And---One hard days machining yields the frame. I don't have a lot to say about this---it's just a days steady slugging. One thing--My drawing shows 1/2" radii at the bottom of the vertical pillar. To get a 1/2" radius you need to drill a hole with a 1" drill. My old smaller mill couldn't have handled this easily if at all. So---If your mill blows fuses trying to drill a 1" diameter hole you might want to settle for 1/4" radius and drill thru with a 1/2" drill. And yes, that is one of the ball bearings setting in it's counterbore. I dropped it in for test fit after boring the hole and in it went---then I had no way to get it out until I removed the piece for a different set-up.
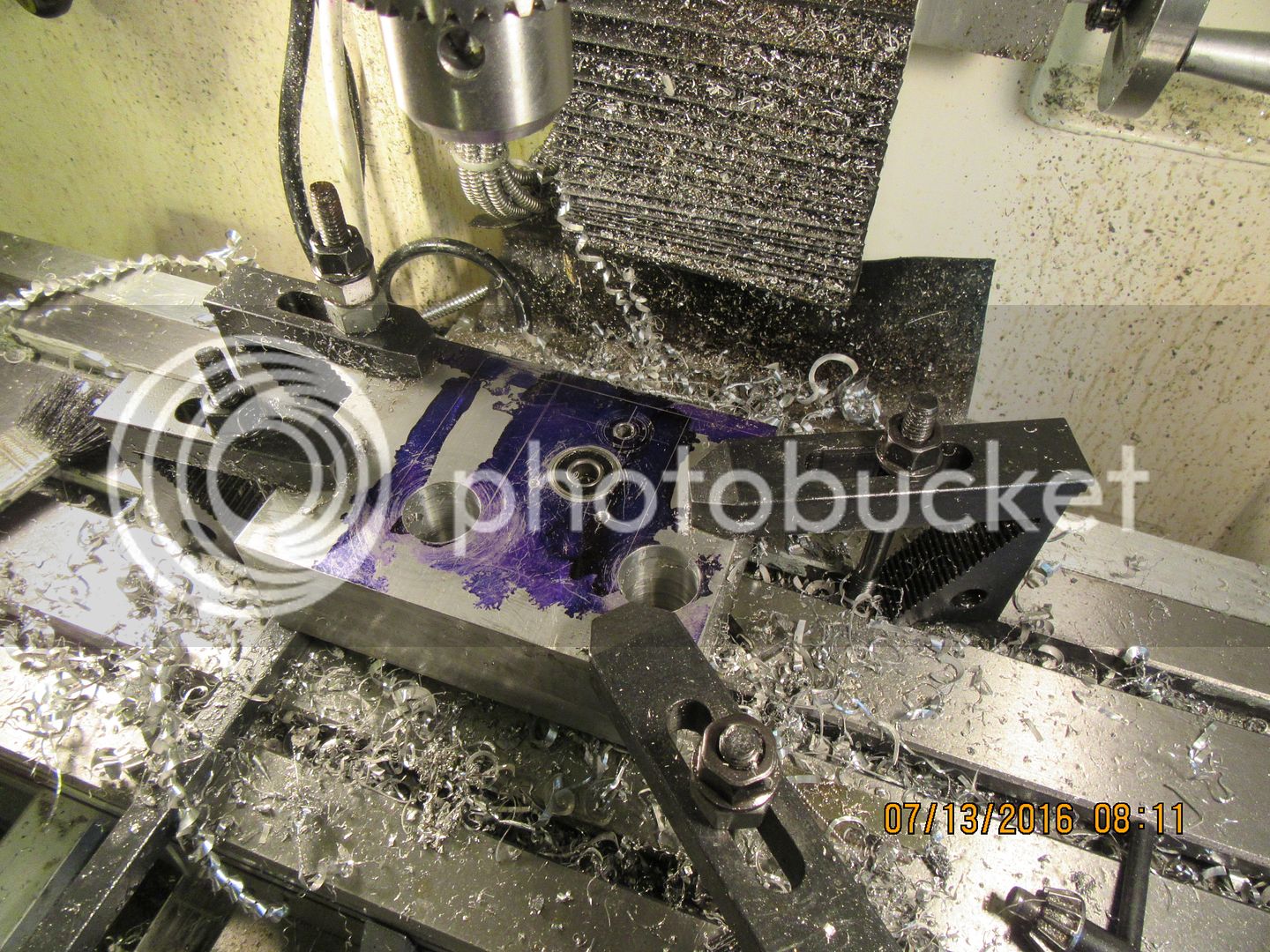
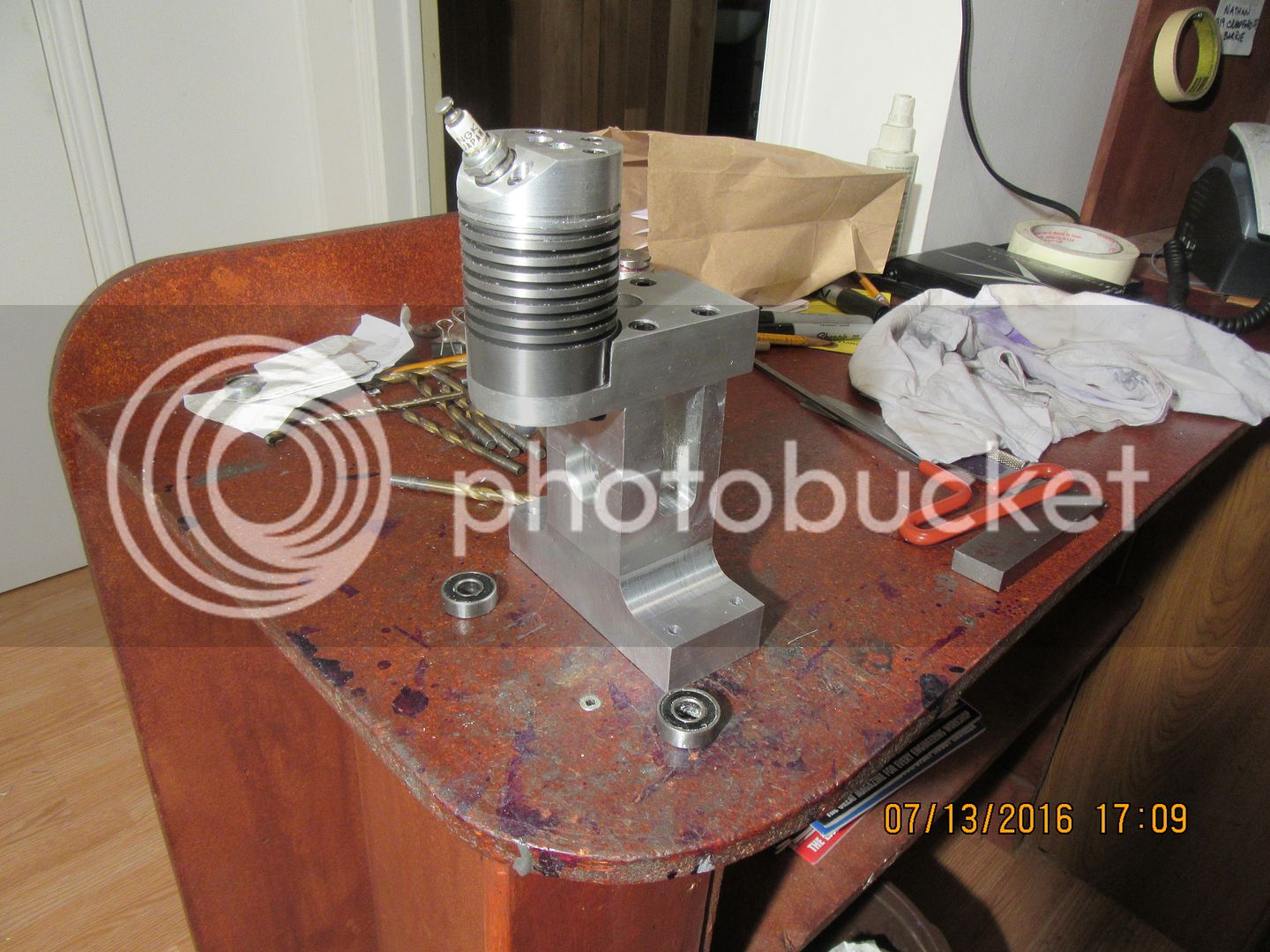