I made the cutter out of an old broken 1/4" endmill. Then put the radius in on the milling machine. The part is sitting on top of a couple of parallels.
Here's a pic showing how the flywheel sits against this part. At the end the screws will be covered with filler and paint.
That's it for now
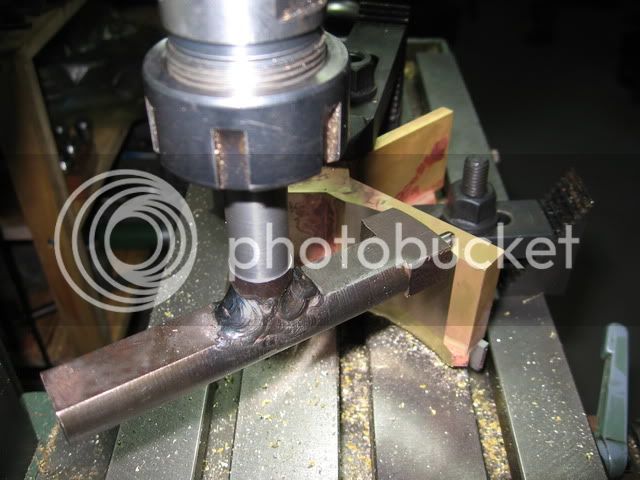
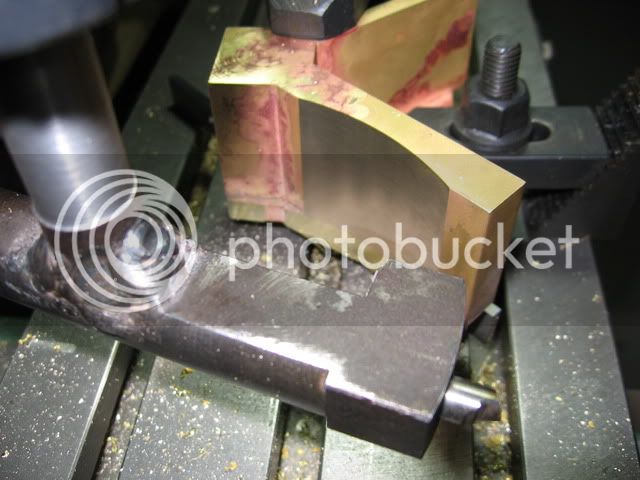
Here's a pic showing how the flywheel sits against this part. At the end the screws will be covered with filler and paint.
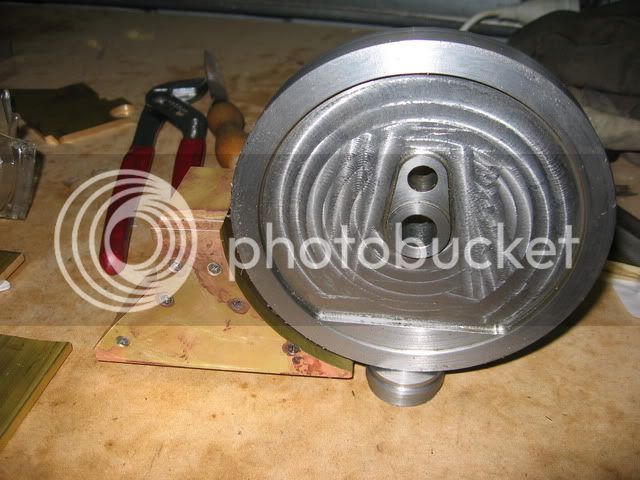
That's it for now