- Joined
- Feb 25, 2008
- Messages
- 464
- Reaction score
- 7
I dont have room for a permanent soldering hearth, so after having to move and stack firebrick off and on the bench in order to have a place to solder I decided to make a portable hearth. I wanted one that could be easily moved and stored on a shelf and that could be used on any type of surface. It also needed to have back and side barriers to protect bench top items from the torch flame.
Heres what I came up with.
Its 12 x 12 and the sides are 4 high. The lining is 1/2 Solderite board which is a ceramic fiber board. I got my board at a swap meet, but its available on-line from jeweler supply stores under soldering supplies. It saws easily, is a great heat reflector and cools down quickly.
The hearth is made from 18 gauge steel sheet. I dont have a welder so I riveted the back edges. The front edges were rigid enough without rivets.
Two angle brackets are fastened to the bottom to provide an insulating air space between the hearth and the bench top (I got this idea from a thread on this board, but cant find the thread. Whoever you were, thanks!)
Ive tried it and with the solderite board and the air gap theres hardly any heat transfer to the bench top. Im comfortable using the hearth on any type of surface.
Actual soldering is done on an auxiliary piece of solderite board with fire brick and solderite reflectors/enclosures built as necessary.
Ive used the hearth a few times now, and I think its really going to work out well. Wish Id have made it a long time ago.
Regards,
Dennis
Heres what I came up with.
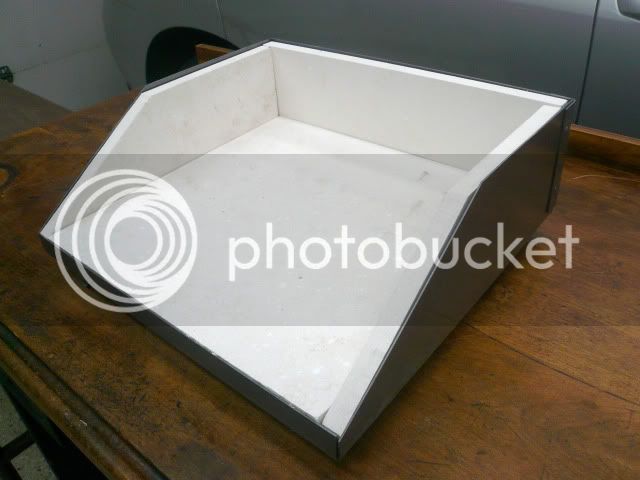
Its 12 x 12 and the sides are 4 high. The lining is 1/2 Solderite board which is a ceramic fiber board. I got my board at a swap meet, but its available on-line from jeweler supply stores under soldering supplies. It saws easily, is a great heat reflector and cools down quickly.
The hearth is made from 18 gauge steel sheet. I dont have a welder so I riveted the back edges. The front edges were rigid enough without rivets.
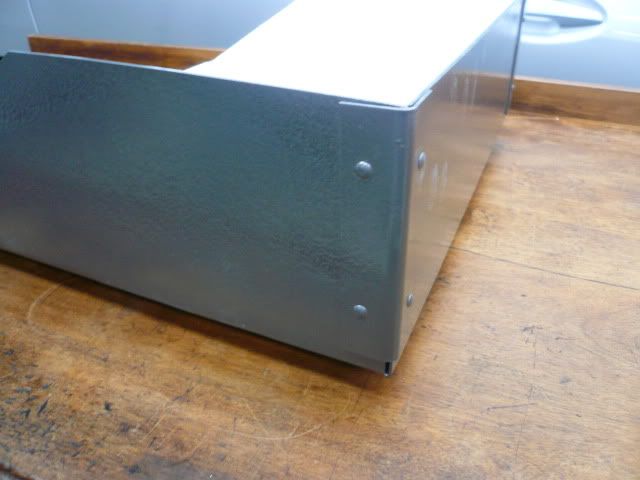
Two angle brackets are fastened to the bottom to provide an insulating air space between the hearth and the bench top (I got this idea from a thread on this board, but cant find the thread. Whoever you were, thanks!)
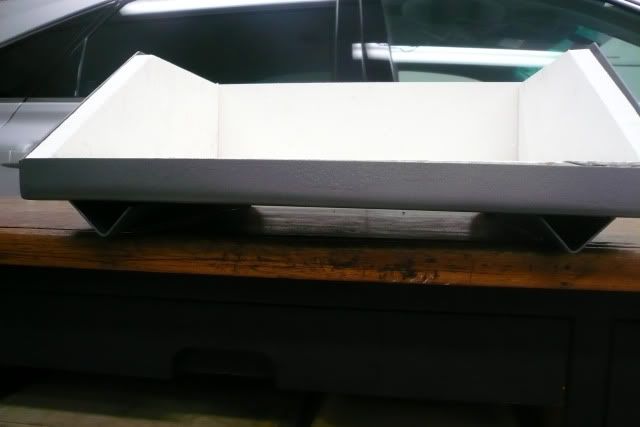
Ive tried it and with the solderite board and the air gap theres hardly any heat transfer to the bench top. Im comfortable using the hearth on any type of surface.
Actual soldering is done on an auxiliary piece of solderite board with fire brick and solderite reflectors/enclosures built as necessary.
Ive used the hearth a few times now, and I think its really going to work out well. Wish Id have made it a long time ago.
Regards,
Dennis