Allen
Well-Known Member
- Joined
- Jul 14, 2008
- Messages
- 128
- Reaction score
- 55
Since this doesn't really fit anywhere else, I thought I'd put it here...
About a decade ago our local antique machinery club was donated a collection of steam pumps from a longtime member's estate. Originally they were going to build a stepped rack (something like bleachers) to display them on. It never happened. Instead most of them were put "into storage" (ie dumped in the tree line at the bottom of the showgrounds.)
A couple years ago my fiancee Kim decided that these orphans really needed rescued. So she started to paint them right where they were. This Transit duplex is the largest of the ones in this lot.
A bit later, Kim and I decided that putting them on a wagon just might be better than waiting on the club to decide to scrap them or leaving them in the weeds for the scrappies to steal..... Except we didn't have one.
Last year a family friend was scrapping out a bunch of old rotted machinery. So I purchased a pair of axles with steel wheels from him for $35. A steering axle from a wagon type manure spreader, and a straight axle out from under a husker shredder..... Except I couldn't get them hauled until this Spring.... Meanwhile, the guy who was cutting up the scrap got a little torch happy and cut away all the steering parts from MY axle. Grrrrrrrr!
The guy felt bad and gave me another set of steering parts. They looked close, but weren't quite right. So I spent over 3 hours making them fit. I needed to lengthen the tie bar almost 4", so I got the bright idea of splicing it in the center. Then I had to graft on the part that holds the tongue since that was burnt off as well.... It doesn't look factory purty but it should be serviceable.
Then I had to widen the rear axle just a little to match the front. While I was at it I welded a smaller pipe inside the axle pipe to give it a bit more strength.
Welding in 90+ degree early Summer weather wasn't much fun, but soon they were a (mis)matched pair.
Next step was to weld mounting perches on the rear axle. Which was finished the 3rd week of June. After that I wanted to get a couple 12 foot 4x6 or perhaps even 6x6 beams for the sills. The big pump (about a 6x7x6) goes directly over the rear axle, and 2 or possibly 3 of the other ones ahead of it. These things are bloody HEAVY, so I figured I may well need to build truss rods before I'm done.
Meanwhile, one of the club directors had already begun poo-poo-ing the whole bloody project. He says that the pumps are "junk"... (I asked if we were a "preservation" group, or scrappies) Since they've been out in the wather so long, I'll probably have to tear into them after they're mounted and see what they'll require to be gotten running again. This may sound backwards, but they'll be at a nice convenient height to work on once they're on the wagon - rather than fighting with them down in the dirt!
About this time the club president told me NOT to buy the sills (about $80) because the club had a couple ash logs they would cut for me. So i didn't. And they didn't. July slipped past, then the 50th show, then half of August and STILL no sills........................................
So, rather than wait any longer, I decided to go another route. Another friend donated me 2 sections of used 12" mobile home frame I beam. He delivered them the third week of August. I decided I'd probably better go over and start mounting them a few days later, before the scrappies saw them. And of course it had to rain.
Tramming everything up took a lot longer than the actual welding did. But the end result is that it's within 1/16" of perfectly square. NO 'dog tracking' allowed! Besides, it gave me something to do while waiting for the rain to quit.
This was the first of many braces. I trust my welds. But I also trust some of the guys in the club. I trust that sooner or later one of them WILL hook a tractor to this thing, rip 'n snort and run it into a doorframe, post, tree, or other bit of machinery.
Since it was getting dark I had to stop there for the day. My last project before leaving was to flip the steering stuff over (I'd somehow managed to mount it upside down!) Luckily that was a 5 minute deal. One big bolt from the pivot, a kotter pins at each end of the tie rod, and turn it all over as a unit. By golly, if it didn't fit even better than it had the other way!
Then we rolled it outside in the rain so nobody could complain that it was in the way.
We had 3 nice days this past week, so I made a lot of progress on this.
I was warned that due to the thin material, mobile home I-beams don't have a lot of side strength. So first I added two vertical X braces made from 3/4" Schedule 80 pipe to help hold the beams square. Since the big pump will be centered over the rear axle, I also put on a pair of braces on the outer stubs to help keep the axle from springing
There was this angled flange on the rear axle, so I decided it was a really good place to attach a horizontal diagonal to help keep the frame from going diamond shape... It looks sort of like a panhard bar.
Since the axle attach point was a little below the bottom I-beam flange, it allowed me to run the other diagonal flat and tie them together.
I then decided I probably needed to put something across the rear for strength and to help minimize the chances of someone punching the end of the beams through a building.
Sadly, I ran out of the real pretty dark blue and couldn't find more, but a local odd lot store had this other "dark" blue on sale for $4 a quart... so far I've used 2 quarts.
The big pump got brought up out of the weeds. It's 5 feet long, and the wagon is 12.... the other pumps will get mounted crosswise.
I was going to salvage the oak skids to place crosswise to mount the pump on ... but, while they still looked good on top, they're kind of punky underneath. So I'll have to see if I can find some used channel.
Some fat guy at work....
The wagon itself is pretty much done except for the tongue. It ain't fancy, but it should keep the pumps out of the mud for a bit.
About a decade ago our local antique machinery club was donated a collection of steam pumps from a longtime member's estate. Originally they were going to build a stepped rack (something like bleachers) to display them on. It never happened. Instead most of them were put "into storage" (ie dumped in the tree line at the bottom of the showgrounds.)
A couple years ago my fiancee Kim decided that these orphans really needed rescued. So she started to paint them right where they were. This Transit duplex is the largest of the ones in this lot.
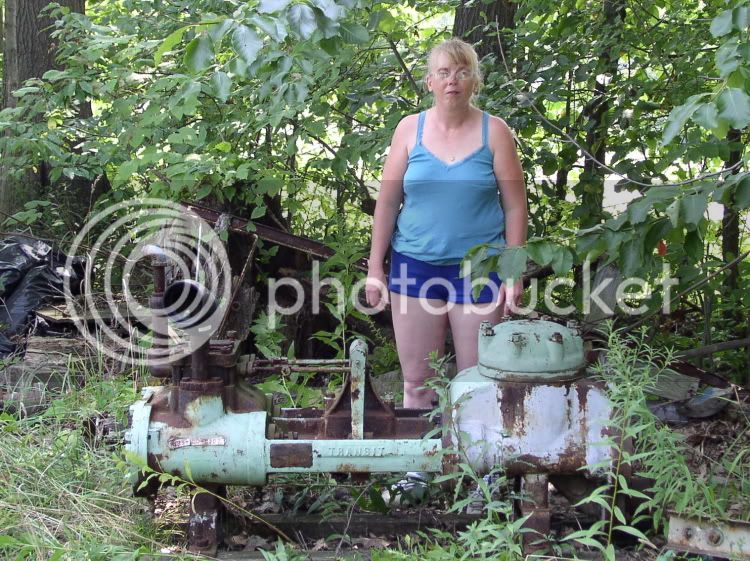
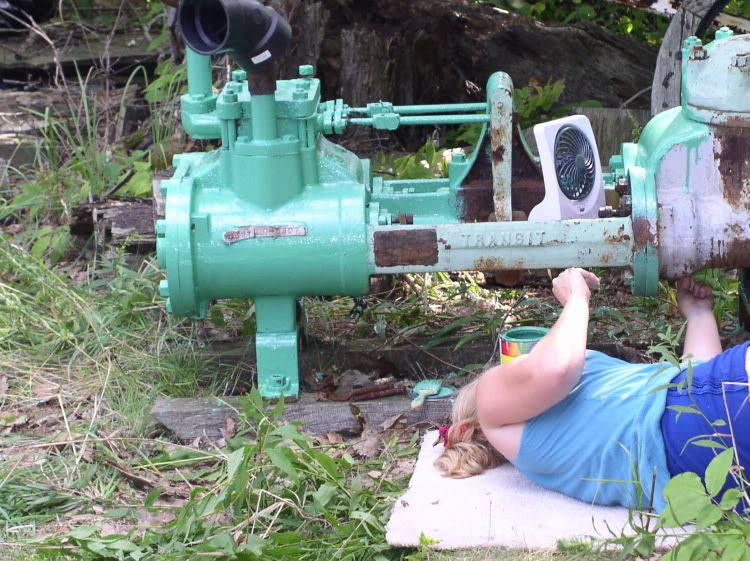
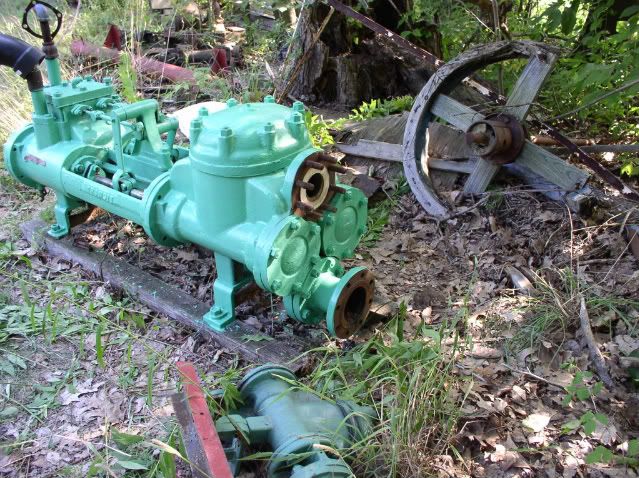
A bit later, Kim and I decided that putting them on a wagon just might be better than waiting on the club to decide to scrap them or leaving them in the weeds for the scrappies to steal..... Except we didn't have one.
Last year a family friend was scrapping out a bunch of old rotted machinery. So I purchased a pair of axles with steel wheels from him for $35. A steering axle from a wagon type manure spreader, and a straight axle out from under a husker shredder..... Except I couldn't get them hauled until this Spring.... Meanwhile, the guy who was cutting up the scrap got a little torch happy and cut away all the steering parts from MY axle. Grrrrrrrr!
The guy felt bad and gave me another set of steering parts. They looked close, but weren't quite right. So I spent over 3 hours making them fit. I needed to lengthen the tie bar almost 4", so I got the bright idea of splicing it in the center. Then I had to graft on the part that holds the tongue since that was burnt off as well.... It doesn't look factory purty but it should be serviceable.
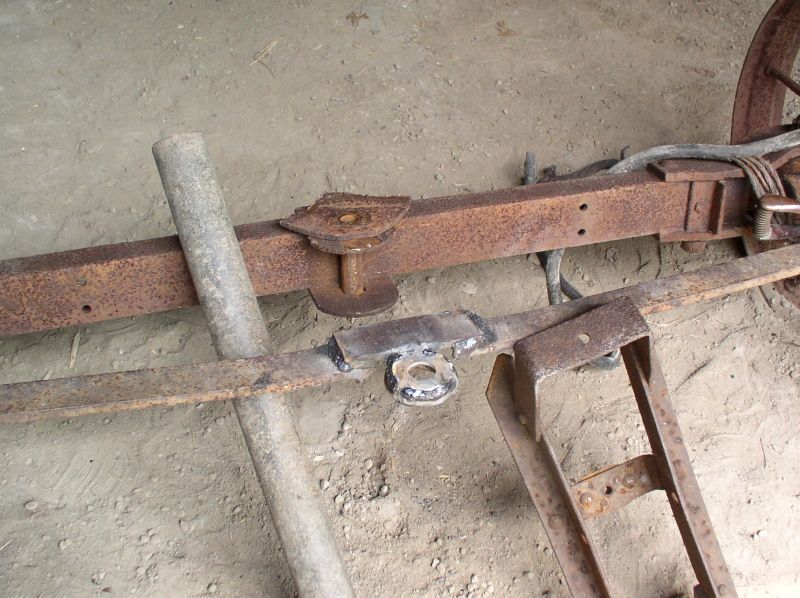
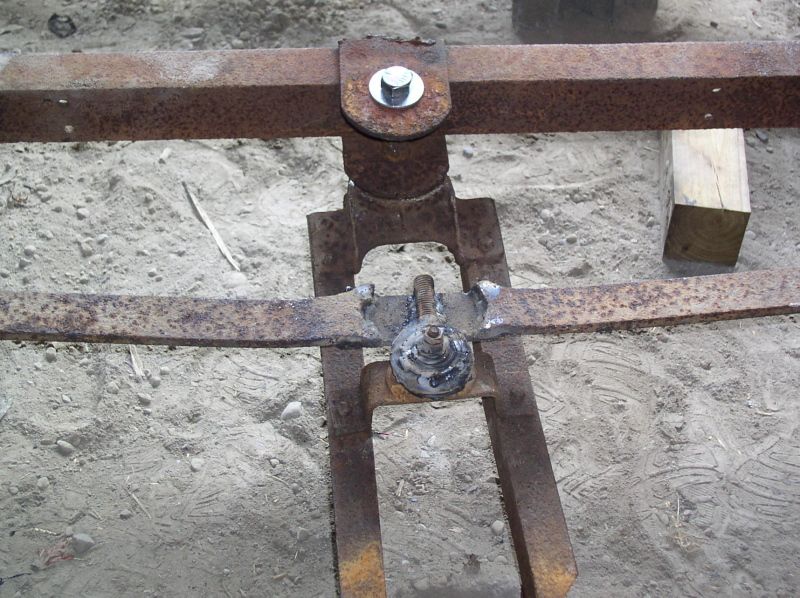
Then I had to widen the rear axle just a little to match the front. While I was at it I welded a smaller pipe inside the axle pipe to give it a bit more strength.
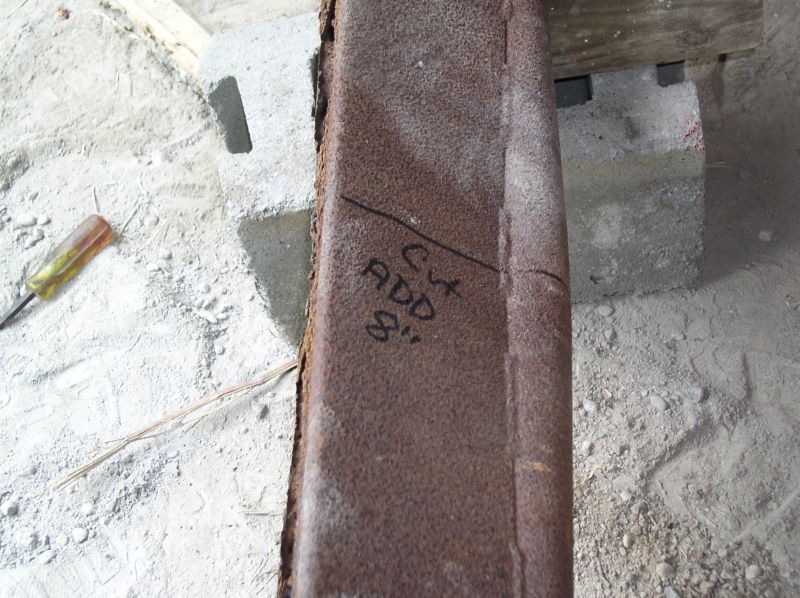
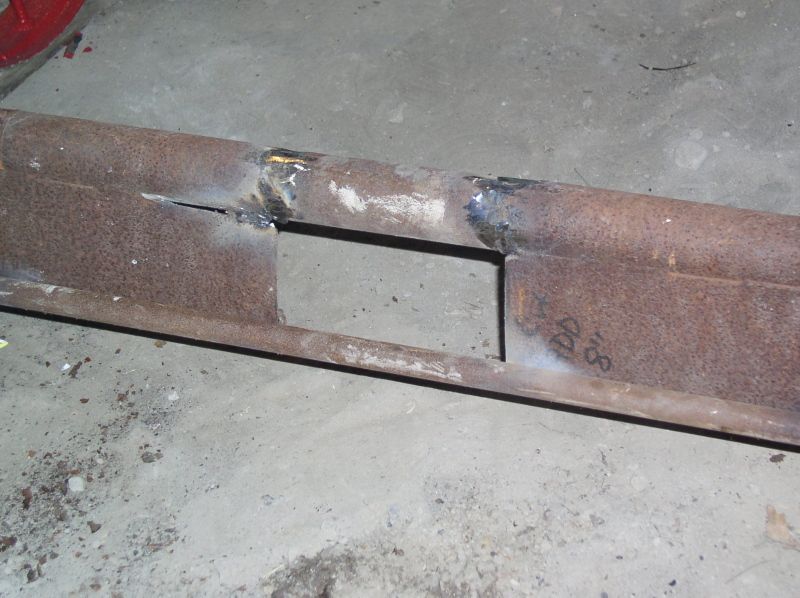
Welding in 90+ degree early Summer weather wasn't much fun, but soon they were a (mis)matched pair.
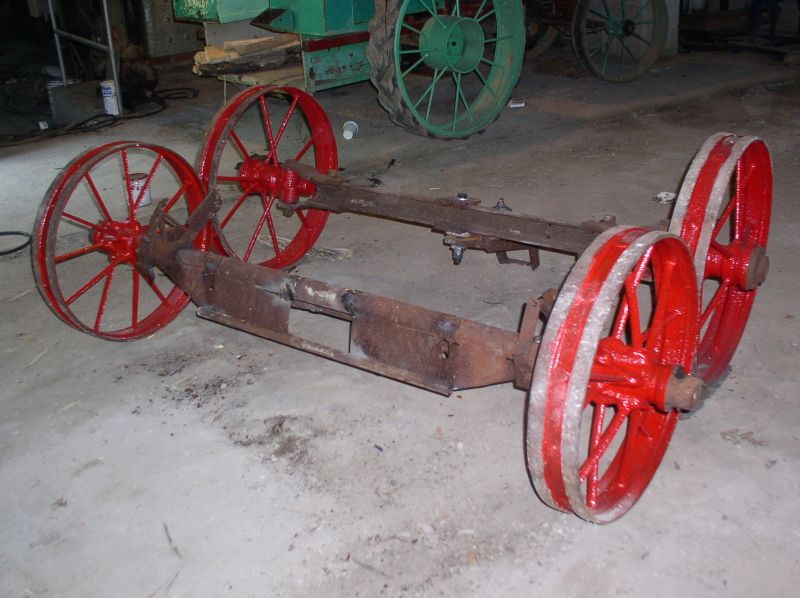
Next step was to weld mounting perches on the rear axle. Which was finished the 3rd week of June. After that I wanted to get a couple 12 foot 4x6 or perhaps even 6x6 beams for the sills. The big pump (about a 6x7x6) goes directly over the rear axle, and 2 or possibly 3 of the other ones ahead of it. These things are bloody HEAVY, so I figured I may well need to build truss rods before I'm done.
Meanwhile, one of the club directors had already begun poo-poo-ing the whole bloody project. He says that the pumps are "junk"... (I asked if we were a "preservation" group, or scrappies) Since they've been out in the wather so long, I'll probably have to tear into them after they're mounted and see what they'll require to be gotten running again. This may sound backwards, but they'll be at a nice convenient height to work on once they're on the wagon - rather than fighting with them down in the dirt!
About this time the club president told me NOT to buy the sills (about $80) because the club had a couple ash logs they would cut for me. So i didn't. And they didn't. July slipped past, then the 50th show, then half of August and STILL no sills........................................
So, rather than wait any longer, I decided to go another route. Another friend donated me 2 sections of used 12" mobile home frame I beam. He delivered them the third week of August. I decided I'd probably better go over and start mounting them a few days later, before the scrappies saw them. And of course it had to rain.
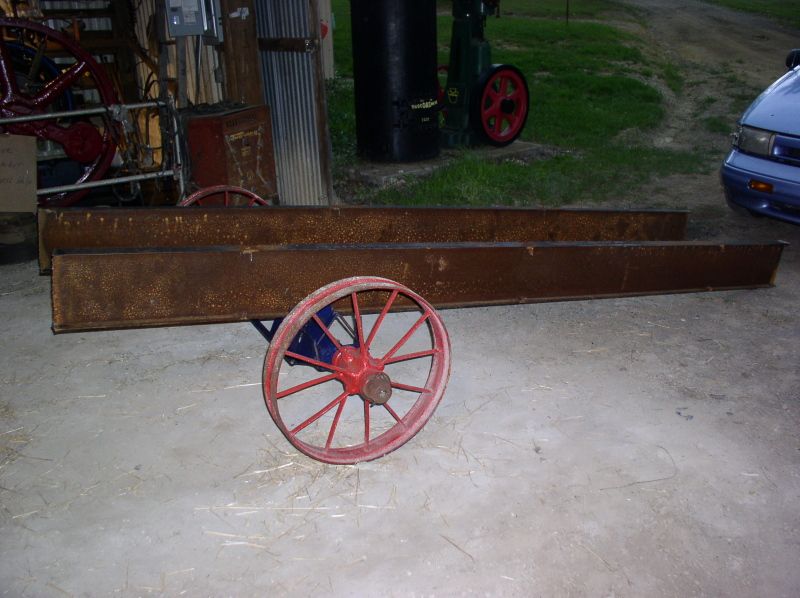
Tramming everything up took a lot longer than the actual welding did. But the end result is that it's within 1/16" of perfectly square. NO 'dog tracking' allowed! Besides, it gave me something to do while waiting for the rain to quit.
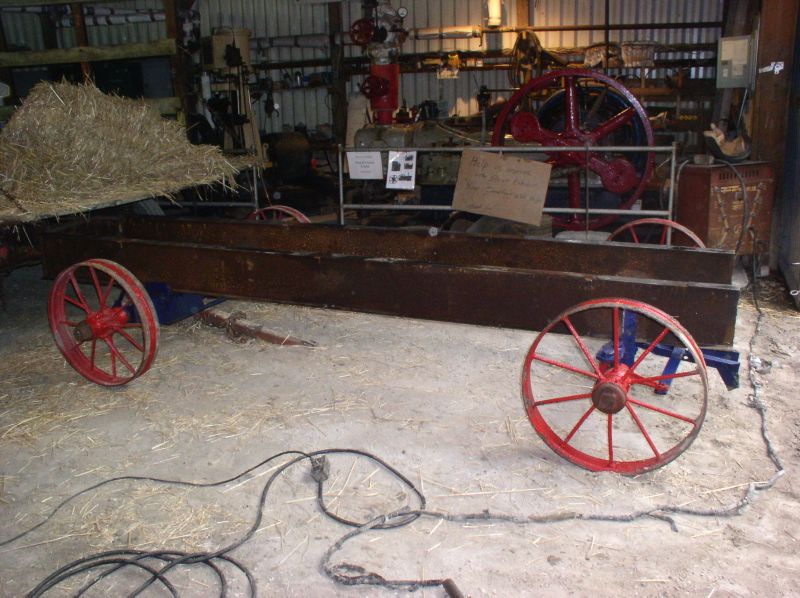
This was the first of many braces. I trust my welds. But I also trust some of the guys in the club. I trust that sooner or later one of them WILL hook a tractor to this thing, rip 'n snort and run it into a doorframe, post, tree, or other bit of machinery.
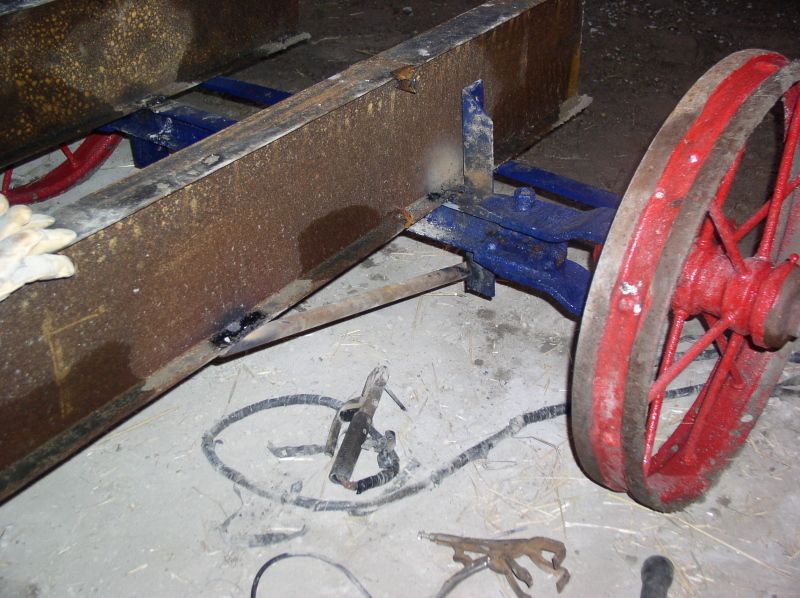
Since it was getting dark I had to stop there for the day. My last project before leaving was to flip the steering stuff over (I'd somehow managed to mount it upside down!) Luckily that was a 5 minute deal. One big bolt from the pivot, a kotter pins at each end of the tie rod, and turn it all over as a unit. By golly, if it didn't fit even better than it had the other way!
Then we rolled it outside in the rain so nobody could complain that it was in the way.
We had 3 nice days this past week, so I made a lot of progress on this.
I was warned that due to the thin material, mobile home I-beams don't have a lot of side strength. So first I added two vertical X braces made from 3/4" Schedule 80 pipe to help hold the beams square. Since the big pump will be centered over the rear axle, I also put on a pair of braces on the outer stubs to help keep the axle from springing
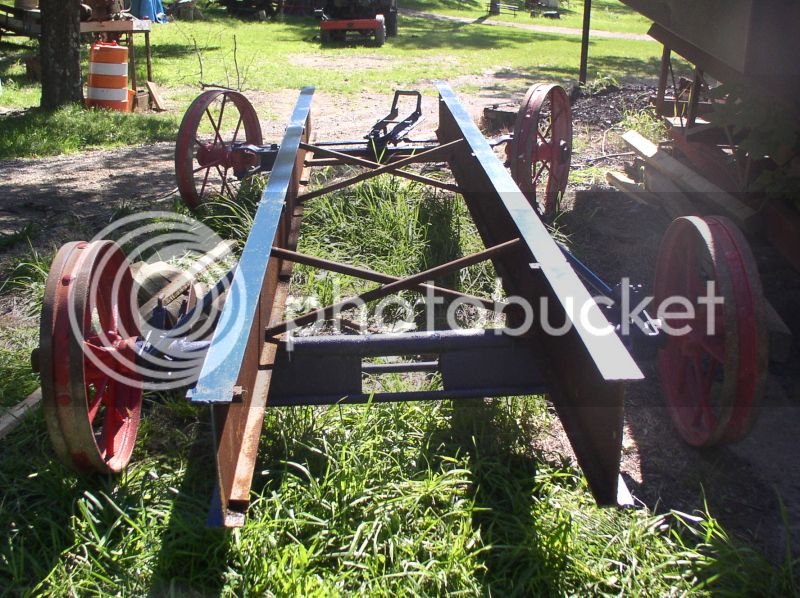
There was this angled flange on the rear axle, so I decided it was a really good place to attach a horizontal diagonal to help keep the frame from going diamond shape... It looks sort of like a panhard bar.
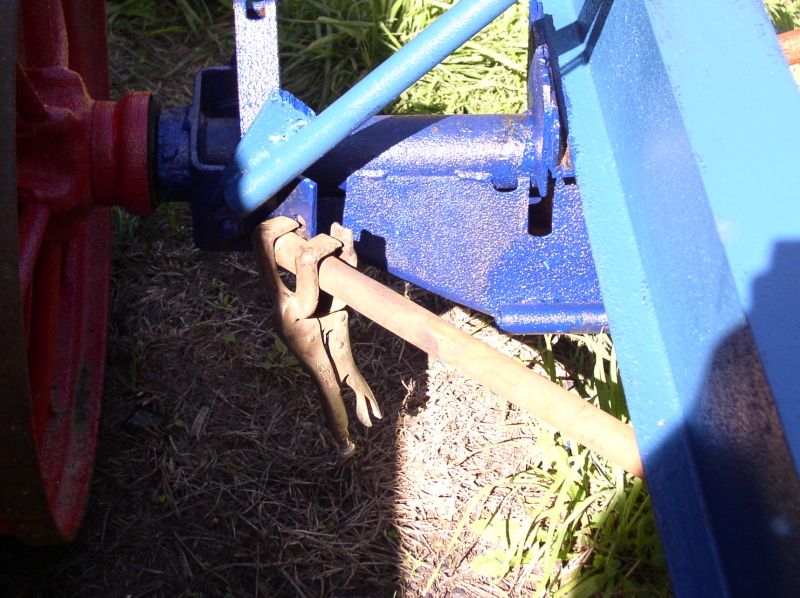
Since the axle attach point was a little below the bottom I-beam flange, it allowed me to run the other diagonal flat and tie them together.
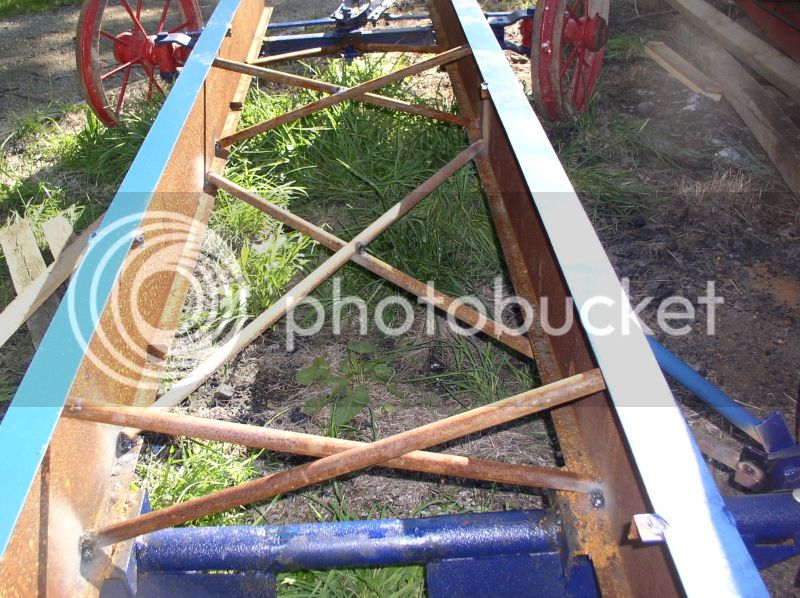
I then decided I probably needed to put something across the rear for strength and to help minimize the chances of someone punching the end of the beams through a building.
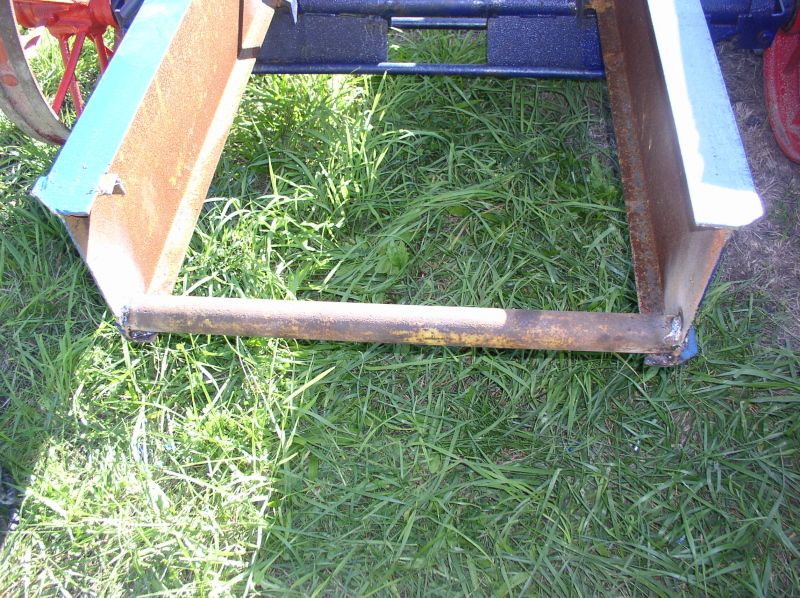
Sadly, I ran out of the real pretty dark blue and couldn't find more, but a local odd lot store had this other "dark" blue on sale for $4 a quart... so far I've used 2 quarts.
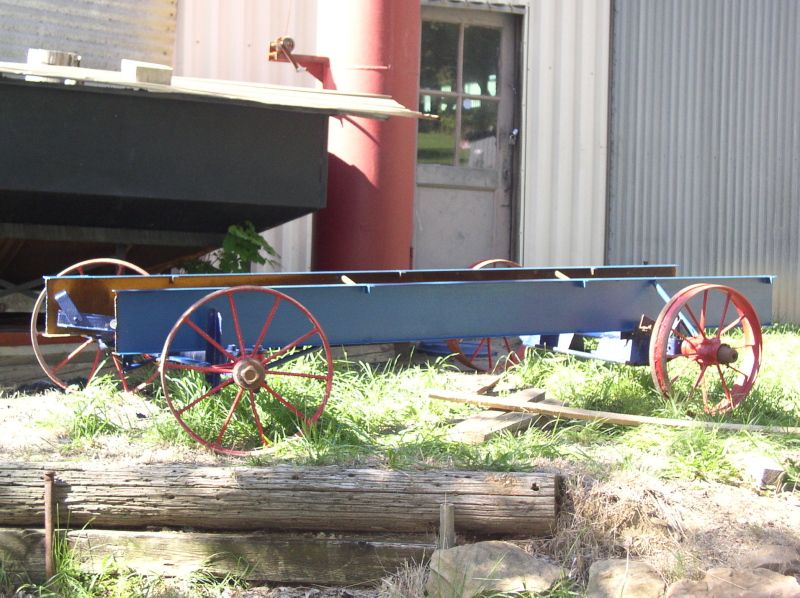
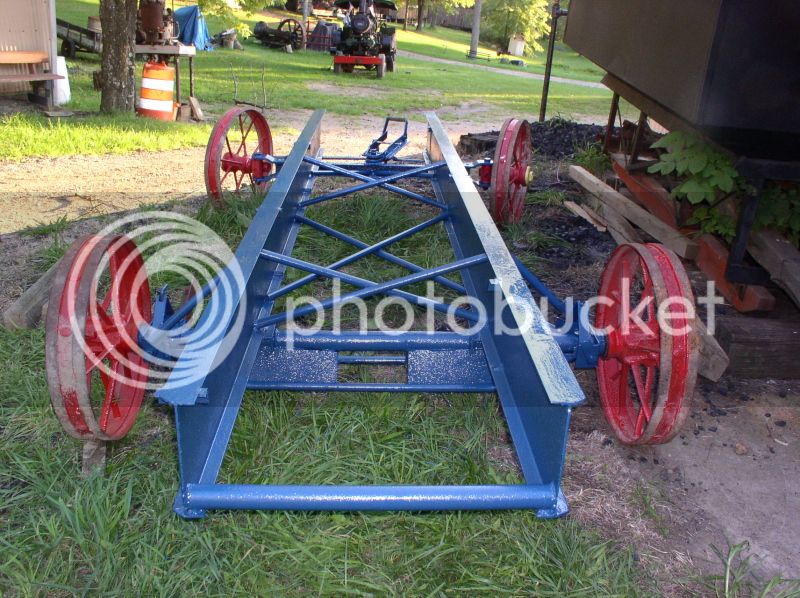
The big pump got brought up out of the weeds. It's 5 feet long, and the wagon is 12.... the other pumps will get mounted crosswise.
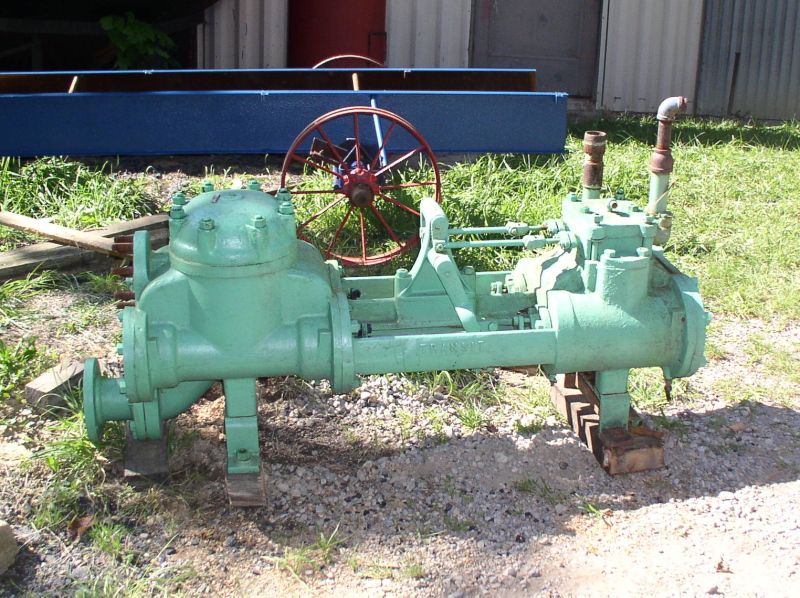
I was going to salvage the oak skids to place crosswise to mount the pump on ... but, while they still looked good on top, they're kind of punky underneath. So I'll have to see if I can find some used channel.
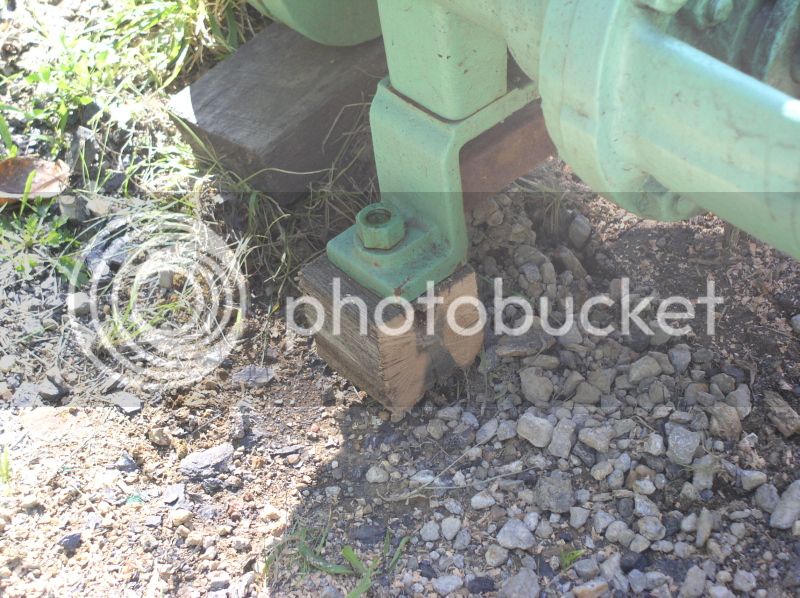
Some fat guy at work....
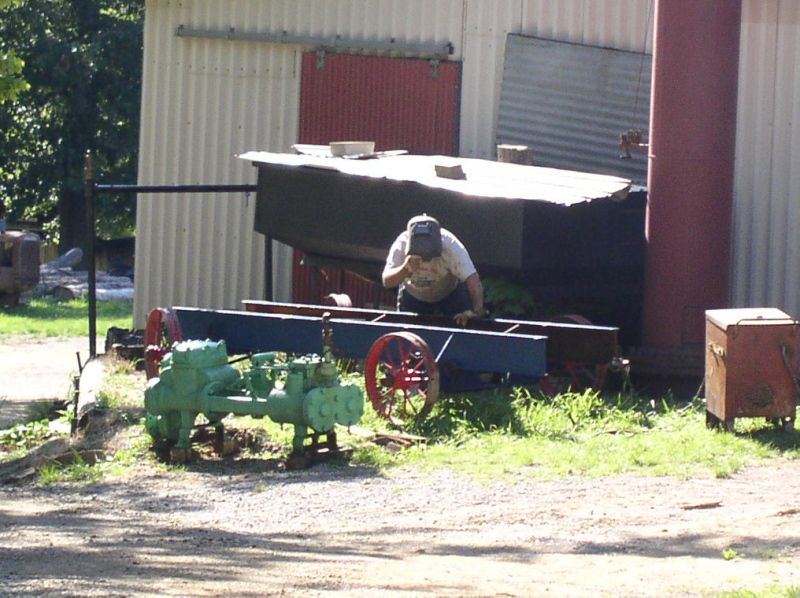
The wagon itself is pretty much done except for the tongue. It ain't fancy, but it should keep the pumps out of the mud for a bit.
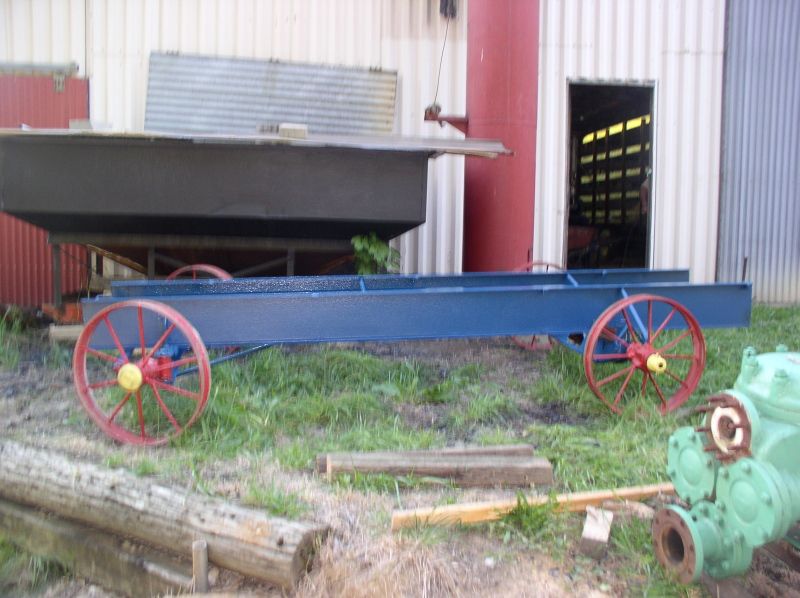