I've not posted a build here for very long time but thought why not.
Having recently enjoyed making the Gamages and Bassett Lowke small marine steam engines the next engine to catch my eye while looking for something else was C W Woodson's "Little Husky" as it was a similar type engine and being a Uniflow would allow me to tick off making one of those too. It also had those tempting words "Requires no Castings"
The original article appeared in Popular Science Magazine in 1944 and can be read here
There have been a few of these built on the various forums and even Julius has done a version but they all looked a bit heavy and bulky to my eye. So as well as redrawing it in metric I set about putting this little puppy on a diet and adding a few curves and features while I was at it. The main areas of attention are:
- Entablature and Base. Both made of thinner material and some additional machining to remove excess metal and add some shape particularly to the entablature and I also added some holes so it could be mounted in a hull if needed.
- Columns. Reduced in number from six to four, smaller diameter and also a bit taller with a tapered profile rather than just straight bar.
- Bearing Supports. A couple of holes to reduce bulk and separate bronze bearings added
- Cylinder / Valve chest. Rather than solder two cylinders together I cut this from solid. The valve hole was reamed right through rather than try and ream a blind hole to the end, this also made lapping the valve into the hole easier.
And this is what I came up with after a couple of hours with Alibre
Having recently enjoyed making the Gamages and Bassett Lowke small marine steam engines the next engine to catch my eye while looking for something else was C W Woodson's "Little Husky" as it was a similar type engine and being a Uniflow would allow me to tick off making one of those too. It also had those tempting words "Requires no Castings"
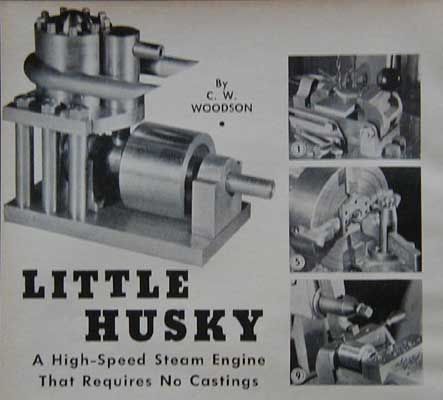
The original article appeared in Popular Science Magazine in 1944 and can be read here
There have been a few of these built on the various forums and even Julius has done a version but they all looked a bit heavy and bulky to my eye. So as well as redrawing it in metric I set about putting this little puppy on a diet and adding a few curves and features while I was at it. The main areas of attention are:
- Entablature and Base. Both made of thinner material and some additional machining to remove excess metal and add some shape particularly to the entablature and I also added some holes so it could be mounted in a hull if needed.
- Columns. Reduced in number from six to four, smaller diameter and also a bit taller with a tapered profile rather than just straight bar.
- Bearing Supports. A couple of holes to reduce bulk and separate bronze bearings added
- Cylinder / Valve chest. Rather than solder two cylinders together I cut this from solid. The valve hole was reamed right through rather than try and ream a blind hole to the end, this also made lapping the valve into the hole easier.
And this is what I came up with after a couple of hours with Alibre
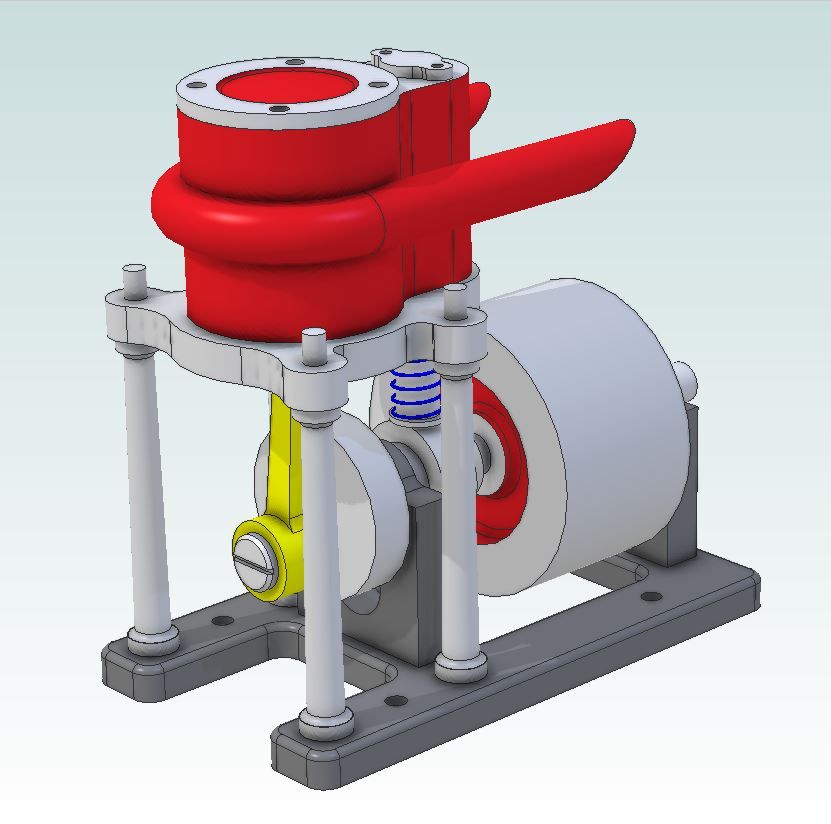
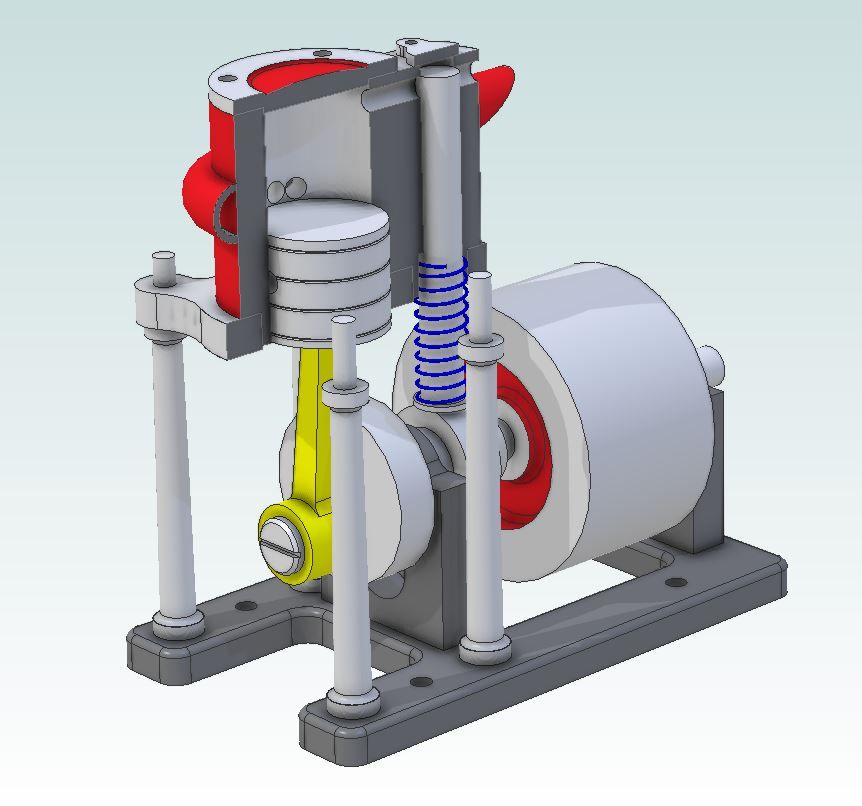