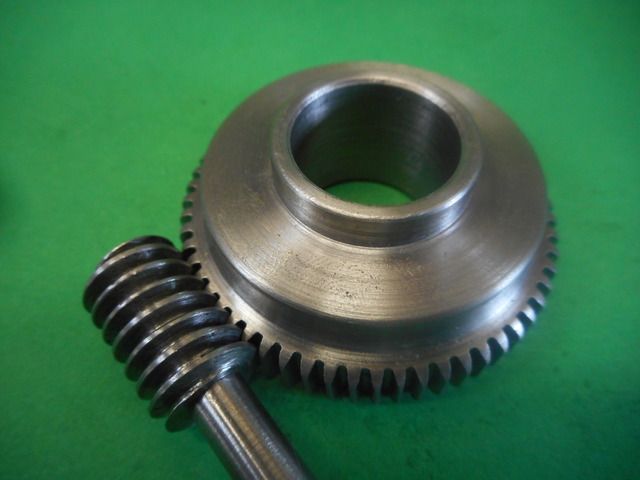
How it all fits together
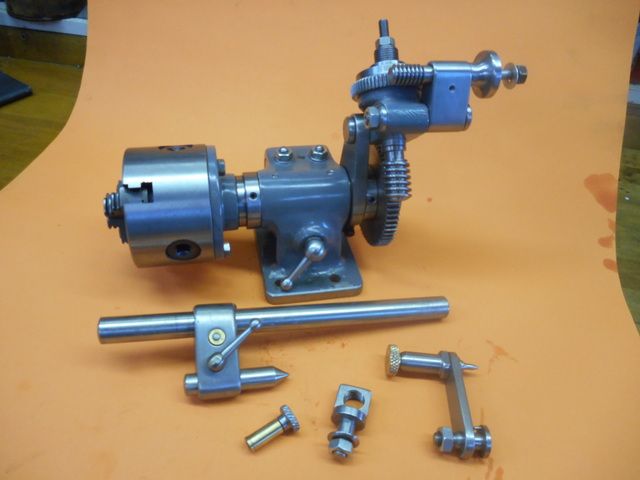
Index plates will attach to the small wormwheel on the left. A graduated micro-adjustment goes on the worm spindle on the right for dividing prime numbers etc, and making the dividing head's own indexing plates from scratch.
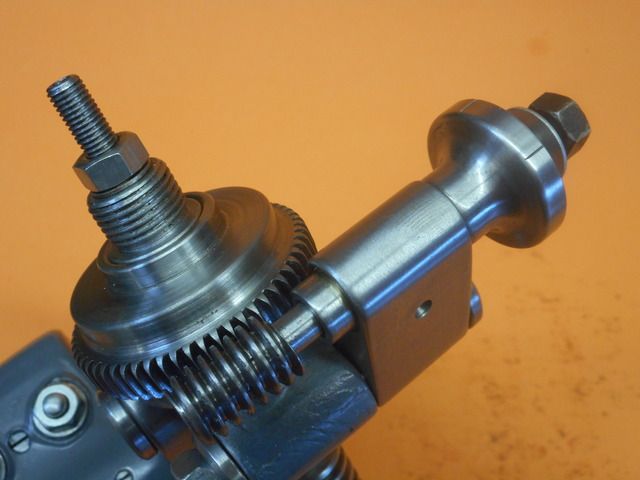
In the end, I was glad I spent the money on the commercial cutter. The two inch diameter steel gear, 5/16 thick would have been a long slow job with a single tooth flycutter and I don't think the vertical slide would be stout enough to take much of a cut, it was bouncing about enough under the smooth sailing of the commercial cutter.