- Joined
- Apr 3, 2011
- Messages
- 192
- Reaction score
- 305
Right, here we go again!
I've decided on a V10 this time, just to be different.
And I'm going up a scale, as with the V8 everything seemed to be just slightly too small to make a proper job. Maybe my eyesight is going, or I need smaller fingers.
Bore will be 1", capacity about 125cc.
I want a 90 degree block, but even firing, which means a split journal crank!
Not solved that one yet, but should be doable.
Not too much design work done yet, but I've started with the boring bits, which is conrods, pistons and crank, as they'll be pretty standard whatever the engine looks like.
I do know now, after the smoking issues on the V8 that I'm going for 3 rings on the pistons. 2 above the pin and 1 below. I'm also making the rings a bit thicker and wider than last time, to get a bit more sealing. This is on top of the scale factor of course.
Anyway, rods first:-
I've decided on a V10 this time, just to be different.
And I'm going up a scale, as with the V8 everything seemed to be just slightly too small to make a proper job. Maybe my eyesight is going, or I need smaller fingers.
Bore will be 1", capacity about 125cc.
I want a 90 degree block, but even firing, which means a split journal crank!
Not solved that one yet, but should be doable.
Not too much design work done yet, but I've started with the boring bits, which is conrods, pistons and crank, as they'll be pretty standard whatever the engine looks like.
I do know now, after the smoking issues on the V8 that I'm going for 3 rings on the pistons. 2 above the pin and 1 below. I'm also making the rings a bit thicker and wider than last time, to get a bit more sealing. This is on top of the scale factor of course.
Anyway, rods first:-
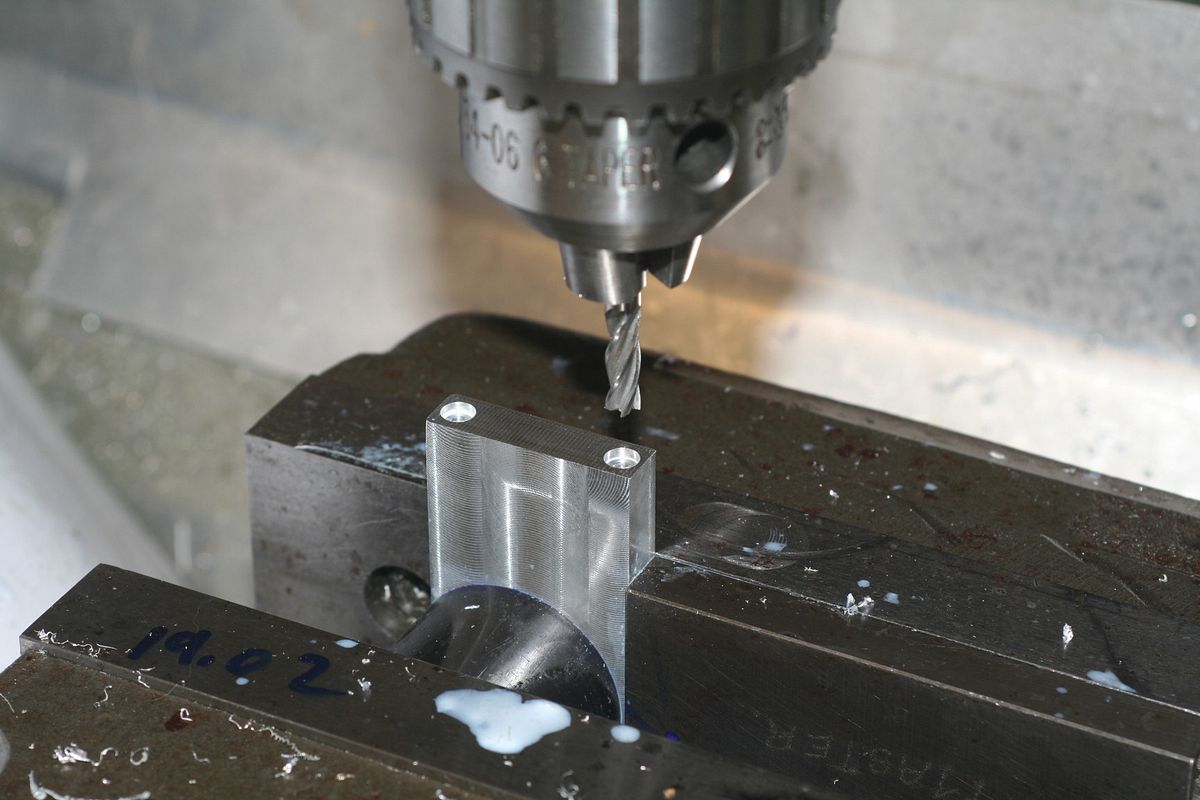
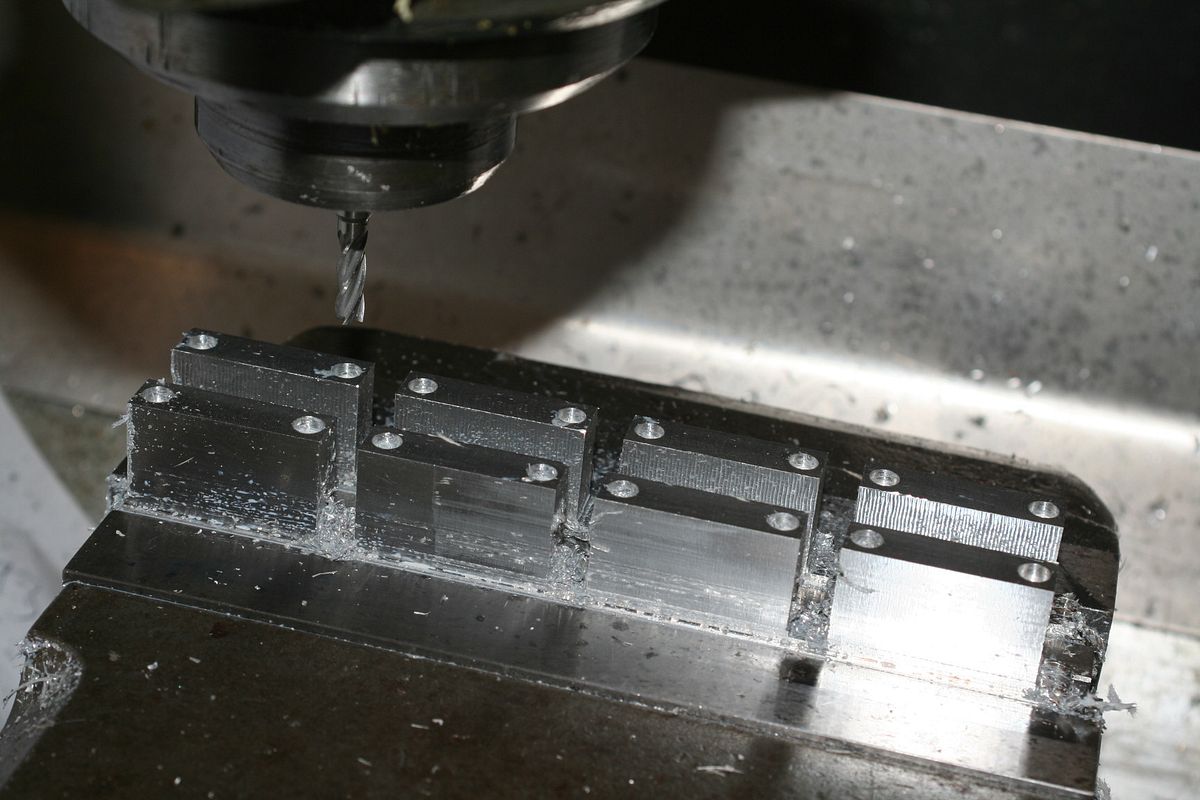
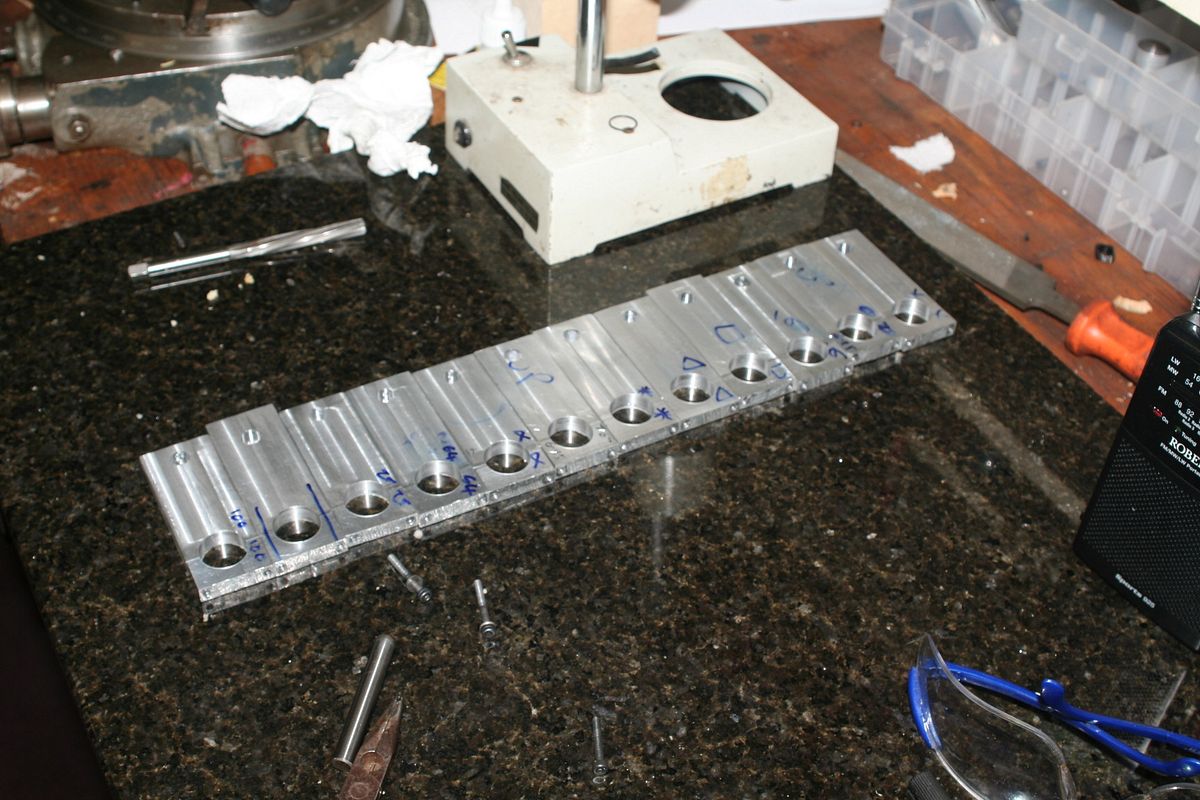
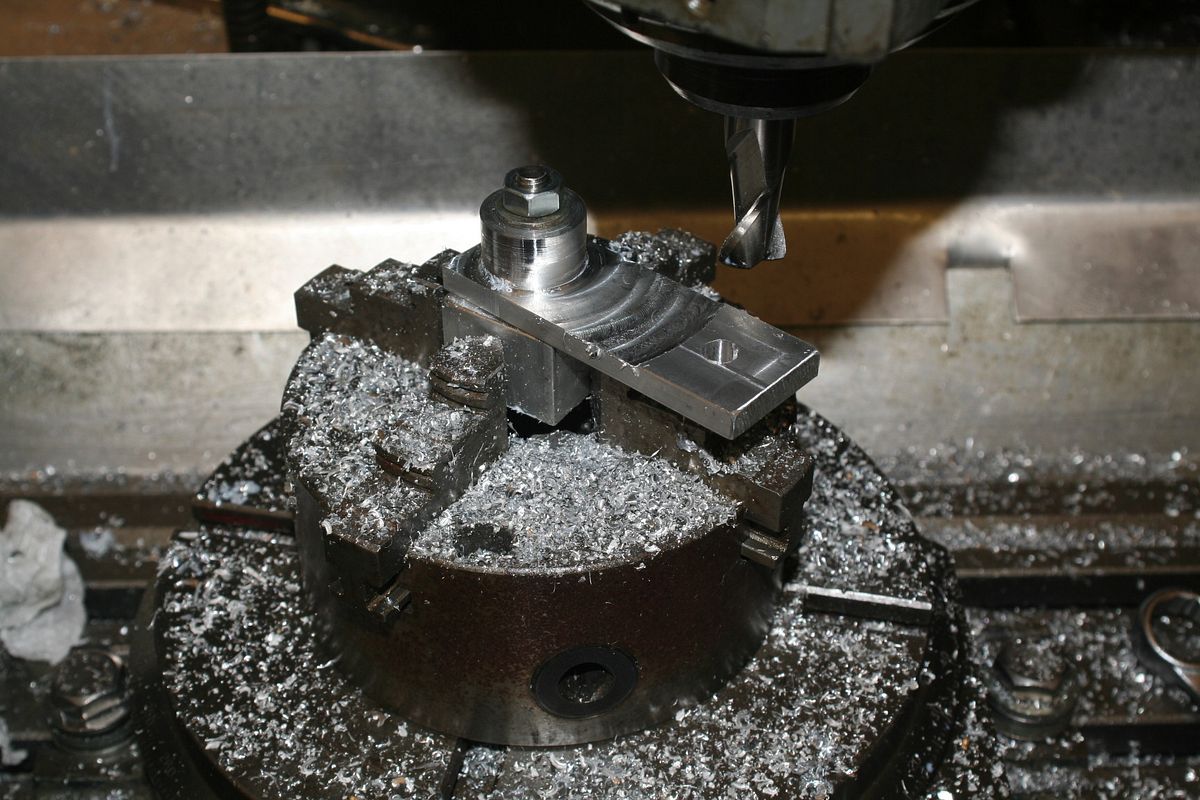
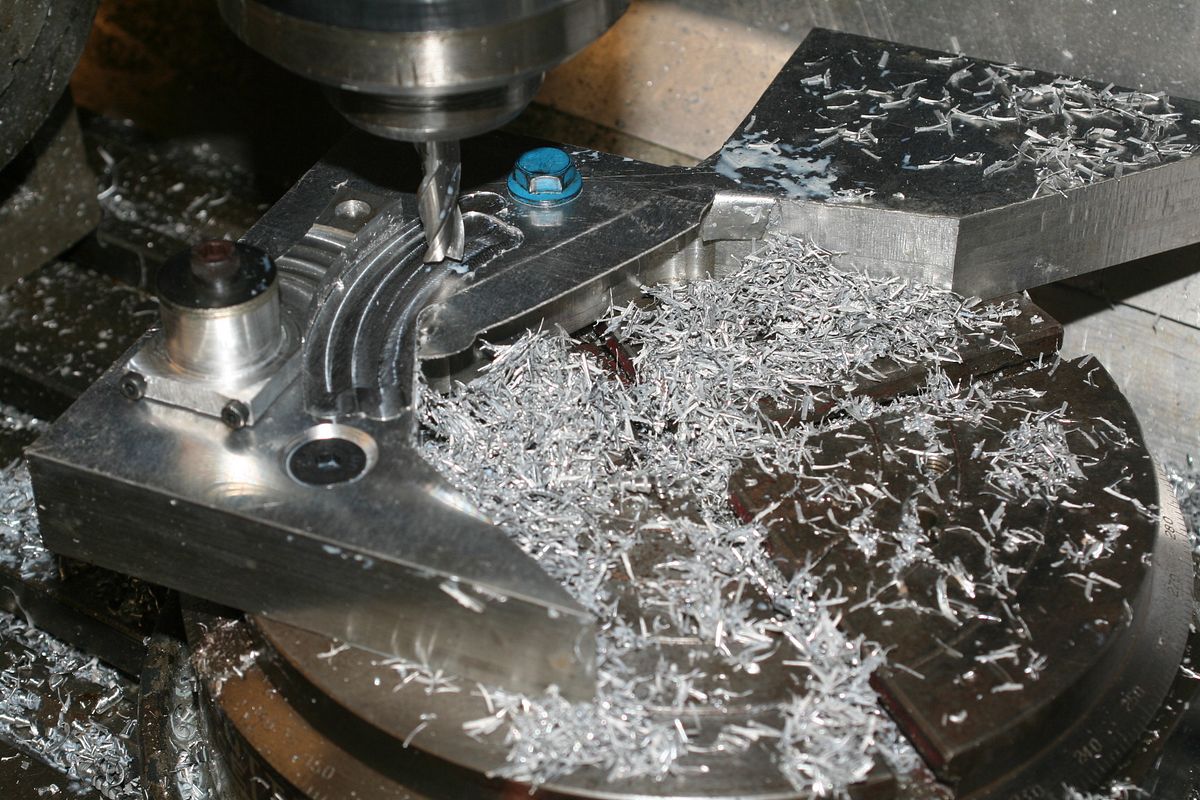
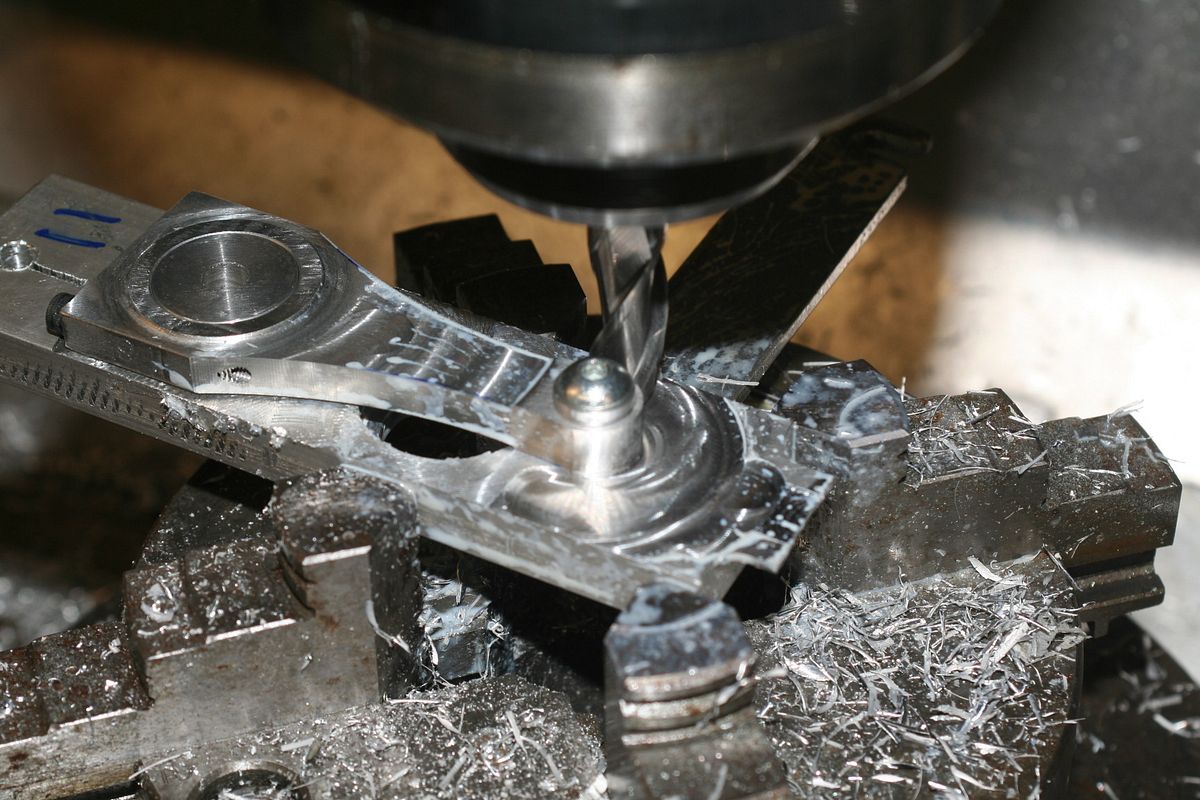
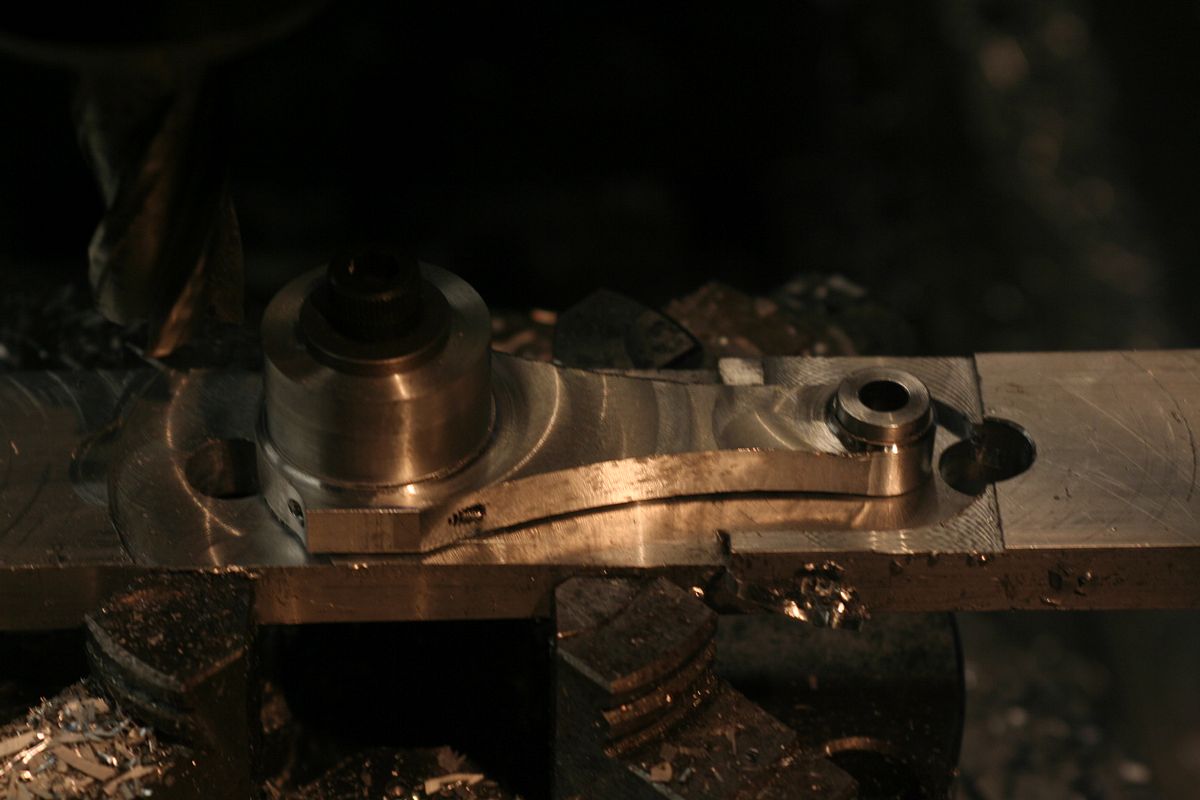