- Joined
- Mar 13, 2012
- Messages
- 583
- Reaction score
- 62
Hi Ralph, you have touched on something that took me a long time to come to grips with 
I once though that the beauty of cast iron parts was their naturally rough surface finish. When I did my PM #3, I worked really hard not to disturb that finish with any accidental machining marks because I though it would look great once painted. However, when I was done with the painting, I was incredibly disappointed with the results. It looked like a cheap toy, not a model of a real engine. It took some time, but I finally realized that what I didn't like was that the surface was too rough for the scale of the engine.
If you look at a full scale engine from 20 feet away, the surface does not look very rough, so I don't think a 1/20th scale model should look rough from 1 foot away.
I don't think the cast iron look comes from the rough surface. The recent Waller and Benson builds from bar stock that were shown on this site prove that.
http://www.homemodelenginemachinist.com/index.php?topic=16453.0
http://www.homemodelenginemachinist.com/index.php?topic=18153.0
What makes something look cast is the complexity of the shape, the draft, and the natural fillets that occur. If you doubt this, take a look at these two pictures. One is the cylinder which I have not touched yet, and the other is the frame.
How would the cylinder look with a coat of paint? Is there any doubt in your mind that the fame was cast?
I once though that the beauty of cast iron parts was their naturally rough surface finish. When I did my PM #3, I worked really hard not to disturb that finish with any accidental machining marks because I though it would look great once painted. However, when I was done with the painting, I was incredibly disappointed with the results. It looked like a cheap toy, not a model of a real engine. It took some time, but I finally realized that what I didn't like was that the surface was too rough for the scale of the engine.
If you look at a full scale engine from 20 feet away, the surface does not look very rough, so I don't think a 1/20th scale model should look rough from 1 foot away.
I don't think the cast iron look comes from the rough surface. The recent Waller and Benson builds from bar stock that were shown on this site prove that.
http://www.homemodelenginemachinist.com/index.php?topic=16453.0
http://www.homemodelenginemachinist.com/index.php?topic=18153.0
What makes something look cast is the complexity of the shape, the draft, and the natural fillets that occur. If you doubt this, take a look at these two pictures. One is the cylinder which I have not touched yet, and the other is the frame.
How would the cylinder look with a coat of paint? Is there any doubt in your mind that the fame was cast?
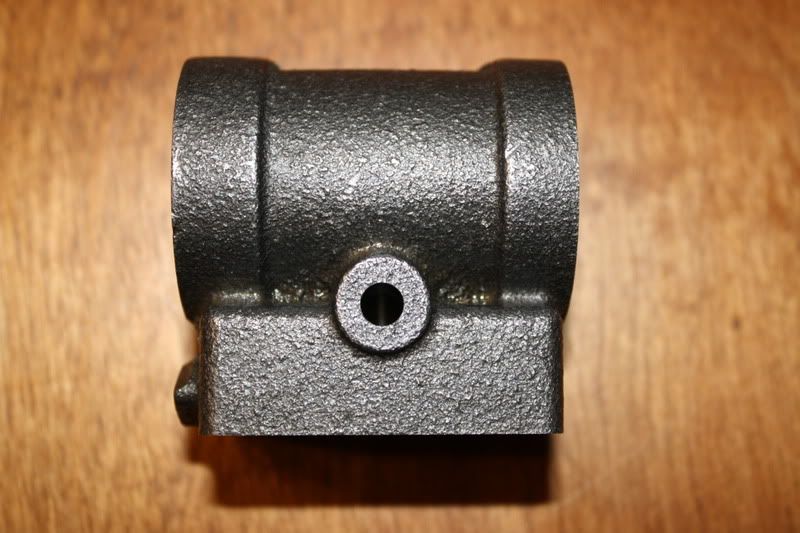
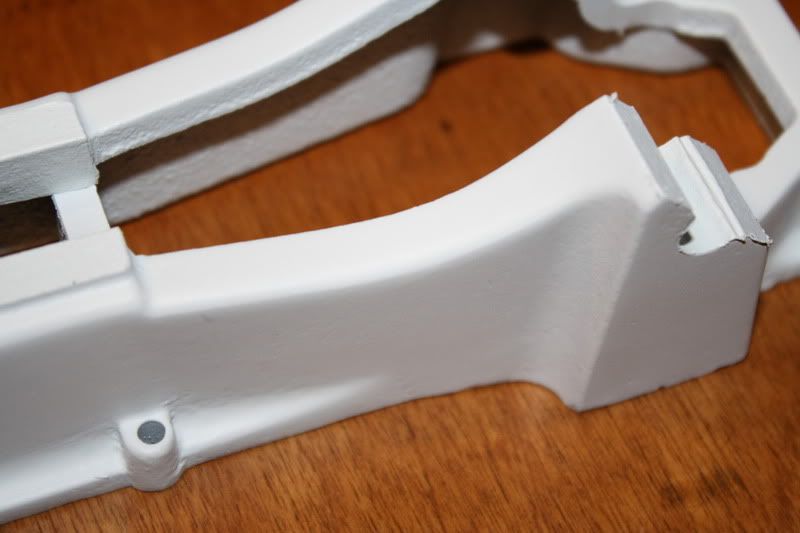