WOWZA!!! Ya never know your luck in the big city. I remembered having a 30 tooth gear in my shelf of "things recovered from old projects" and I did. But---amaze me--I had a 60 tooth gear in there that I had forgotten all about. Both gears will require a bit of creative hub rework, but not near as much work as setting up and cutting new gears.
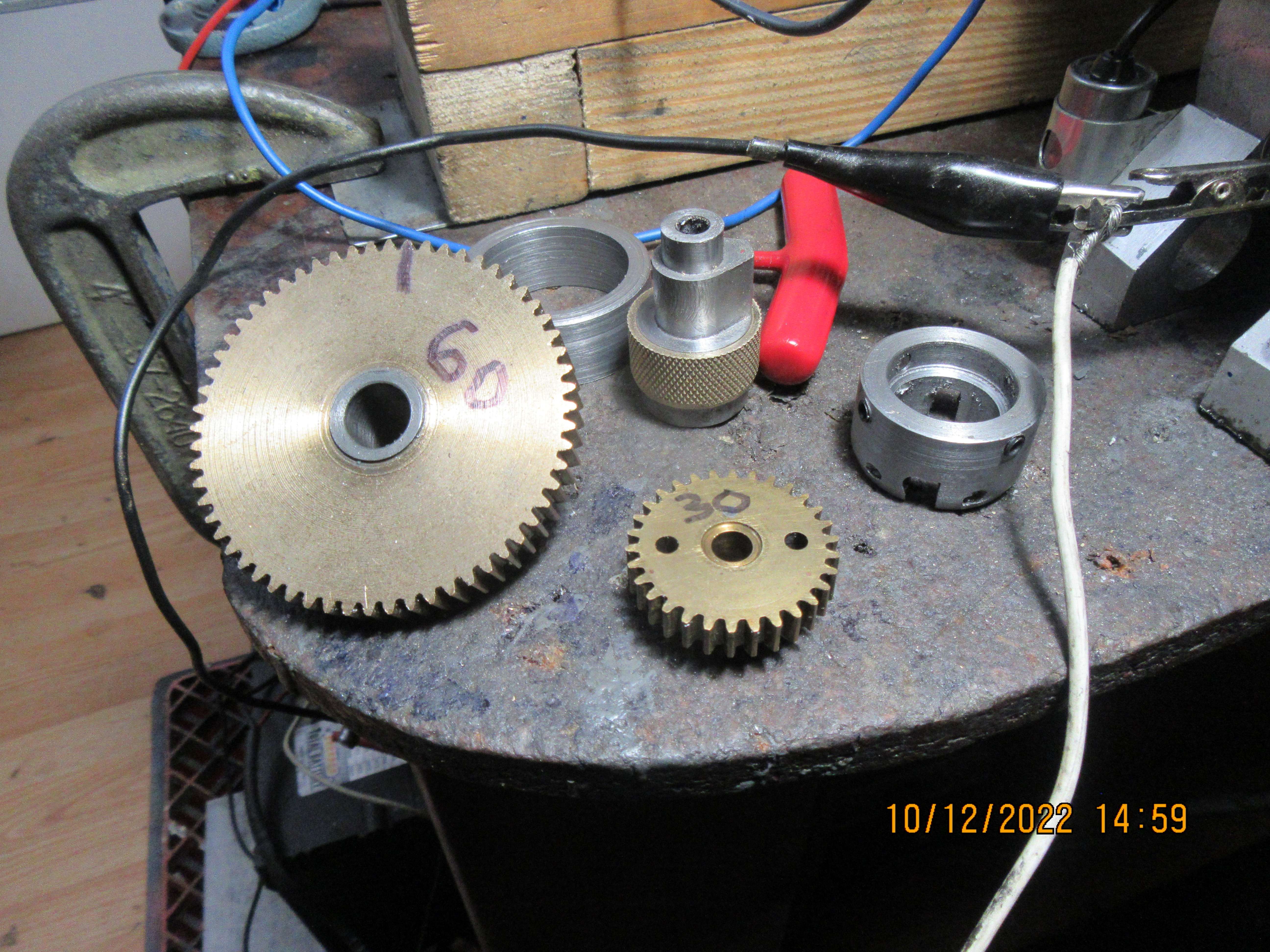