rodw
Well-Known Member
- Joined
- Dec 2, 2012
- Messages
- 1,146
- Reaction score
- 340
Hi guys, I just wondered if you can help me out here? It is a simple question, so please bear with me,
I have a part I make
It is pretty simple really. It is 100 mm x 32mm x 8mm mild steel. It has two holes. One is tapped to M8 and the other is countersunk for an M8 machine screw.
I started off building this from scratch out of 8mm x 32 mm bar stock but then I got a bit cunning and had it laser cut. This worked OK and then I got lazy and sent the whole job out 100 at a time and it came back finished and powder coated. The price went up so last time, I ordered 300 of them and went back to tapping and countersinking them on my drill press. So far I have finished 200 of them and have about 100 to go. For some reason in this batch, every now and again I hit a hard piece of steel and I have ruined a couple of countersinking tools (after making hundreds with my first one). I figured that somehow the steel has been hardened in the laser cutting process.
I tried an indexable countersinker for $33 but have ruined all 3 sides of the included cutter so I am not keen on buying $100 worth of inserts to continue down that path!
So anyway, I decided to finally do something serious with my mill and machined the jig I made years ago before I bought a lathe/mill. I was able to square the jig up so the sides held in the vice are parallel with the part and I indicated it in using an edge finder.
I cut one with a blunt countersink which lined up nicely and am going to buy another tool in the morning so my long winded question is:
"What is the ideal RPM for a countersink operation like this?"
Oh and in case you were wondering, I used a tapping tool in the drill press to cut the threads and it was easy as to thread the 300 holes.
I have a part I make
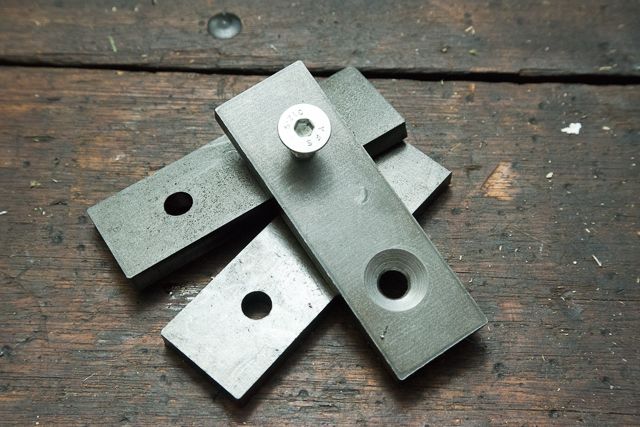
It is pretty simple really. It is 100 mm x 32mm x 8mm mild steel. It has two holes. One is tapped to M8 and the other is countersunk for an M8 machine screw.
I started off building this from scratch out of 8mm x 32 mm bar stock but then I got a bit cunning and had it laser cut. This worked OK and then I got lazy and sent the whole job out 100 at a time and it came back finished and powder coated. The price went up so last time, I ordered 300 of them and went back to tapping and countersinking them on my drill press. So far I have finished 200 of them and have about 100 to go. For some reason in this batch, every now and again I hit a hard piece of steel and I have ruined a couple of countersinking tools (after making hundreds with my first one). I figured that somehow the steel has been hardened in the laser cutting process.
I tried an indexable countersinker for $33 but have ruined all 3 sides of the included cutter so I am not keen on buying $100 worth of inserts to continue down that path!
So anyway, I decided to finally do something serious with my mill and machined the jig I made years ago before I bought a lathe/mill. I was able to square the jig up so the sides held in the vice are parallel with the part and I indicated it in using an edge finder.

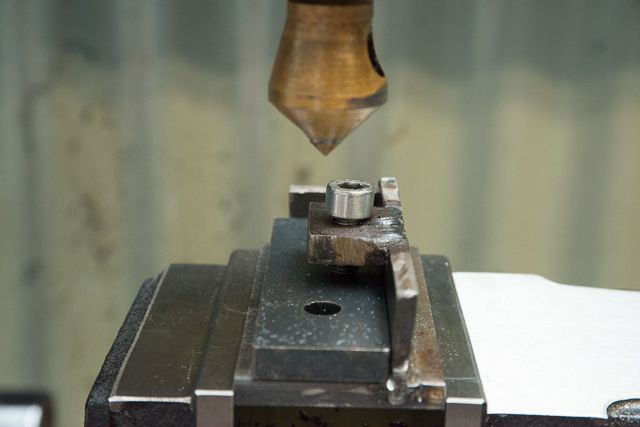
I cut one with a blunt countersink which lined up nicely and am going to buy another tool in the morning so my long winded question is:
"What is the ideal RPM for a countersink operation like this?"
Oh and in case you were wondering, I used a tapping tool in the drill press to cut the threads and it was easy as to thread the 300 holes.
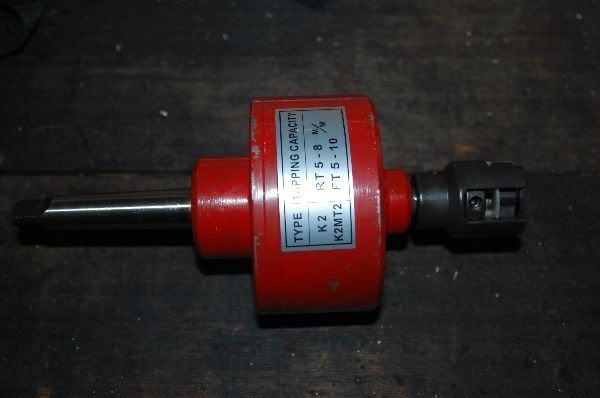